The dairy industry faces the challenge of maintaining high-quality standards while keeping production lines running efficiently. With equipment working constantly, skipping maintenance tasks can lead to costly downtimes, lower product quality, and safety risks. Ensuring regular maintenance is crucial to avoid disruptions and maintain smooth operations.
This article highlights the essential routine maintenance tasks in the dairy industry and how they contribute to effective dairy maintenance management. From cleaning milking machines to maintaining cooling systems, we’ll cover key tasks that help improve efficiency, reduce costs, and extend the life of equipment.
Importance of Dairy Maintenance Tasks
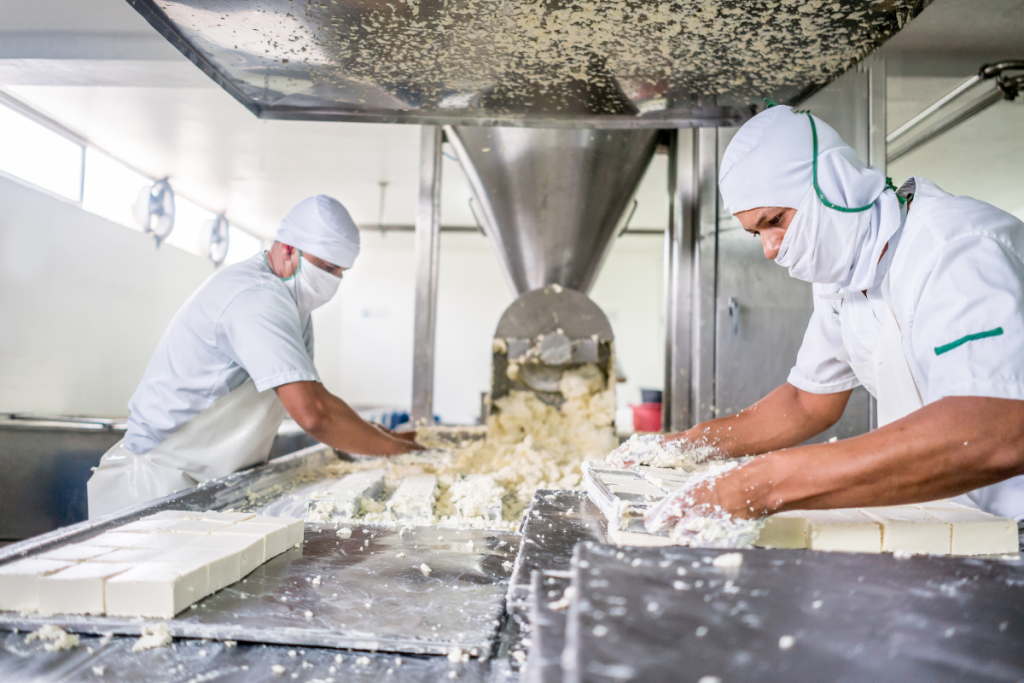
The dairy industry relies heavily on equipment like pasteurizers, milking machines, refrigeration systems, and pumps. If these systems break down, even for a short period, it can disrupt the entire production cycle. Routine maintenance tasks for dairy are designed to identify potential issues before they cause significant problems, ensuring that dairy products meet quality standards and are produced without delays.
A proactive approach, such as preventive maintenance for dairy, can help identify wear and tear early on, extend the lifespan of machinery, and reduce the likelihood of unexpected breakdowns. This methodical approach to dairy maintenance management has become a critical part of daily operations in dairy plants around the world.
- Regular maintenance prevents costly breakdowns.
- Ensures consistent product quality and safety.
- Minimizes production downtime and interruptions.
- Extends the lifespan of expensive equipment.
- Reduces the risk of contamination during milk collection and processing.
- Helps comply with health and safety regulations.
- Improves energy efficiency and lowers operating costs.
- Reduces the need for expensive emergency repairs.
- Boosts overall operational efficiency.
- Improves staff safety by ensuring equipment is in good working condition.
Key Routine Maintenance Tasks in the Dairy Industry
Maintaining dairy equipment is essential to ensuring smooth production and high-quality products. Regular maintenance tasks not only prevent equipment failure but also optimize the efficiency of operations. These tasks vary depending on the machinery, but all are vital for keeping systems running at their best.
Below are the key maintenance tasks for dairy that help to keep the production process uninterrupted and efficient.
1. Regular Inspection and Cleaning of Milking Equipment
Milking machines are central to dairy production, and any malfunction can cause a halt in milk collection. Regular inspections are vital to ensure the machines are functioning efficiently. Maintenance tasks for dairy include cleaning milking machines thoroughly to avoid bacterial growth and potential contamination of milk. These systems need to be checked for wear, with specific attention to pumps, vacuum systems, and hose connections.
A typical routine inspection might involve:
- Checking for leaks or cracks in pipes
- Ensuring proper functioning of the vacuum pump
- Lubricating moving parts
- Cleaning and disinfecting the milking system
These dairy maintenance tasks help in reducing downtime and maintaining milk hygiene standards.
2. Preventive Maintenance for Cooling Systems
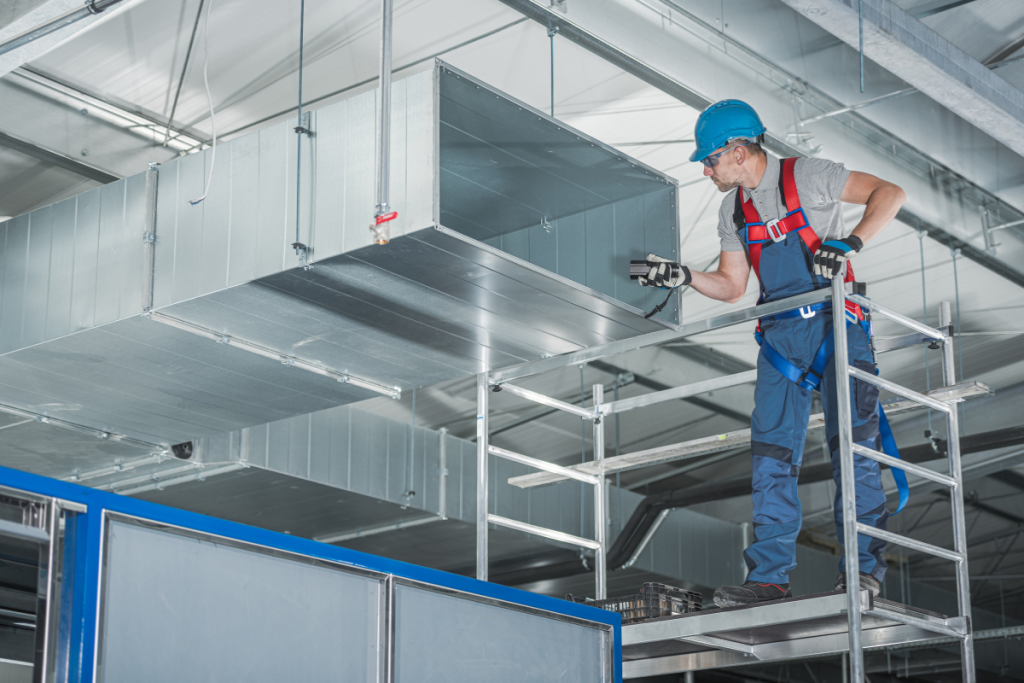
Cooling is critical in the dairy industry to ensure milk and other dairy products stay fresh. Refrigeration units, cooling tanks, and storage facilities must undergo regular inspections and maintenance to prevent equipment failures, which could result in product spoilage.
The maintenance task for dairy involves:
- Cleaning condenser coils and evaporators to ensure optimal heat exchange
- Checking refrigerant levels and replacing fluids when necessary
- Inspecting insulation for wear and tear
- Verifying temperature controls are functioning correctly
Routine checks ensure these systems are working efficiently, reducing energy consumption and preventing costly repairs due to neglected issues.
3. Routine Cleaning and Sanitizing of Processing Equipment
Dairy processing involves several stages—pasteurization, homogenization, and packaging—all of which require specialized equipment. Maintaining hygienic conditions is paramount. Dairy maintenance tasks for processing equipment include regular sanitizing to prevent contamination and maintain the quality of dairy products.
- Regular cleaning schedules for pasteurizers and homogenizers
- Calibrating temperature control systems to ensure milk reaches the desired pasteurization temperature
- Checking valves, pipes, and tanks for leaks or contamination risks
These tasks are essential to maintain the quality of dairy products and avoid production stoppages.
4. Monitoring and Maintaining Water Systems
Water is a vital resource in dairy production, used in cleaning, cooling, and processing. A failure in water systems can halt operations. Routine maintenance tasks for dairy water systems include:
- Regular cleaning of water tanks and filters
- Checking for leaks or cracks in the pipes
- Testing water quality to ensure it meets industry standards
Keeping water systems in good condition is crucial for hygiene, machine efficiency, and overall operational productivity.
5. Inspecting and Replacing Worn-Out Seals and Gaskets in Machinery
Worn-out seals and gaskets can lead to leaks, contamination, and inefficiencies in dairy equipment. Regular inspection and replacement of these components are vital to maintain the integrity of systems, especially in pasteurizers, pumps, and refrigeration units. Routine tasks include:
- Inspecting seals and gaskets for cracks or wear.
- Replacing damaged seals to prevent leaks and product contamination.
- Ensuring that the new seals are correctly fitted to maintain optimal performance.
- Monitoring for any unusual vibrations or sounds that may indicate seal failure.
6. Regular Checks and Maintenance of Refrigeration Units
Refrigeration is essential for preserving dairy products, and any malfunction can result in product spoilage. Maintaining refrigeration units ensures temperature stability and energy efficiency. Regular maintenance tasks for refrigeration include:
- Cleaning condenser coils to prevent blockages that could affect cooling efficiency.
- Checking refrigerant levels to ensure proper functioning and avoid overheating.
- Inspecting door seals to prevent temperature fluctuations and energy waste.
- Ensuring the thermostat is calibrated correctly to maintain the desired temperature.
- Checking for leaks in refrigerant lines that could lead to a loss of cooling performance.
Benefits of Preventive Maintenance for Dairy
Preventive maintenance helps address minor issues before they develop into significant problems, ensuring that dairy operations stay productive and efficient. Implementing an effective dairy maintenance management system offers several benefits:
- Reduced downtime: Scheduled maintenance minimizes the risk of unexpected breakdowns.
- Extended equipment lifespan: Regular checks and repairs increase the longevity of expensive machinery and equipment.
- Improved product quality: Proper maintenance prevents contamination and ensures the smooth operation of production lines, maintaining milk quality.
- Cost savings: Preventive maintenance reduces repair costs and avoids emergency call-outs, which can be expensive and disruptive.
Best Practices for Routine Dairy Maintenance Management
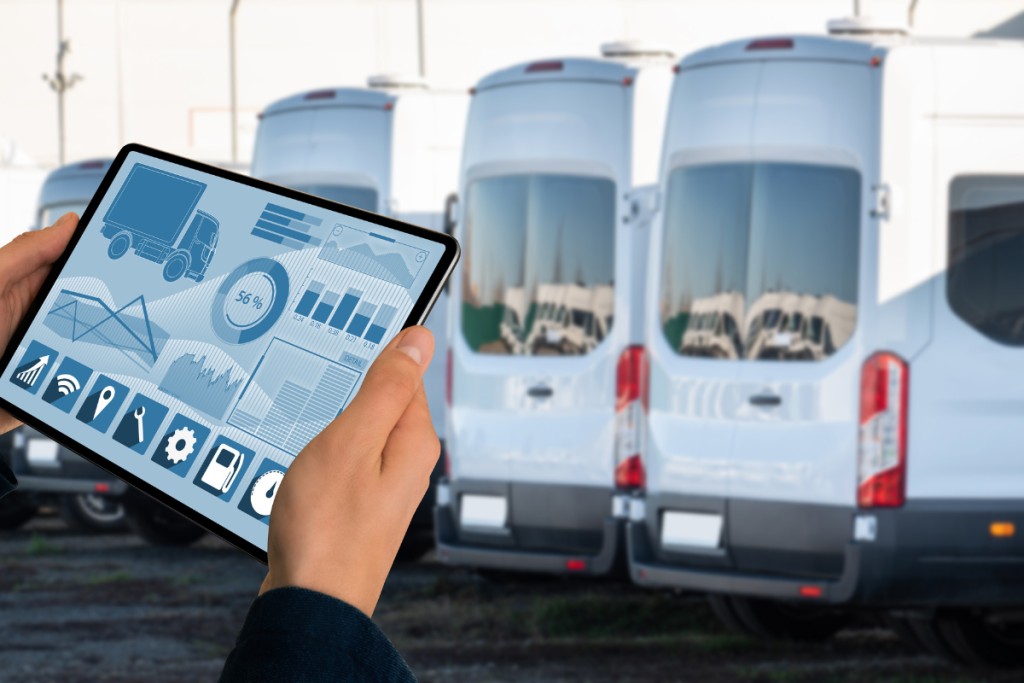
Effective dairy maintenance management relies on a structured approach that helps identify potential issues before they disrupt production. Regularly scheduled maintenance, coupled with detailed record-keeping, ensures that equipment stays in optimal working condition. A proactive system of monitoring and repairs can significantly extend the lifespan of dairy machinery, improving overall operational efficiency and reducing costs.
Utilizing technology and data-driven decisions can further improve the maintenance process. Maintenance software systems can track equipment usage, performance, and upcoming maintenance tasks, allowing dairy managers to plan effectively. A focus on continuous staff training ensures everyone is equipped to identify issues early and follow maintenance protocols properly.
- Implement a preventive maintenance schedule for all critical equipment.
- Track maintenance activities and keep detailed records for future reference.
- Regularly assess equipment performance to identify potential problems.
- Ensure prompt repairs to minimize downtime and maintain efficiency.
- Create a checklist for routine inspections to standardize maintenance tasks.
- Implement a condition-based monitoring system that uses sensors to detect early signs of wear and tear in equipment.
- Ensure that all safety valves, pressure gauges, and temperature controls are calibrated regularly to prevent over-pressurization or overheating.
- Perform vibration analysis on motors and pumps to detect potential mechanical failures before they lead to a breakdown.
- Use infrared thermography to detect overheating electrical components and prevent electrical failures.
- Develop a thorough cleaning and maintenance schedule for automated milking systems to ensure consistent milk quality and avoid bacterial contamination.
- Schedule regular tank inspections to check for scale buildup or corrosion, which can affect milk quality and refrigeration efficiency.
- Use ultrasonic testing to check for cracks or defects in storage tanks or pipelines that are not visible to the naked eye.
- Replace oil and lubricants in motors, compressors, and other machinery as per the manufacturer’s guidelines to maintain smooth operation and prevent excessive wear.
- Install backflow prevention devices in water systems to protect against contamination from external sources.
- Maintain proper documentation of parts inventory to ensure quick replacements during unexpected failures.
Putting it to the end
Ensuring your dairy operations run seamlessly goes beyond having the right equipment—it’s about staying on top of maintenance to prevent costly disruptions. Small tasks today can save you from bigger issues tomorrow. If you’re looking to optimize your dairy maintenance or need expert advice, we’re here to help. Reach out to us at contact@terotam.com and let’s discuss how we can enhance your maintenance strategy.