Elevators are the backbone of modern buildings, quietly carrying people and goods every day. But when they stop working unexpectedly, it can cause major disruptions—not just in operations, but also in safety and customer trust. For service providers, staying ahead of faults is no longer optional—it’s a necessity.
Relying on manual schedules or reactive repairs often leads to missed issues, increased breakdowns, and rushed service calls. This is where preventive maintenance software makes a real difference. It helps service teams plan smarter, act faster, and keep elevators running smoothly.
In this article, we’ll explore the key benefits of preventive maintenance software for elevator service providers—from reducing downtime to improving compliance, streamlining operations, and gaining data-driven insights.
The essential role of maintenance for lifts performance
Elevators operate continuously under mechanical and electrical stress, often making hundreds of trips daily. Over time, components like motors, brakes, door mechanisms, and control panels experience wear and tear. Without regular maintenance, small issues can escalate into major faults—affecting not just performance, but also safety and reliability.
Proper maintenance ensures smooth rides, accurate floor levelling, quicker door operations, and minimal downtime. It also extends the service life of components, reduces energy consumption, and lowers the chances of costly emergency repairs. For service providers, consistent upkeep is not just a technical task—it’s a direct contributor to user satisfaction and contractual performance.
Inconsistent or delayed maintenance can also trigger compliance issues, especially in buildings governed by strict safety codes. Regular servicing helps identify risks early, avoids fines, and builds trust with property managers and building occupants. Whether the lift is in a residential tower or a commercial high-rise, maintenance is the foundation for uninterrupted, safe operation.
Risks of skipping elevator maintenance: what can go wrong?
Elevators might run smoothly for a while even without attention, but that silence is deceptive. Mechanical systems deteriorate gradually, and without proper maintenance, small issues often snowball into bigger, costlier problems.
In high-traffic buildings, a lift failure can instantly disrupt daily routines and trigger urgent repair calls. For service providers, inconsistent maintenance not only raises operating costs but also affects client satisfaction and long-term contracts.
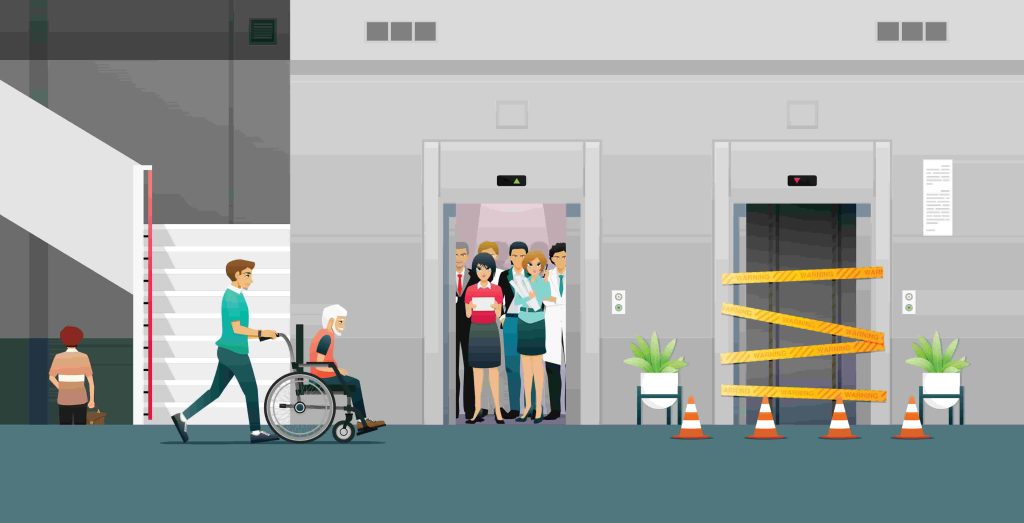
Here’s what can go wrong without proper elevator maintenance:
Frequent breakdowns
When faults aren’t addressed early, components fail more often, leading to repeated service interruptions and emergency call-outs.
Safety hazards
Worn-out brakes, faulty door sensors, or uncontrolled speeds can create dangerous situations for passengers inside the elevator.
Increased repair costs
Deferred maintenance leads to bigger problems that require urgent repairs, overtime labour, and premium-priced spare parts.
Regulatory fines
Missed inspections or outdated safety certificates can attract penalties from local authorities and damage your service reputation.
Shortened equipment lifespan
Neglected elevators experience faster wear on motors, ropes, and electronic systems, reducing their usable operational life.
Tenant dissatisfaction
Frequent downtime leads to complaints from building occupants and puts pressure on property managers to change vendors.
6 reasons why preventive maintenance is non-negotiable for elevator service providers
Elevator systems are intricate networks of mechanical, electrical, and electronic components that operate under high-frequency cycles. Preventive maintenance isn’t just a way to reduce breakdowns—it’s a system-driven approach that optimises the performance, safety, and lifespan of each subsystem. When overlooked, even minor deviations in system behaviour can result in high-risk faults, costly component damage, and regulatory non-compliance.
Here’s a breakdown of six technically-driven reasons why preventive maintenance must be an integral part of every elevator service strategy:
1. Controls mechanical wear across high-friction components
Elevator systems involve constant interaction between moving parts—sheaves, bearings, rollers, hoist ropes, and guide rails. These are all subject to fatigue, misalignment, and micro-fracturing due to repetitive motion.
Scheduled maintenance allows precise measurements of wear tolerance, alignment checks, and re-lubrication schedules based on duty cycles. It also helps detect early-stage mechanical imbalance that could lead to major motor strain or hoisting failure.
2. Maintains reliability of control systems and electronics
Elevator controllers manage the logic, routing, and feedback of the entire lift operation. Over time, issues like sensor drift, relay burnout, or firmware glitches can lead to unpredictable behaviour.
Preventive servicing includes diagnostics on I/O modules, memory usage, software updates, and inspection of control boards for voltage irregularities or corrosion. Regular controller recalibration ensures consistent response times and fault-free ride logic.
3. Reduces load stress on motors and drive systems
The traction motor and drive system bear the brunt of every lift operation. Without timely intervention, torque overload, overheating, or insulation degradation can go undetected.
Preventive tasks include thermal scanning, current draw analysis, and VFD tuning. Monitoring motor RPM stability and load distribution helps prevent overloading and prolongs motor brush and bearing life.
4. Prevents failures in safety-critical subsystems
Safety gear, overspeed governors, buffers, and interlocks are passive systems that don’t activate under normal conditions—but when they do, they must perform flawlessly.
Routine inspections involve mechanical triggering of safety devices, governor tension checks, buffer oil level verification, and fail-safe system diagnostics. Preventive routines ensure these safety mechanisms meet operational thresholds and activate without delay during fault scenarios.
5. Optimises door operation cycles and alignment
Lift doors undergo thousands of open-close cycles daily, making them one of the most failure-prone parts. Malfunctions here often stem from alignment drift, motor wear, or sensor calibration loss.
Preventive maintenance includes torque testing, sensor recalibration, track cleaning, and door clearance measurement. By maintaining proper door operation parameters, the system avoids erratic closures or user entrapment.
6. Enables early-stage detection through performance analytics
Advanced preventive maintenance platforms integrate data logging, condition monitoring, and analytics to spot anomalies like cycle time variations or repeated error codes.
This data-driven approach helps identify high-friction travel zones, load inconsistencies, or even floor level drift before they turn into full-system failures. It gives technicians the ability to intervene based on patterns, not just schedules.
Benefits of implementing preventive maintenance software for elevator maintenance
Managing elevator maintenance today means juggling complex systems, tight schedules, and safety demands. Preventive maintenance software helps service providers organize tasks efficiently, track vital data, and detect problems before they cause breakdowns or safety risks. It’s a powerful tool that supports both routine servicing and advanced diagnostics, helping providers deliver better, faster service.
Here are the key ways this software improves elevator maintenance operations:
1. Smarter scheduling based on actual elevator usage
Elevators don’t all operate the same way—some see light use, others run almost non-stop. Scheduling maintenance based only on fixed intervals can either waste resources or miss signs of wear.
Preventive maintenance software uses data like door cycles, motor run hours, and travel distance to create schedules tailored to each elevator’s actual workload. This targeted approach avoids unnecessary maintenance while ensuring critical lifts get attention before problems develop.
2. Centralized and detailed service records
In elevator maintenance, knowing the history of repairs and inspections is crucial for quick diagnosis and preventing repeat issues.
The software stores all service records digitally—tracking what work was done, parts replaced, faults reported, and inspections completed. This creates a complete profile for each elevator, making it easy for technicians to review past work and plan the right interventions.
3. Efficient technician dispatch and job preparation
Technicians often lose valuable time when sent without clear information or the right tools, leading to multiple visits and longer downtime.
Preventive maintenance software assigns jobs based on each technician’s skills and experience, while providing detailed fault histories and required parts before they arrive on site. This improves the chances of fixing issues on the first visit and reduces service delays.
4. Early detection through real-time data monitoring
Many modern elevators are equipped with sensors that monitor parameters like motor current, door speed, and vibration levels. These data points signal when components are starting to fail.
Integrated software collects and analyzes this information remotely, alerting service teams about abnormal patterns before faults cause breakdowns. This proactive insight allows maintenance to be scheduled precisely when needed, avoiding costly emergency repairs.
5. Simplified compliance with automatic documentation
Elevator maintenance is subject to strict safety regulations that require detailed records of all inspections and repairs.
Instead of relying on paper forms, preventive maintenance software automatically logs every service task with timestamps, technician details, and digital signatures. This streamlines regulatory audits and reduces the risk of missing or inaccurate documentation.
6. Accurate tracking of parts and inventory management
Without clear records, it’s easy to lose track of which components were replaced or when they need replacement again. This can cause delays when parts are out of stock or past warranty.
The software monitors part usage and service intervals, helping managers forecast inventory needs and schedule timely part replacements. This reduces downtime caused by waiting for parts and keeps repairs efficient.
7. Transparent communication with clients
Building owners and managers want to stay informed about elevator safety and maintenance status without sifting through technical jargon.
Preventive maintenance software generates clear, professional reports summarizing completed work, identified issues, and upcoming maintenance plans. This transparency builds client confidence and supports long-term service agreements.
Putting it to the end
Successful elevator maintenance relies on staying proactive and organized rather than reacting to problems after they occur. Preventive maintenance software gives service providers a comprehensive way to manage schedules, track equipment health, and access important data in real time. This leads to fewer breakdowns, faster repairs, and improved safety for building occupants.If you want to boost your team’s efficiency and deliver a higher level of service, reach out to us at contact@terotam.com. We’re here to support your journey toward smarter, more reliable elevator maintenance that keeps clients satisfied and operations running smoothly.