FRACAS (Failure Reporting, Analysis, and Corrective Action System) is a systematic framework designed to improve the reliability and performance of industrial systems by addressing failures at their core. It integrates failure reporting, root cause analysis, and corrective actions into a continuous feedback loop, ensuring that maintenance tasks are data-driven and effectively aligned with operational goals. By systematically documenting failures, analyzing their root causes, and implementing targeted corrective measures, FRACAS minimizes unplanned downtime, reduces maintenance costs, and enhances overall asset reliability.
This guide delves into the technical components of FRACAS, demonstrating how its implementation can streamline maintenance processes, optimize resource allocation, and drive continuous improvement in high-demand industrial environments.
FRACAS – An Overview
FRACAS is a comprehensive approach used in maintenance management to track, analyze, and resolve failures that occur within a system or process. It includes the following stages:
- Failure Reporting: The initial step involves documenting every failure that occurs. This can include equipment breakdowns, safety issues, or performance deviations.
- Failure Analysis: Once failures are reported, the next phase involves analyzing the root causes of these failures, often using methods like root cause analysis (RCA), failure modes effects analysis (FMEA), or statistical tools.
- Corrective Action: The final step is to implement corrective actions to resolve the identified issues, preventing their recurrence. These actions may involve equipment adjustments, process improvements, or changes in maintenance procedures.
FRACAS is an ongoing cycle that emphasizes continuous improvement, ensuring maintenance operations are continually refined.
Key Components of FRACAS
FRACAS consists of three main components that enable organizations to manage and address failure-related issues effectively:
Failure Reporting:
Every failure, regardless of its size, is reported. These reports may come from operators, maintenance staff, or automated systems integrated into tools like Computerized Maintenance Management Systems (CMMS).
Information collected includes failure time, location, operating conditions, and other relevant data.
Failure Analysis:
After reporting, an in-depth analysis of the failure’s root cause is conducted. Tools like Root Cause Analysis (RCA) and Failure Modes and Effects Analysis (FMEA) help identify the underlying issues.
Statistical methods can also be applied to detect recurring failure patterns, aiding future decision-making.
Corrective Action:
Once the root cause is identified, corrective actions are put in place. These actions can include equipment modifications, changes to operational procedures, or adjustments to maintenance schedules.
Emphasis is placed on implementing preventive measures to avoid future failures, making FRACAS an essential component of continuous improvement.
The Importance of FRACAS in Enhancing Maintenance Tasks
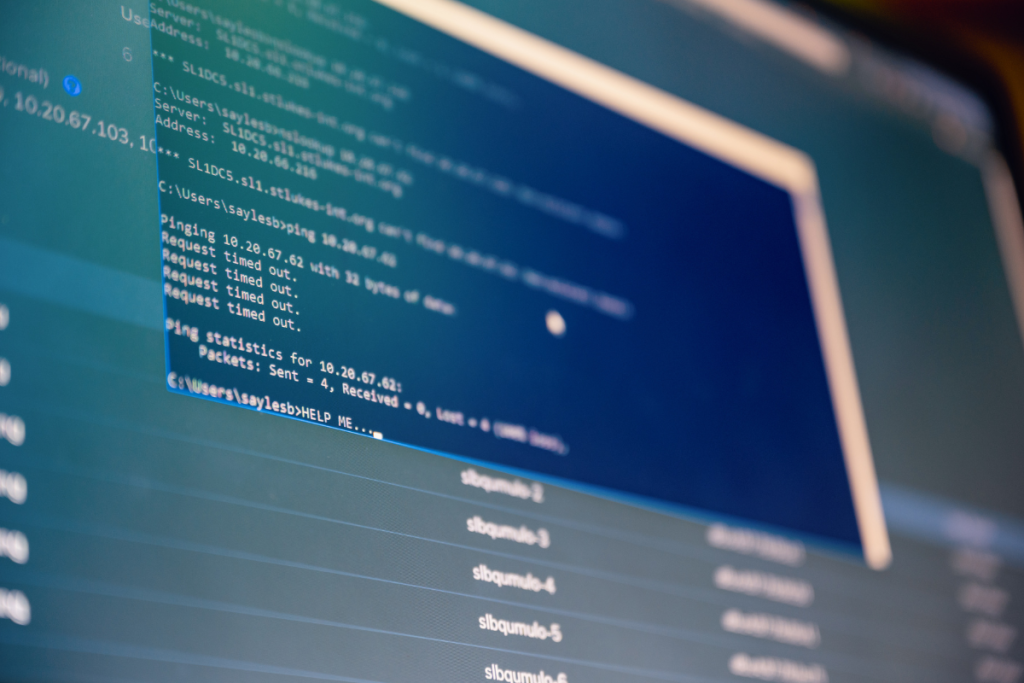
Minimizing Downtime and Improving Equipment Availability
FRACAS ensures failures are addressed comprehensively, not just temporarily fixed. This approach reduces unplanned downtimes, increasing equipment availability, which is vital in industries where continuous operations are critical.
Identifying and resolving root causes of failures reduces the frequency of breakdowns, thereby improving equipment uptime and operational efficiency.
Facilitating Data-Driven Decision Making
FRACAS collects detailed data about each failure, enabling organizations to make more informed decisions regarding maintenance strategies. This process facilitates:
- Predictive Maintenance: Recognizing failure patterns allows for a shift from reactive to proactive maintenance, anticipating issues before they become critical.
- Better Maintenance Planning: Understanding failure trends enables better planning of preventive and predictive maintenance tasks, reducing unscheduled maintenance.
Reducing Maintenance Costs
FRACAS helps identify and eliminate inefficient maintenance practices. Preventing recurring failures means fewer repairs and replacements, ultimately lowering maintenance costs.
Moreover, the data collected can inform better spare parts management, reducing excess inventory while ensuring critical parts are available when needed.
Continuous Improvement of Maintenance Processes
FRACAS encourages an ongoing process of learning and refinement. The system doesn’t merely fix failures—it ensures that each failure leads to valuable insights that can improve future maintenance practices, resulting in a stronger, more efficient maintenance environment.
How FRACAS Fits Into the Broader Maintenance Strategy?
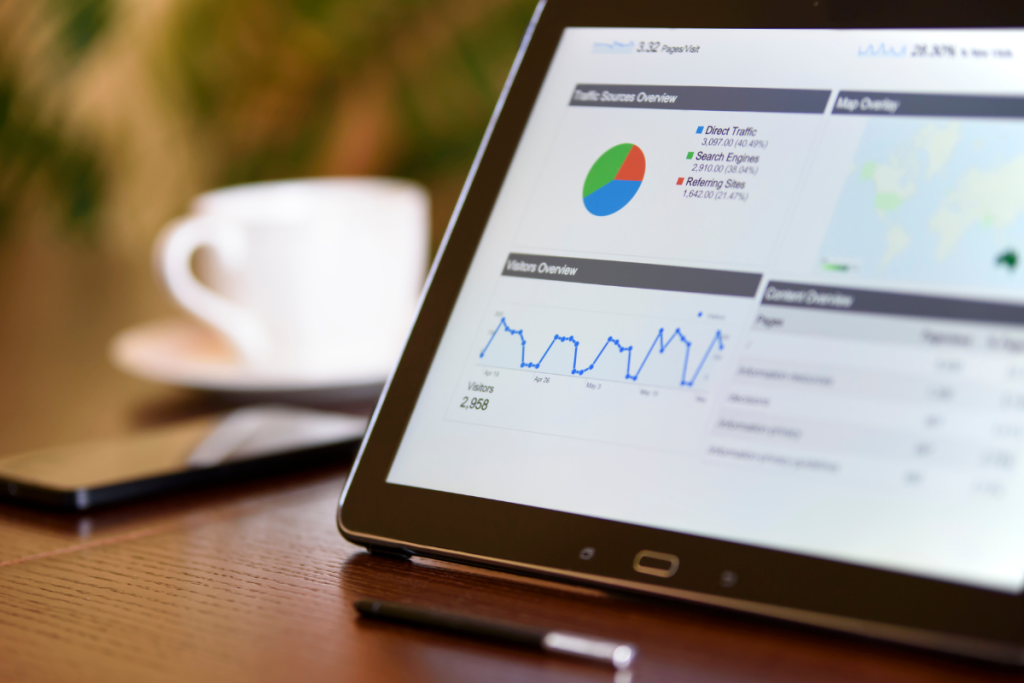
FRACAS works best when integrated into the overall maintenance strategy. Here are several ways in which it complements other maintenance management tools:
- Integration with CMMS: It can be combined with a Computerized Maintenance Management System (CMMS) to automate failure reporting, track corrective actions, and leverage data for better decision-making.
- Collaboration with Reliability-Centered Maintenance (RCM): RCM and FRACAS can work together. RCM identifies critical assets and failure modes, while FRACAS ensures all failures, regardless of size, are reported, analyzed, and addressed.
- Root Cause Analysis (RCA): RCA tools are integral to the failure analysis phase in FRACAS, helping determine the underlying causes and guiding corrective actions.
Benefits of Implementing FRACAS in Maintenance Operations
Better Resource Allocation
FRACAS helps organizations allocate resources more effectively by directing efforts toward resolving the most critical failures. This focused approach ensures that time and resources are used efficiently, improving overall maintenance outcomes.
Improved Safety
Failure to address the root causes of equipment breakdowns can lead to unsafe conditions. FRACAS ensures that safety-related failures are addressed before they escalate into hazardous situations, particularly in industries like oil and gas, manufacturing, or chemical processing.
Compliance and Reporting
FRACAS can help ensure compliance with industry regulations by providing comprehensive records of failure reports, analyses, and corrective actions. This documentation is invaluable during audits and regulatory inspections.
Enhanced Equipment Life Cycle Management
By addressing the underlying causes of failures, FRACAS helps extend the life cycle of equipment. Preventive actions slow the rate of wear and tear, reducing the frequency of major repairs or replacements.
Putting it to an end
FRACAS is a powerful tool for improving maintenance operations. Through its structured approach to failure reporting, analysis, and corrective actions, FRACAS not only enhances equipment reliability but also contributes to more efficient maintenance practices. It integrates seamlessly with other strategies such as CMMS and predictive maintenance, offering a data-driven approach to optimize maintenance activities.
For organizations looking to improve their maintenance tasks, adopting FRACAS is a key step in driving efficiency, reducing costs, and enhancing overall equipment performance.