Why Does Your Business need IoT based Predictive Maintenance?
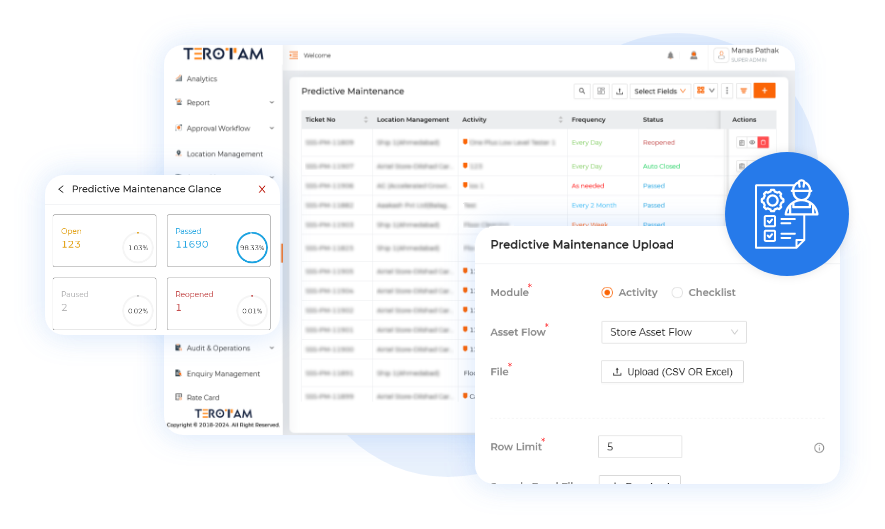
Conventional maintenance strategies, such as reactive and preventive methods, are no longer sufficient for today’s industrial requirements. Reactive maintenance results in unplanned equipment failures that disrupt production and increase downtime costs. Preventive maintenance, while more proactive, often involves servicing equipment unnecessarily, leading to wasted resources and missed optimization opportunities.
IoT for Predictive Maintenance leverages real-time sensor data and advanced analytics to continuously monitor key equipment parameters, such as temperature, pressure, and vibration. With machine learning algorithms analyzing this data, businesses can predict failures before they happen and schedule maintenance precisely when it’s needed. This proactive approach enhances asset reliability, reduces downtime, and extends the lifespan of critical equipment. The combination of IoT, cloud computing, and predictive analytics ensures smarter, data-driven decisions that improve overall operational efficiency and reduce maintenance costs.
Centralized Equipment Monitoring
Track and manage all your machinery through a single platform that provides real-time visibility into equipment performance. This system ensures timely responses to emerging issues, reducing downtime and maintaining operational continuity. With constant monitoring, you can improve both efficiency and asset management.
IoT sensors capture crucial data like temperature and pressure continuously, enabling proactive tracking of equipment health and performance.
Easily access the centralized dashboard from any device, allowing you to monitor equipment and respond to alerts from anywhere, ensuring seamless operations.
The IoT platform integrates with your existing machinery and software, enabling smooth adoption without the need for significant operational changes.
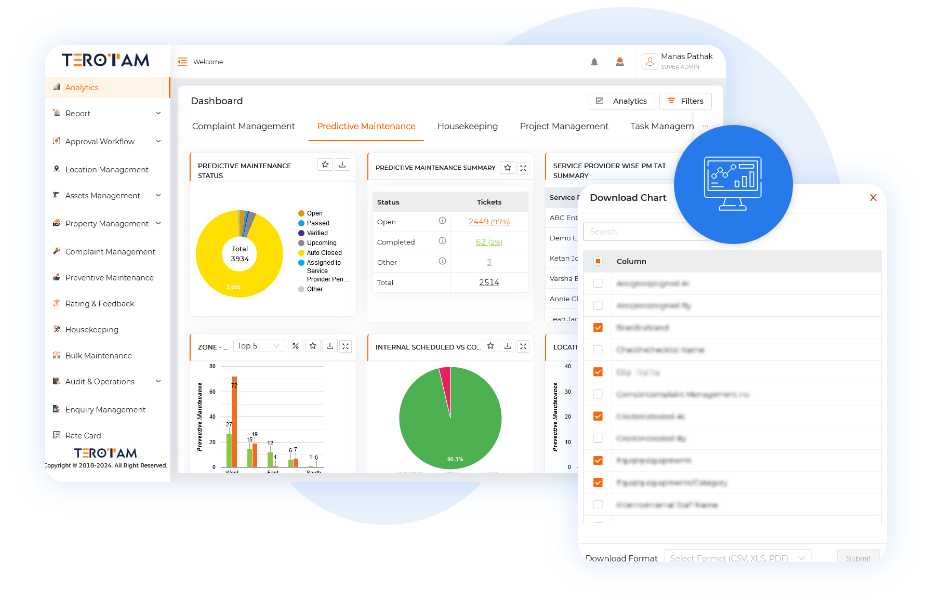
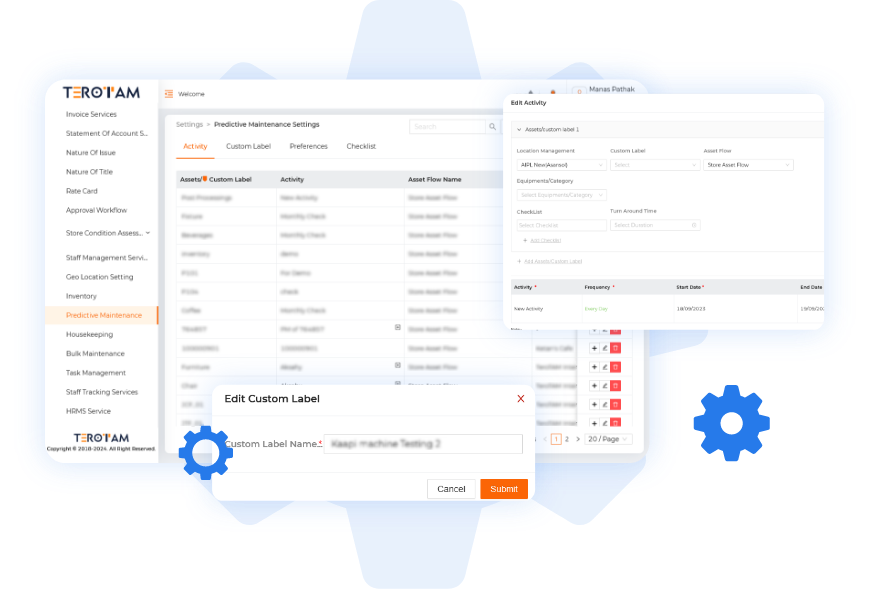
Automated Maintenance Scheduling
Automate maintenance workflows to avoid unnecessary repairs and keep equipment running at optimal performance levels. This reduces manual scheduling errors and ensures maintenance happens only when needed, saving time and costs. The system helps extend the lifespan of your machines while reducing maintenance-related downtime.
Work orders are automatically generated and assigned to technicians, eliminating delays and ensuring prompt responses to potential issues.
Real-time alerts notify teams of abnormal equipment performance, allowing quick action to prevent disruptions and minimize maintenance costs.
Maintenance windows are forecasted based on equipment health data, ensuring service is scheduled at the optimal time, preventing unnecessary downtime.
Advanced Analytics and Predictive Insights
Leverage the power of advanced analytics to predict equipment failures and fine-tune maintenance schedules for optimal performance. With features like energy monitoring and vibration analysis, the system identifies key trends and patterns, providing actionable insights to enhance operational efficiency. These predictive insights allow businesses to address potential issues before they escalate, ensuring smoother workflows and reduced downtime.
Use real-time and historical data, including energy consumption and vibration readings, to forecast potential equipment issues and schedule maintenance effectively.
Monitor equipment behavior to identify patterns that lead to failures, allowing for solutions that address underlying problems and improve uptime.
Generate tailored reports that track key metrics such as energy use, vibration levels, repair costs, and overall performance, providing clear insights into operations.
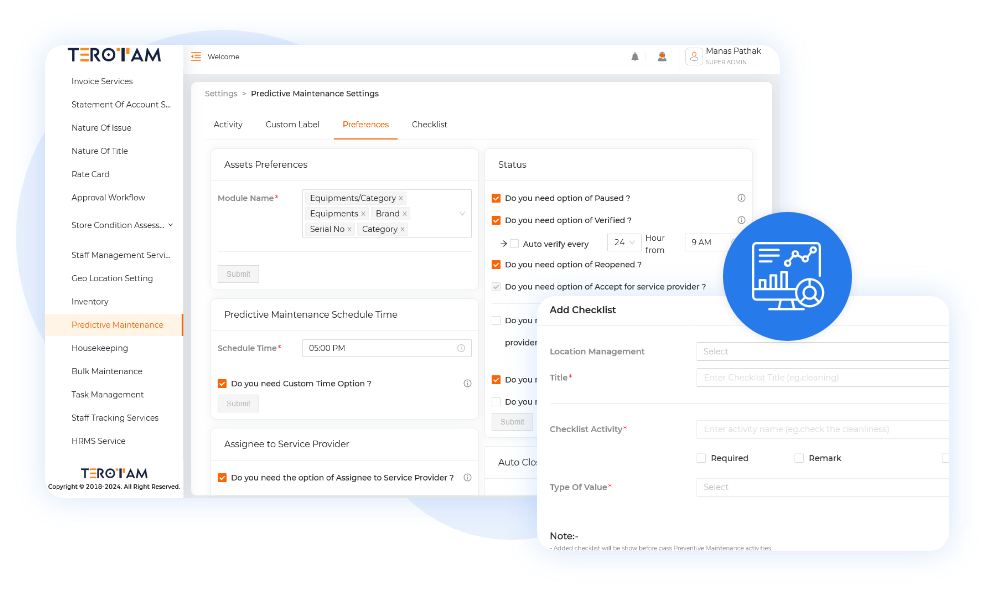
Ready to Transform Your Maintenance Process?
Explore how IoT can enhance your predictive maintenance strategies and minimize unexpected downtimes.
Mobile-Enabled IoT Predictive Maintenance
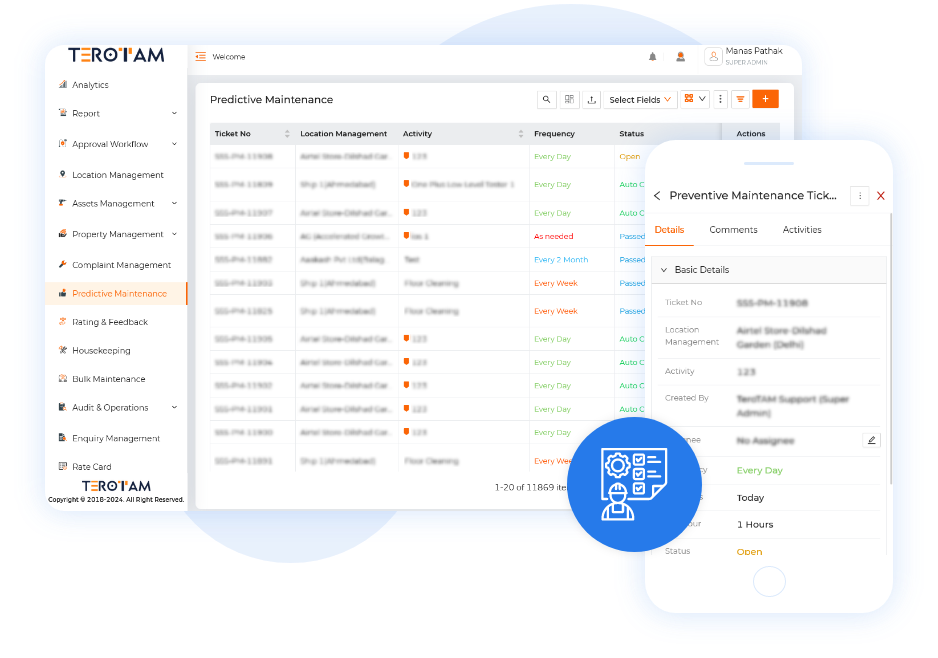
Manage and monitor maintenance activities on the go with our mobile app. Stay informed and take quick action through real-time alerts and diagnostics available on your smartphone.
Access live equipment data from anywhere
Assign maintenance tasks to technicians remotely
Track work orders and receive updates instantly
Easily upload photos, documents, or maintenance checklists to better communicate issues
Key Features of IoT Based Predictive Maintenance
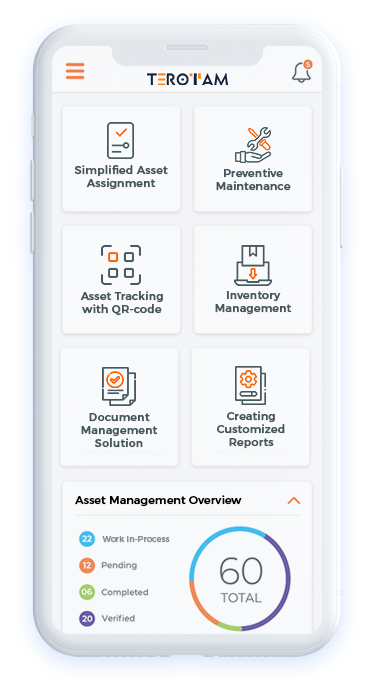
Industries We Serve

Maintenance

Education
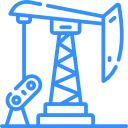
Oil & Gas

Real Estate

Banking

Equipment

Healthcare

Non-Profit

Government

Fire Department/EMS

Hotels
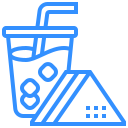
Food & Beverage
Do you have questions?
We know the most obvious doubts one has in mind while thinking of Asset Management Solution. Check out FAQs and unravel your doubts.
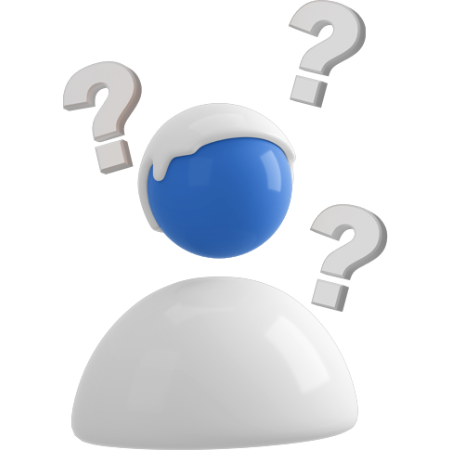
What is IoT for Predictive Maintenance?
IoT for Predictive Maintenance refers to using Internet of Things (IoT) devices and advanced analytics to monitor equipment health, predict failures, and optimize maintenance schedules to reduce downtime and maintenance costs.
Can IoT solutions integrate with my existing systems?
Yes, IoT solutions for predictive maintenance can be seamlessly integrated with your existing equipment and software, offering flexibility and compatibility with a range of platforms.
How can I measure the success of my predictive maintenance program?
Success can be measured using KPIs such as reduced downtime, improved equipment reliability, maintenance cost savings, and increased overall equipment effectiveness (OEE).
What types of sensors are commonly used in IoT predictive maintenance?
Common sensors include vibration sensors, temperature sensors, humidity sensors, acoustic sensors, and energy meters. These devices collect critical data to monitor equipment conditions effectively.
What challenges can arise when implementing IoT for predictive maintenance?
Common challenges include data integration from multiple sources, ensuring data quality, managing cybersecurity risks, and training staff to effectively use new technologies.