When it comes to keeping machines and equipment in good shape, most businesses don’t want to wait for things to break. That’s why traditional maintenance strategies have evolved from fixing problems after they happen to preventing them before they even start. And now, we’re stepping into a smarter, more data-driven stage: prescriptive maintenance.
Prescriptive maintenance doesn’t just tell you that a machine might fail soon. It tells you exactly what to do about it and when. It’s like having a virtual maintenance expert who not only spots problems early but also offers a plan to fix them before they impact operations.
So, what makes prescriptive maintenance stand out? How does it actually work? And how can you implement it in your business without overcomplicating your workflow? Let’s break it all down.
What is prescriptive maintenance?
Prescriptive maintenance (sometimes shortened to RxM) is the most advanced form of maintenance strategy. It uses data, machine learning, and predictive analytics to recommend the best course of action when something in your equipment seems off.
It goes a step further than predictive maintenance. While predictive maintenance might say, “This motor is likely to fail in two weeks,” prescriptive maintenance adds, “Reduce the load by 15%, schedule a service in five days, and replace the part if vibration levels remain high.”
In short, it:
- Predicts potential issues.
- Analyses different possible actions.
- Recommends the most effective solution based on real-time data.
Why should businesses care about it?
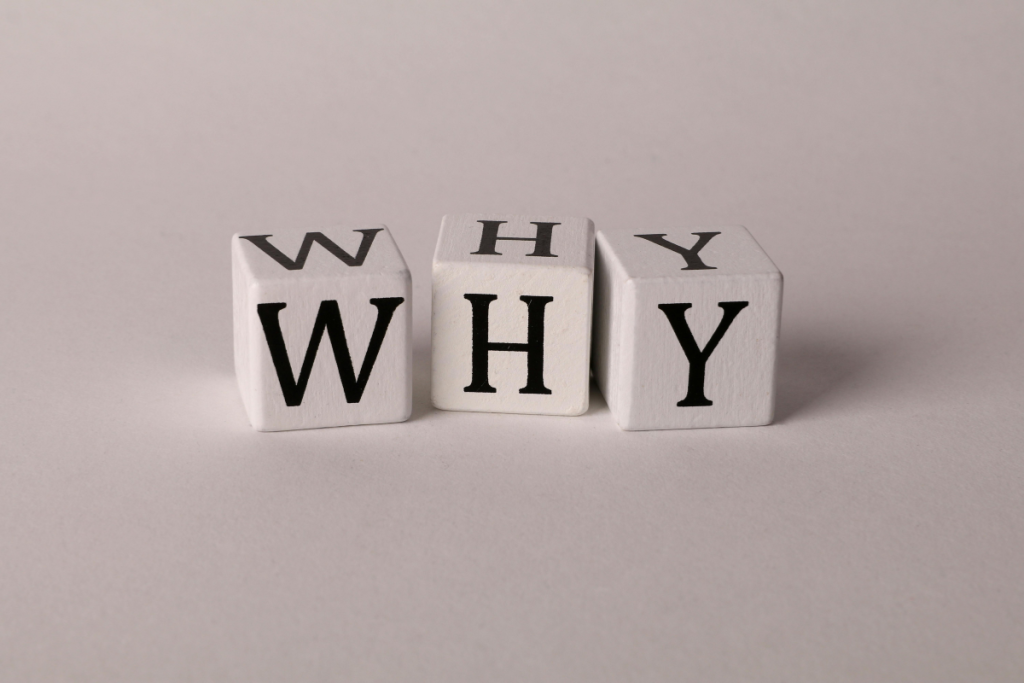
Prescriptive maintenance isn’t just for large factories with massive budgets. Even small and medium businesses can benefit from it, especially if they rely on machinery or equipment for day-to-day operations.
Here’s what makes it useful:
1. Fewer unplanned breakdowns
By predicting what might go wrong and giving clear advice, it helps you avoid sudden shutdowns and panic-driven repairs.
2. Optimised maintenance schedules
Instead of doing maintenance too often (or too late), prescriptive maintenance recommends service only when needed, saving time and money.
3. Extended equipment life
Taking timely action can prevent unnecessary wear and tear, helping you get more years out of your machines.
4. Data-backed decision-making
It takes the guesswork out of the equation. You’re not just hoping a repair will work you’re following a well-informed plan.
5. Lower operating costs
Fewer failures mean less money spent on emergency repairs, replacements, and downtime.
How does prescriptive maintenance work?
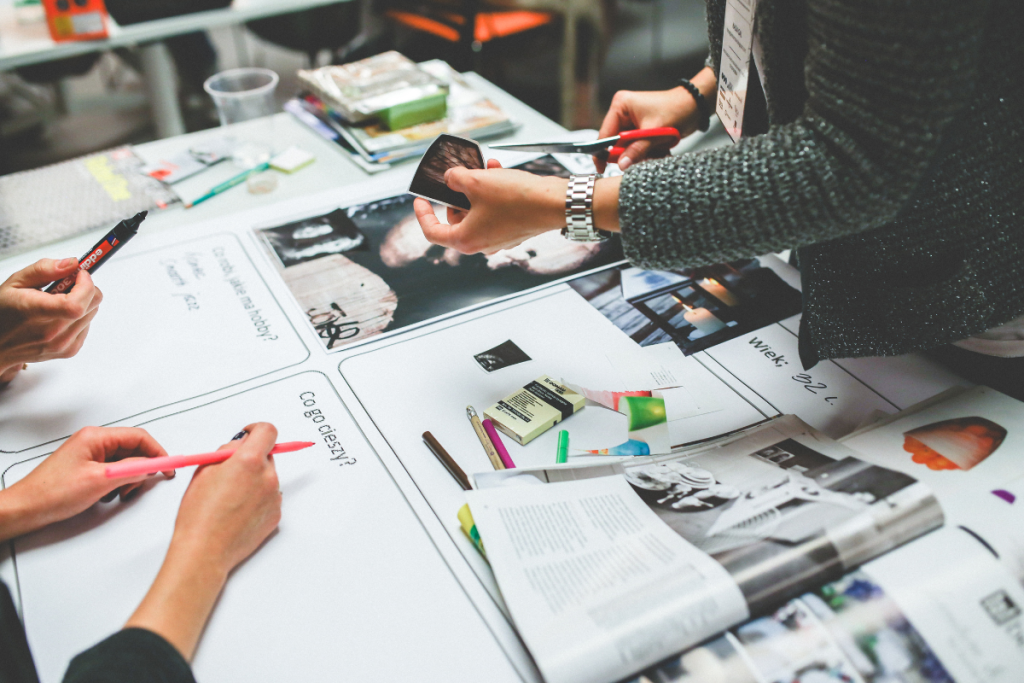
Prescriptive maintenance relies on a combination of technologies and methods that work together in a loop. Here’s how the cycle typically runs:
1. Data collection
Sensors on equipment capture real-time data like temperature, vibration, noise, pressure, and more. Historical data is also pulled in from past maintenance logs.
2. Data analysis
Advanced analytics software processes all the incoming data, identifying patterns, anomalies, and signs of wear or stress.
3. Predictive modeling
Machine learning algorithms forecast potential failures by comparing the data to previous failure patterns.
4. Simulation of possible actions
The system runs different “what if” scenarios. For example, what if you shut the machine down now? What if you delay maintenance by a week?
5. Prescriptive output
Based on the simulations, the system recommends a specific action—whether it’s a repair, a part replacement, a load adjustment, or something else.
How to implement prescriptive maintenance in your business?
Shifting towards prescriptive maintenance can feel like a big leap, but with the right approach, it can be rolled out smoothly. The key is to move gradually, start small, track results, and build from there. Here’s a closer look at each step you should consider:
1. Assess your current maintenance strategy
Start by mapping out what kind of maintenance practices you’re currently following. Are your teams working reactively, or do you have a preventive schedule in place? Understanding this baseline helps you figure out what changes are needed and how ready your team is for a more advanced system.
2. Start with your most critical assets
Not every machine needs prescriptive maintenance from day one. Begin with the equipment that has the highest impact on production or safety. Focusing on these machines gives you quicker results and makes it easier to justify the investment across other departments.
3. Install sensors and IoT devices
For prescriptive maintenance to work, your machines need to communicate. Install sensors that track key data points like temperature, vibration, current flow, or pressure. Choose devices that suit each machine’s nature and operating conditions to get accurate readings.
4. Choose the right software platform
The software you pick will do the heavy lifting analyzing data and recommending actions. Look for a platform that’s user-friendly, supports machine learning, and fits into your existing ecosystem. It should offer real-time monitoring, customizable dashboards, and simple alert systems.
5. Connect your data sources
Feed your system with data from multiple touchpoints. Combine real-time sensor data with historical records such as past maintenance logs, failure history, and manufacturer guidelines. This combined data set strengthens the accuracy of recommendations.
6. Run pilot tests
Before deploying it everywhere, run a pilot on selected machines. Observe how the system performs, evaluate the suggestions it provides, and compare outcomes with your manual process. This phase helps you identify gaps and improve setup before scaling.
7. Train your maintenance team
Your team needs to understand what the system is telling them and why. Offer hands-on training to interpret the dashboards, alerts, and suggested actions. When the team feels confident with the system, they’re more likely to trust and follow it.
8. Measure results and scale up
Track the impact through metrics like downtime reduction, cost savings, and service efficiency. Use these insights to justify expansion. Gradually roll out the system across more machines and facilities, fine-tuning as you go.
Common challenges of prescriptive maintenance
Introducing prescriptive maintenance is a smart move, but it’s not without its hurdles. From technical setup to team adoption, several roadblocks can slow things down if not managed properly. Knowing what to expect and how to navigate it can help you avoid unnecessary delays or disappointments.
High initial investment
Setting up sensors, buying software, and onboarding a team can feel costly at first. To ease the financial load, start with a limited rollout. Proving ROI on a small scale helps make the case for broader implementation and secures internal support.
Data overload
It’s easy to collect more data than you can use. But raw data alone isn’t helpful unless you can turn it into action. Use software that can filter, prioritise, and simplify insights so your team only sees what actually matters.
Change resistance
New systems can face pushback from teams who are used to traditional ways of working. Make them part of the journey from day one explain the purpose, offer training, and show how it makes their job smoother, not harder.
Integration issues
Prescriptive maintenance platforms need to work well with your existing systems. If your current software or hardware is outdated, integration can hit snags. Choose platforms with open APIs and solid technical support to avoid compatibility issues.
Final thoughts
Prescriptive maintenance brings more clarity and control to your maintenance strategy. It helps businesses move away from guesswork, plan better, and reduce the stress of surprise breakdowns. The real value lies in staying ahead of problems and acting with confidence, supported by real-time data.
If you’re considering making this shift and need guidance or a solution tailored to your setup, reach out to our team at contact@terotam.com. We’ll help you explore the right path forward step by step.