Preventive maintenance is a proactive approach to managing facilities, ensuring that all systems and equipment are in optimal condition to prevent failures. One of the critical benefits of preventive maintenance is its role in reducing the risk of fire accidents. Fires can cause significant damage, endanger lives, and result in substantial financial loss.
This article explores how preventive maintenance can help avoid fire accidents, highlighting the importance of maintaining facilities properly, the major areas requiring attention, and specific preventive measures that can be taken.
How Poor Facility Maintenance Can Be Fire Prone?
Poor maintenance is a significant contributing factor to fire accidents in various facilities. When maintenance is neglected, the likelihood of electrical failures, such as short circuits and overheating, increases due to worn-out wiring, overloaded circuits, and malfunctioning electrical equipment. Without proper maintenance, these critical systems may fail, leading to uncontrolled fires and increased damage. When maintenance is neglected, several risks increase:
Electrical Failures:
Faulty wiring, overloaded circuits, and malfunctioning electrical equipment can spark fires.
Mechanical Failures:
Heating, ventilation, and air conditioning (HVAC) systems that are not regularly serviced can overheat or fail, leading to fires.
Accumulation of Flammable Materials:
Dust, debris, and other flammable materials can accumulate in neglected areas, providing fuel for fires.
Malfunctioning Fire Safety Systems:
Fire alarms, sprinkler systems, and extinguishers require regular maintenance to function correctly. Without it, these critical systems may fail during a fire emergency.
How Preventive Maintenance Can Avoid Chances of Fire?
Preventive maintenance is a systematic approach to inspecting, testing, and servicing equipment and systems to identify and correct potential issues before they escalate into serious problems. By implementing a thorough preventive maintenance program, facilities can significantly reduce the risk of fire accidents.
Here are detailed ways in which preventive maintenance helps avoid the chances of fire:
1. Early Detection of Electrical Hazards
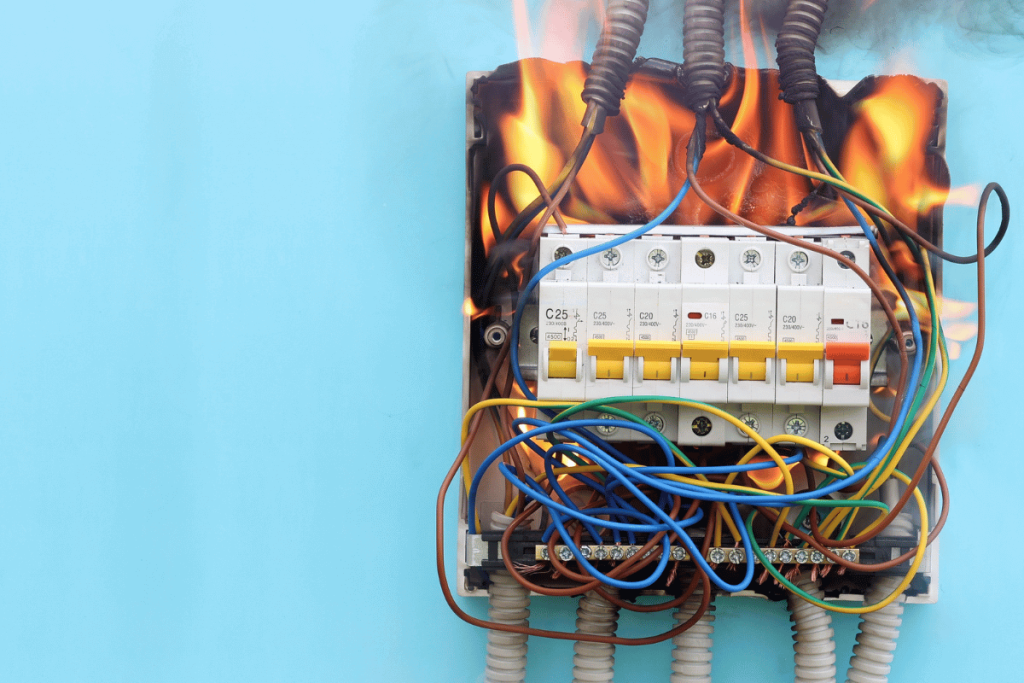
- Inspection of Wiring and Circuits: Regular inspections of electrical wiring and circuits help identify wear and tear, frayed wires, and loose connections that can cause short circuits or sparks, leading to fires.
- Testing Electrical Panels: Routine testing of electrical panels ensures they are not overloaded and that all connections are secure. Identifying and addressing issues like faulty breakers or corrosion can prevent overheating and potential fires.
- Maintaining Electrical Equipment: Regular maintenance of electrical equipment and appliances ensures they operate within safe parameters. This includes checking for overheating components, faulty switches, and ensuring proper grounding.
2. Ensuring Proper Functioning of Fire Safety Systems
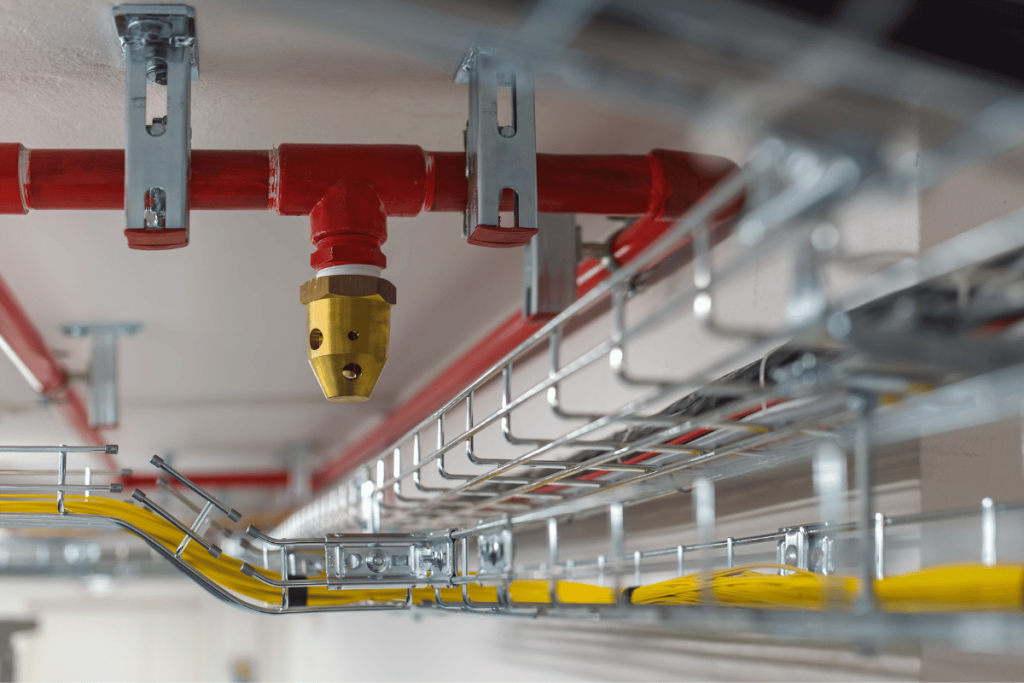
- Regular Testing of Fire Alarms: Fire alarms need to be tested frequently to ensure they are operational and can provide early warnings in case of fire. This includes checking battery levels, sensors, and alarm functionality.
- Servicing Sprinkler Systems: Sprinkler systems should be inspected and tested to ensure they have adequate water pressure and no blockages. Regular maintenance ensures that sprinklers will activate promptly and effectively during a fire.
- Inspecting Fire Extinguishers: Fire extinguishers must be regularly inspected to ensure they are charged, accessible, and have not passed their expiration date. This guarantees that they can be used immediately in an emergency.
3. Reducing Accumulation of Flammable Materials
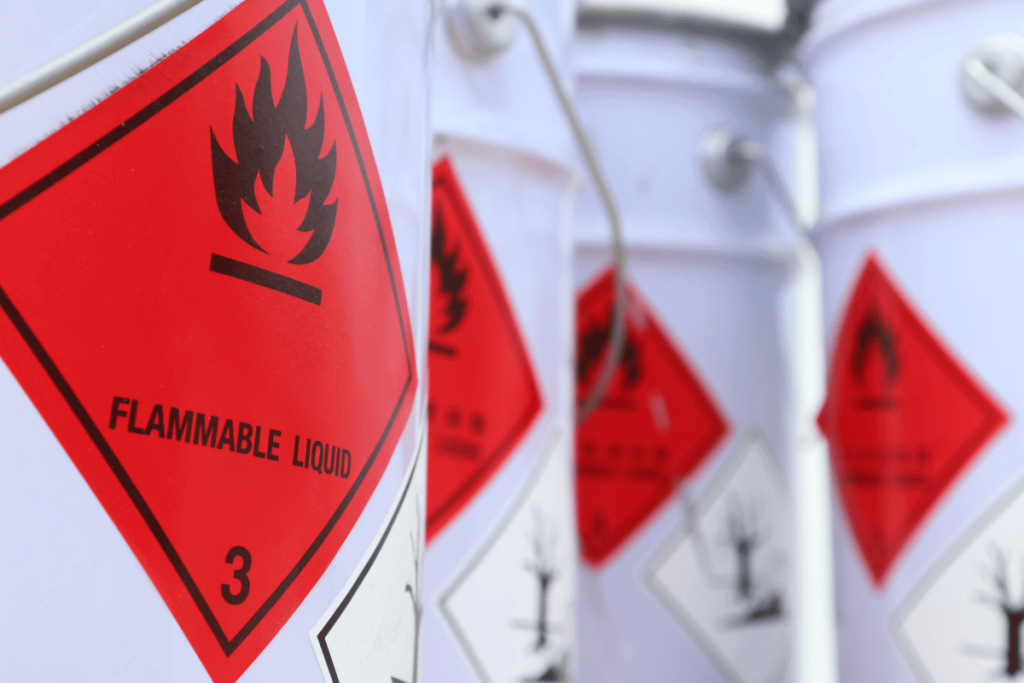
- Regular Cleaning: Routine cleaning of facilities reduces the buildup of dust, debris, and other flammable materials. This includes cleaning areas that are often overlooked, such as behind appliances, in ductwork, and storage areas.
- Proper Storage Practices: Implementing proper storage practices for flammable materials can prevent accidental ignition. This includes using fire-resistant storage cabinets, keeping flammable materials away from heat sources, and ensuring proper labeling and segregation of chemicals.
4. Maintaining HVAC Systems

- Cleaning Air Filters and Vents: Regularly cleaning or replacing air filters and vents in HVAC systems prevents the buildup of dust and debris that can act as fuel for fires.
- Inspecting Mechanical Components: Ensuring that all mechanical components of HVAC systems, such as motors and compressors, are in good working order prevents overheating and mechanical failures that could lead to fires.
- Checking Ductwork: Inspecting and cleaning ductwork prevents the accumulation of flammable materials and ensures that airflows correctly, reducing the risk of overheating.
5. Ensuring Compliance with Safety Standards
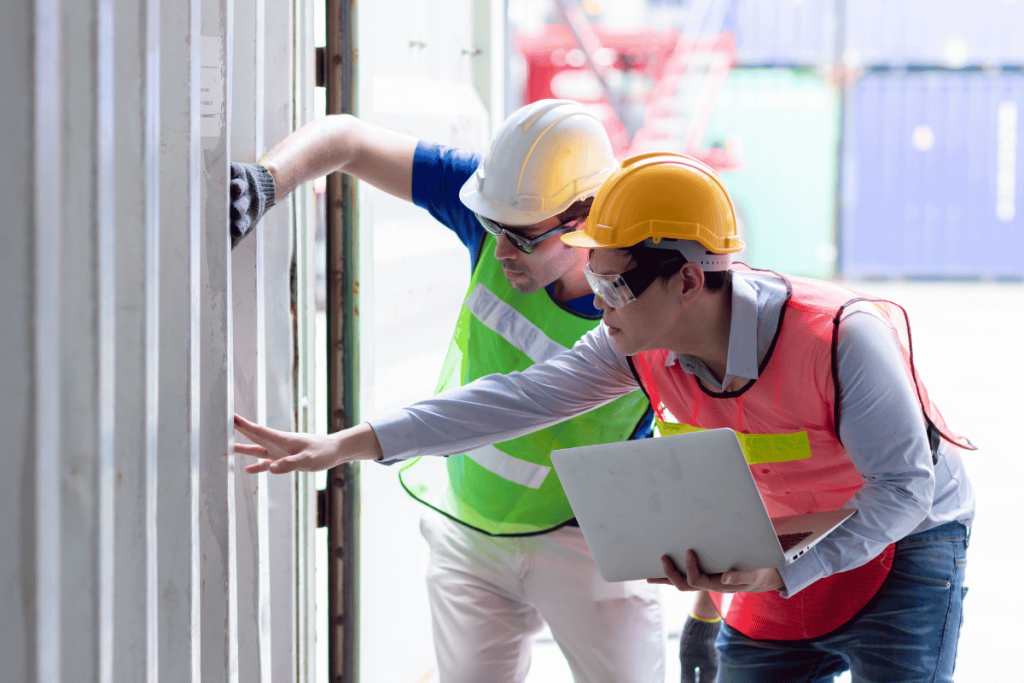
- Adhering to Fire Codes: Regular maintenance ensures that facilities comply with local fire codes and safety standards, which are designed to minimize fire risks. This includes maintaining clear exit paths, proper signage, and fire-resistant construction materials.
- Updating Safety Protocols: Keeping safety protocols up-to-date with regular training and drills ensures that all personnel are prepared to act quickly and effectively in the event of a fire. Regularly reviewing and updating these protocols can identify new risks and improve response strategies.
6. Inspecting Building Structure
- Checking for Structural Integrity: Regular inspections of the building’s structural components, such as walls, ceilings, and floors, can identify and repair potential fire hazards, like gaps that could allow fire to spread more quickly.
- Maintaining Fire Doors and Exits: Ensuring that fire doors and emergency exits are unobstructed and functional is critical. Regular maintenance includes checking door seals, hinges, and automatic closing mechanisms to ensure they will work correctly in an emergency.
- Fireproofing Materials: Regular inspections and maintenance of fireproofing materials and insulation can help contain and slow the spread of fire, providing more time for evacuation and firefighting efforts.
7. Maintaining Emergency Lighting and Signage
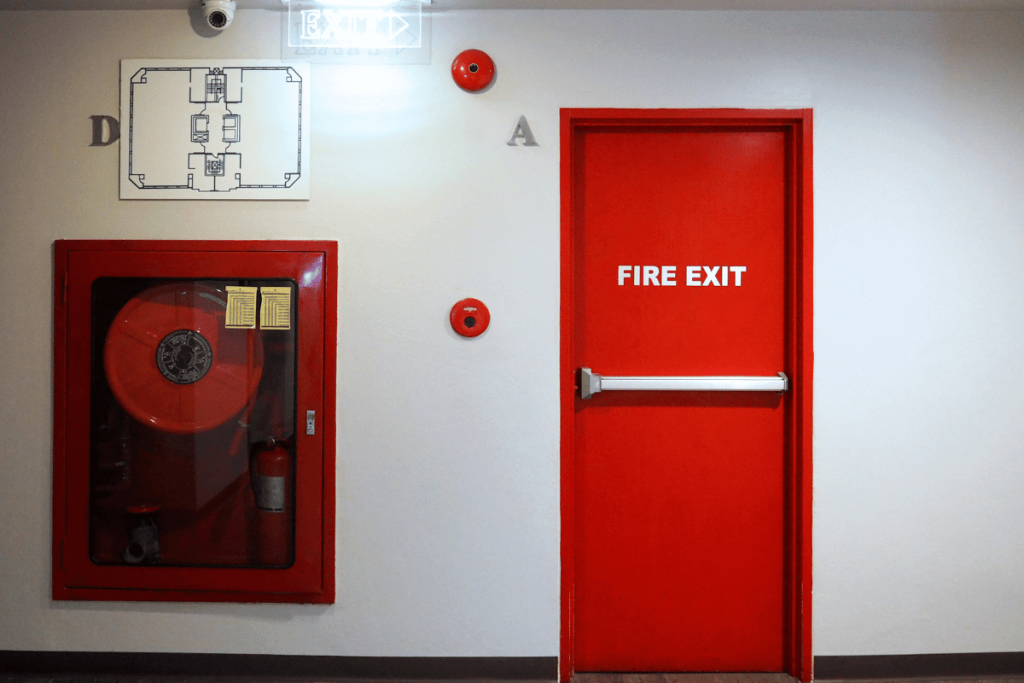
- Testing Emergency Lights: Ensuring that emergency lighting systems are operational can guide occupants safely out of the building during power outages caused by a fire. Regular testing and maintenance of these systems are essential.
- Checking Exit Signs: Regularly checking that exit signs are illuminated and clearly visible ensures that building occupants can quickly find their way to safety in an emergency.
8. Servicing Kitchen Areas
- Cleaning Cooking Equipment: Regular cleaning and maintenance of stoves, ovens, and other cooking equipment prevent grease fires, which are a common cause of kitchen fires.
- Maintaining Hood and Ventilation Systems: Ensuring that kitchen hoods and ventilation systems are free of grease buildup reduces the risk of fire spreading.
- Inspecting Gas Lines and Connections: Regular inspections of gas lines and connections prevent leaks that could ignite and cause fires.
9. Roof and Exterior Maintenance
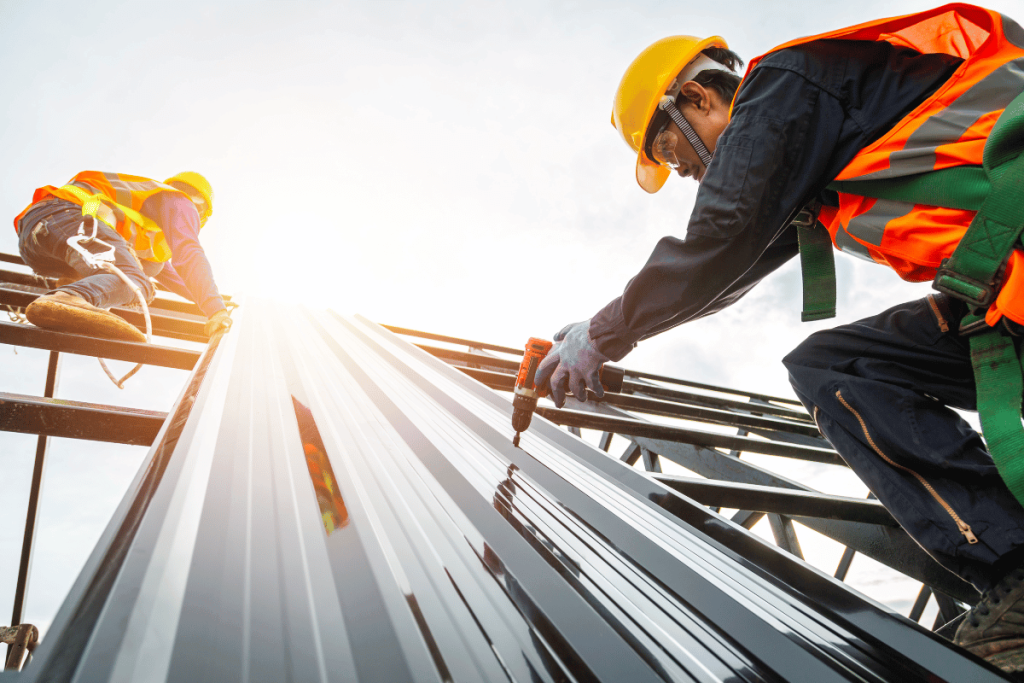
- Inspecting Roofing Materials: Regular inspections ensure that roofing materials are in good condition and fire-resistant, preventing external fires from spreading to the building.
- Cleaning Gutters and Drains: Keeping gutters and drains free of debris prevents the accumulation of materials that could ignite and cause roof fires.
- Maintaining Exterior Lighting and Signage: Regular maintenance of exterior lights and signs prevents electrical fires and ensures that these systems function correctly during emergencies.
Ending Note:
Preventive maintenance is an essential strategy for reducing the risk of fire accidents in facilities. Proactively managing electrical systems, HVAC units, fire safety equipment, storage areas, and the building’s structural integrity, helps facility managers to significantly mitigate fire hazards.
Implementing a comprehensive preventive maintenance program is a crucial step toward creating a safer environment and avoiding the devastating impacts of fire accidents. Want to know how to make your Preventive maintenance simple and sure with the CMMS system and avoid unwanted fire accidents? – Connect our experts now or write us at contact@terotam.com