The concept of Reliability Centered Maintenance (RCM) emerged from the aviation industry in the 1960s. Faced with the challenge of maintaining increasingly complex aircraft, engineers needed a more effective way to ensure safety and reliability. Traditional maintenance methods often involved frequent overhauls and replacements and were costly and inefficient. This led to the development of RCM, a strategy focused on understanding the specific functions of each component, the ways they could fail, and the most effective maintenance practices to prevent those failures. The success of RCM in aviation soon caught the attention of other industries, leading to its widespread adoption.
Reliability Centered Maintenance (RCM) is a methodical approach designed to ensure that assets continue to operate as needed in their current operating context. Unlike traditional maintenance strategies that might apply a uniform approach to all equipment, RCM focuses on understanding the specific functions and failure modes of each asset. This allows for tailored maintenance strategies that prioritize critical assets and failure prevention methods most effective for each scenario.
The result? Improved reliability, reduced downtime, and lower overall maintenance costs.
Key Principles of Reliability-Centered Maintenance
- Function-Oriented: RCM prioritizes the functions that an asset needs to perform. It addresses the question, “What do we need this equipment to do?” and aligns maintenance efforts to ensure these functions are consistently met.
- Failure-Based: Rather than solely preventing failure, RCM seeks to understand the types and causes of failures. It identifies potential failure modes and their effects on system performance, enabling targeted preventive measures.
- Reliability-Focused: The objective is to maintain the inherent reliability of equipment by focusing on the most critical aspects of its operation. This approach acknowledges that not all components require the same level of maintenance.
- Cost-Effective: RCM optimizes maintenance costs by balancing the expense of maintenance activities with the risk and cost of failures. It ensures that resources are allocated where they can provide the most benefit.
- Data-Driven: Decisions in RCM are based on detailed data analysis, historical performance, and failure patterns. This data-driven approach enhances predictive maintenance capabilities.
The Process of RCM
Implementing RCM involves several key steps:
- Identify Critical Assets: Determine which assets are most critical to operations and require detailed analysis.
- Define Functions and Performance Standards: Clearly outline what each asset is supposed to do and the standards it must meet.
- Identify Failure Modes: Analyze how each asset can fail and the potential effects of these failures on operations.
- Evaluate Failure Consequences: Assess the impact of each failure mode, considering factors such as safety, operational impact, and cost.
- Select Maintenance Tasks: Based on the analysis, determine the most appropriate maintenance tasks to address each failure mode. This might include preventive maintenance, condition-based monitoring, or redesign.
- Implement and Monitor: Put the selected maintenance strategies into practice and continuously monitor their effectiveness, making adjustments as necessary.
How is RCM Different from Standard Maintenance Programs?
Standard maintenance programs typically follow a one-size-fits-all approach, often based on fixed schedules or manufacturer recommendations. These programs might include regular preventive maintenance regardless of the actual condition or criticality of the equipment. While this can be effective to some extent, it can also lead to unnecessary maintenance activities and increased costs.
In contrast, RCM is more strategic and targeted. It focuses on understanding each asset’s specific functions and failure modes. This allows for customized maintenance strategies prioritizing critical assets and failure prevention methods that are most effective for each scenario. As a result, RCM often results in improved reliability, reduced downtime, and lower overall maintenance costs compared to standard maintenance programs.
CMMS and RCM – How do both go hand in hand?
A Computerized Maintenance Management System (CMMS) can be a powerful tool in implementing and managing an RCM program. A CMMS helps in the following ways:
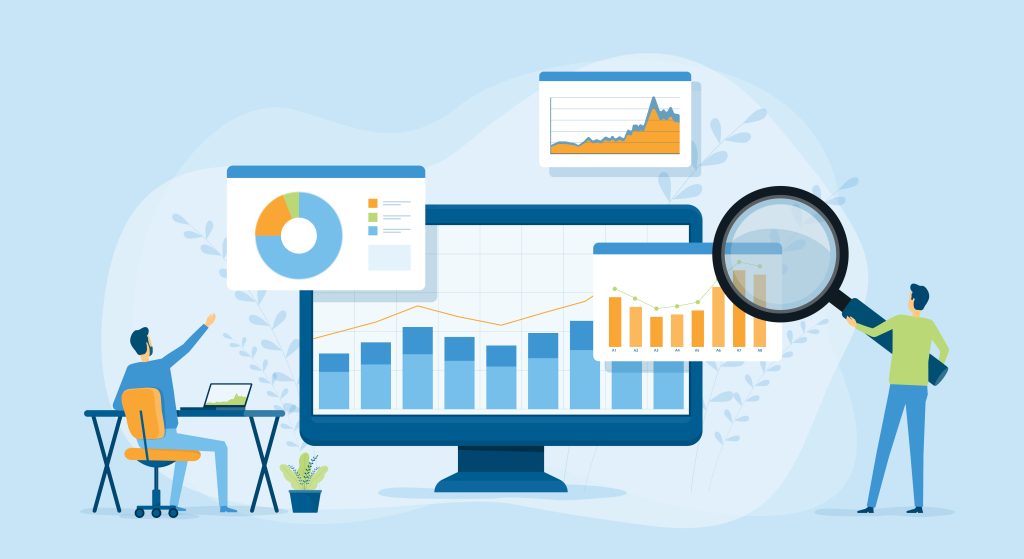
- Data Collection and Analysis: A CMMS can collect and analyze vast amounts of data on equipment performance, failure modes, and maintenance activities. This data is crucial for making informed decisions in an RCM program.
- Scheduling and Tracking: CMMS software can automate the scheduling of maintenance tasks based on RCM analysis, ensuring that critical tasks are performed at the right intervals.
- Condition Monitoring: Many modern CMMS solutions integrate with condition monitoring tools and sensors, allowing for real-time tracking of equipment health and performance. This supports condition-based maintenance strategies within an RCM framework.
- Documentation and Reporting: A CMMS provides a centralized platform for documenting maintenance activities, tracking asset history, and generating reports. This enhances transparency and accountability in the RCM process.
- Continuous Improvement: A CMMS supports the continuous improvement aspect of RCM by providing insights into maintenance effectiveness and asset performance, helping organizations refine their maintenance strategies over time.
Conclusion
Reliability-centered Maintenance is more than just a maintenance strategy; it’s a game-changer that ensures that your operations run smoothly and efficiently. Integrating RCM with a robust CMMS can further enhance these benefits, providing a comprehensive solution to modern maintenance challenges. Discover how TeroTAM’s advanced CMMS can help you implement RCM effectively and unlock the full potential of your assets. Schedule a meeting now with our expert or write us at contact@terotam.com