A significant portion of serious and fatal workplace accidents are caused by deficiencies in or breakdowns in work systems. Since there is a high risk of errors occurring without a defined procedure for performing a task securely and a recognized process in place to deal with non-routine procedures.
A system called Permit-to-work explains the steps you must take to provide a safe working environment in your company. In this essay, let’s quickly look at it.
What is a Permit to Work System?
A formal document known as a permit to work specifies exactly how, when, and where an activity is to be carried out. Contractors are given specific, constrained authority to enter the site in order to carry out that particular task.
Simply put, a permit-to-work system contributes to the safety of dangerous occupations. This is so that the work that needs to be done and the dangers associated may be communicated clearly and succinctly. Both the person performing the chores and others nearby are helped by it.
Additionally, it guarantees that only authorized individuals are permitted to perform the work and that they are properly trained and equipped. You may be sure that all safety precautions are being followed by putting in place a permit process.
How Permit to Work Helps Reduce Risk within Your Work Premises? – The Purpose of Permit to Work System
The purpose of a permit to work is to lessen the possibility of safety problems. This is accomplished by making sure that those tasked with carrying out certain high-risk duties are competent, aware of the relevant hazards, and taking the necessary safeguards.
Each task will have specific requirements based on the circumstance, the procedure, the location, and the work that needs to be done. Safety risks cannot always be completely removed. The 9 steps to operate safely with permission to work, however, goes into detail about various ideas that could assist reduce risk.
9 Steps of a Safe Work Environment with Permit to Work
Step 1: Prevent
As much as possible, dangerous work must be minimized or eliminated. This action is guided by the philosophy of preventing harm and minimizing unnecessary employee exposure. By assuring great design across three areas—equipment, process, and work—prevention can be achieved.
1. Appropriate Equipment Design
The design of the plant must ensure that workers are kept out of dangerous circumstances and that the plant itself is intrinsically safe. The following can be used to achieve this:
- Reducing the number of dangerous elements.
- Substituting less risky materials for hazardous ones.
- Limit or moderate the potency of harmful compounds.
- Reduce complexity in the design to reduce interactions with the equipment.
2. Effective Process Design
The procedure needs to be built with inherent safety in mind. Here, the same guidelines that apply to equipment can be applied: minimize, substitute, moderate, and simplify.
3. Adequate Work Design
Work that must be done in dangerous regions can also be planned to minimize or completely eliminate safety concerns. Every work requires meticulous planning as well as the consideration of alternatives. The use of the proper tools, methods, talents and other aspects must all be taken into consideration in good work design.
Step 2: Plan
The work that needs to be done must be planned out ahead of time before a permit is given. Employees may be exposed to certain combinations of risks and hazardous situations depending on the nature of the task at hand. Planning must be proactive and viewed as a chance to maybe anticipate and consequently eliminate any unneeded risks.
Careful task scheduling in advance is required for effective planning. Included are the following:
- Identifying the work that needs to be done.
- The damaged machinery or procedures.
- Equipment and tools are needed.
- Whether particular abilities are necessary.
- Making sure that PPE is offered where it is needed, that everyone is instructed on its use and that PPE is tested and inspected in advance.
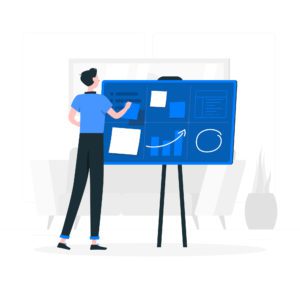
Step 3: Prepare
The work site will need to be ready before work can start after it has been designed. It may be necessary to shut down the process, clean up the process equipment, drain and purge, establish isolations where necessary, and make the work site safe as part of preparation at the work site done in advance. Process operators frequently carry out this preparation, but this is not always the case. It may take multiple shifts to complete preparation work, thus communication between shifts is crucial.
A site inspection is typically part of the preparation process to confirm exactly what needs to be done. To make the most of the shutdown opportunity, planners should also search the maintenance system for more outstanding repair orders in the same region.
Step 4: Permit
Either the job card or the work order will be used to generate the permit. There are a number of methods in use that enable certain permit information to be recorded many days before the scheduled work, with the final information being recorded once the work has begun.
Additionally, some organizations have central offices where officials from operations and/or maintenance prepare, examine and approve permits. The person responsible for authorizing the permit, also known as the issuer/authorizer and the receiver, will sign it alongside the person in charge of the work.
The permit to work will also list the parties engaged in the project and bear their signatures. There may be customized templates used to speed up the creation process if the identical work has already been completed or the job fits into a specific category.
Step 5: Precaution
Precautions are required to make sure that work is carried out safely once the work permit is established and hazards are identified. Precautions can consist of things like unique techniques, specialized equipment, isolations, any additional duties, PPE, etc.
Step 6: Personal Protective Equipment (PPE)
PPE, or personal protective equipment, is a component of safety measures taken to lessen or prevent bodily damage. Hard hats/helmets and safety boots are examples of standard PPE. The work permit must list both of these and any other PPE that is required for the task.
The PPE must be suitable for the task at hand and in excellent working order. PPE standards for the activity must be carefully planned and practical, adding to safety rather than taking away from it.
Step 7: Proceed
The job can now start since all previous processes have been finished. The permission must be legally issued and acknowledged by the respective parties in order to be enforceable as a contract. At this point, the permit must contain all required data, such as:
- The task at hand.
- The risks associated with the task.
- The safety measures that must be taken, include the use of PPE.
- The team members assigned to carry out the work have been confirmed to have the necessary skills and abilities.
The permit must be a tangible document so that anyone doing the work can easily access it. Additionally, having a physical document makes it simpler for health and safety officials to confirm that the work is being done in accordance with the permit’s conditions.
Step 8: Pack Up
The site needs to be cleaned up after the work is over, and the tools and equipment need to be packed up. Individual isolations must be eliminated whenever they are used, and the affected plant component must then be recommissioned and put back into service.
The permit procedure controls how things are handed away. It entails the handoff of accountability from the team that carried out the job back to regular operations. The crew is then excused from performing the precise task and the permit is approved.
Stage 9: Process
When all of the work has been finished, the final step is taken. It entails the examination, processing, and auditing of data from the permit system. The task at hand may be finished once the permit has been approved, but the process is not finished at that point. Analyzing data from prior permits is one of the important elements in a well-designed safety management system.
This makes it possible to spot patterns and any gaps in safety protocols. Additionally, it is crucial to apply any lessons discovered to subsequent practices. Regular permit audits serve a crucial purpose that can lead to new policies, training initiatives, improved business norms, and a more efficient maintenance process.
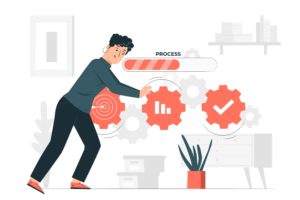
Wrapping it up:
The procedures outlined above are typical of the method used during non-routine maintenance carried out with a permit. Of course, this method will vary at each location depending on the type of work being done there and the operation being conducted. Although each permission to work safety system implementation will be unique, the essential concepts will remain the same. To know more about how you can implement a Permit-to-Work system in your organization for a Safe working environment, connect with our experts now at contact@terotam.com or schedule a call now.