Rotating machinery forms the backbone of numerous industries, from manufacturing plants to power generation. These machines, including motors, turbines, pumps, and compressors, are integral to operational efficiency and production quality. However, maintaining their optimal performance requires constant monitoring to avoid unexpected breakdowns and costly repairs. One of the most effective tools for ensuring the longevity and reliability of these machines is vibration analysis.
In this article, we will explore the concept of rotating machinery, the role vibration analysis plays in monitoring their condition, how it helps in decision-making, and the significance of predictive maintenance through CMMS software.
Concept of Rotating Machineries
Rotating machinery refers to any equipment with rotating parts that perform mechanical work, such as electric motors, fans, pumps, and compressors. These machines typically operate under high loads and at varying speeds, which can lead to wear and tear over time. The condition of rotating machinery is directly tied to its components, such as bearings, shafts, and gears, all of which experience stress during operation.
Monitoring the performance and health of these machines is essential to prevent costly failures and downtime, especially in industries where equipment is critical for operations.
Use of Vibration Analysis for Rotating Machineries
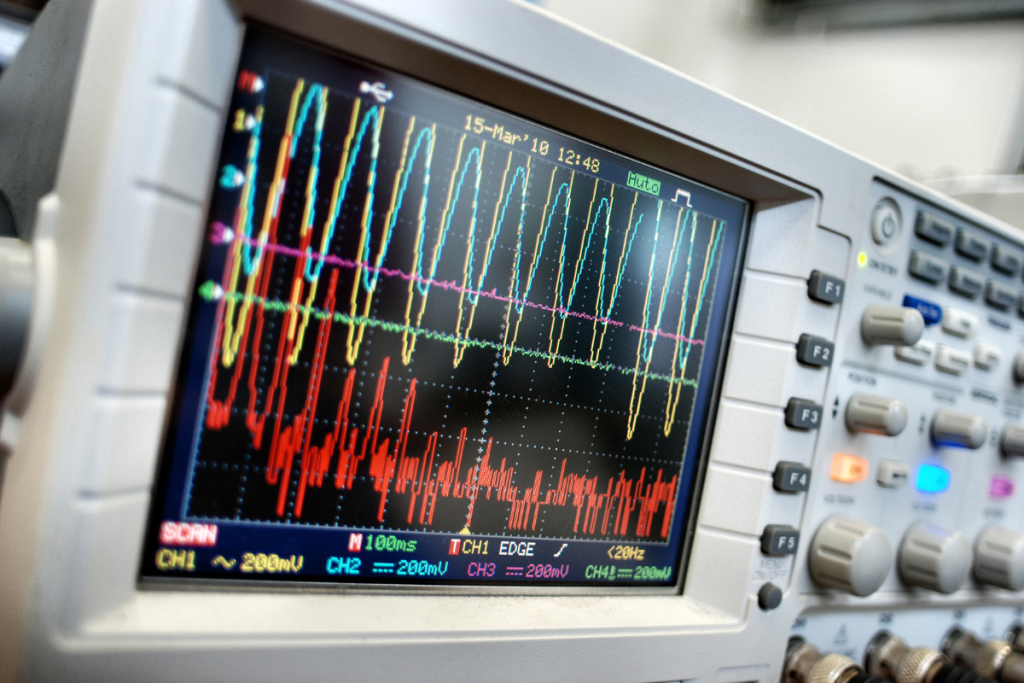
Vibration analysis is a diagnostic tool that plays an important role in the maintenance of rotating machinery. Given the continuous operation of machines such as motors, turbines, and pumps, they inevitably experience wear and stress that can lead to mechanical faults. Regular vibration monitoring helps identify these faults early, preventing unplanned downtime and costly repairs.
Understanding vibration patterns offers insights into the operational health of machinery. With proper analysis, technicians can identify specific issues affecting the performance of rotating equipment, ensuring that corrective actions are taken before failures occur. This proactive approach significantly enhances machine reliability and operational efficiency, making vibration analysis a cornerstone of modern industrial maintenance strategies.
What does Vibration Analysis Do in the Case of Rotating Machineries?
Vibration analysis involves capturing and analyzing vibration signals from rotating machinery to assess its operational condition. Each rotating machine generates specific vibration patterns depending on its internal components and operating conditions. Any deviation from these typical vibration signatures indicates potential faults, such as misalignment, imbalance, or bearing degradation. Identifying these issues early prevents the progression of damage, reducing the risk of unexpected failures and unplanned downtime.
This analysis also provides real-time insights into machinery performance, which is critical for maintaining high efficiency in operations. Vibration data helps identify root causes of abnormal vibrations, making it easier for maintenance teams to apply targeted corrective actions, ultimately enhancing machine reliability and performance.
What Result Does Vibration Analysis Produce?
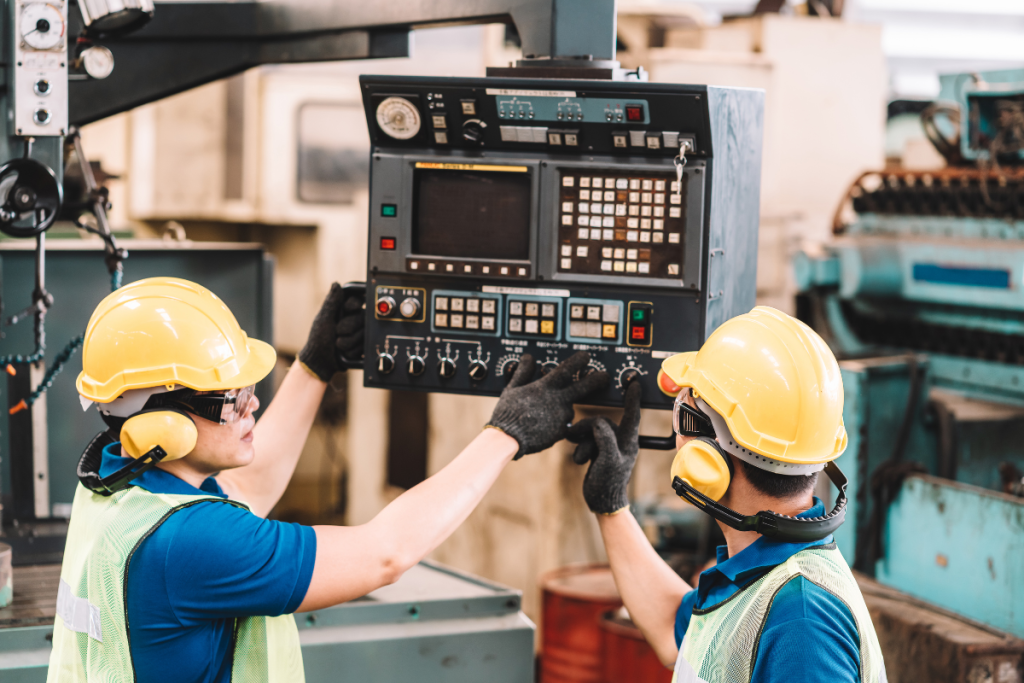
Vibration analysis provides crucial data that enables precise diagnostics and decision-making for rotating machinery. The results of vibration analysis can be interpreted to identify specific faults, determine their severity, and forecast potential failures. Here’s what vibration analysis produces:
- Identification of Fault Types: Differentiates between common issues such as imbalance, misalignment, bearing wear, and gear damage based on vibration signatures.
- Severity Assessment: Quantifies the severity of faults using vibration amplitude and frequency, which helps in determining the urgency of maintenance.
- Trend Analysis: Tracks vibration data over time, enabling the detection of patterns that may indicate gradual wear or deterioration, allowing for predictive maintenance.
- Frequency Spectrum Data: Produces frequency spectra that help in pinpointing specific faults by correlating vibrations to known fault frequencies (e.g., bearing defect frequencies or gear meshing issues).
- Critical Fault Detection: Detects issues such as resonance or natural frequency matches that could cause catastrophic damage if not addressed.
- Operational Conditions Assessment: Evaluates the operational efficiency of machinery by comparing current vibration levels with baseline data, indicating if any adjustments are needed to optimize performance.
- Remaining Useful Life Estimation: Provides an estimate of the remaining useful life of components based on the progression of vibration patterns, assisting in better maintenance scheduling.
- Component-Specific Insights: Offers data for specific components, such as bearings or gears, helping to isolate failure points and reduce unnecessary component replacements.
How Predictive Maintenance is Useful for Rotating Machineries?
Predictive maintenance is an approach that uses data-driven insights, such as vibration analysis, to predict when equipment might fail or require servicing. When coupled with a CMMS software, it becomes even more powerful. CMMS helps track maintenance schedules, store vibration data, and analyze machine performance trends over time.
Through this integration, operators can shift from reactive to proactive maintenance strategies, reducing unplanned downtime and optimizing repair cycles. Predictive maintenance ensures that repairs are performed only when necessary, which helps cut maintenance costs and extend the life of rotating machinery.
Ending note
Vibration analysis provides a practical approach to maintaining the health of your machinery, allowing you to address issues before they cause costly disruptions. Staying proactive ensures smoother operations and extends the lifespan of your equipment. Interested in exploring how this can benefit your business? Reach out to us at contact@terotam.com and we’ll be happy to help.