The manufacturing and maintenance sectors have long been burdened by fragmented workflows, outdated equipment monitoring methods, and inefficiencies in resource utilization. Challenges such as unplanned downtime, limited data visibility, and disconnected systems have historically hampered productivity and escalated operational costs. Addressing these inefficiencies requires advanced technological solutions that enable streamlined operations and predictive decision-making.
This article examines the transformative role of technology in bridging the gaps within manufacturing and maintenance management. We will explore the evolution of operational practices, the implementation of advanced tools and, the impact of integrated systems on enhancing efficiency and sustainability in industrial processes.
The Evolution of Manufacturing and Maintenance Practices
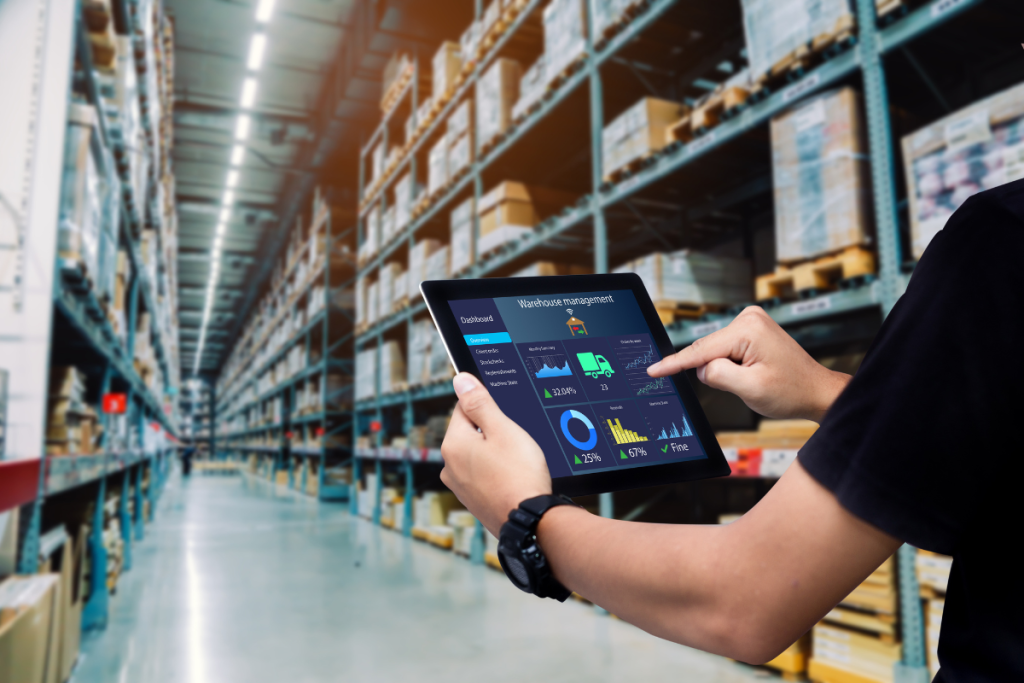
For decades, manufacturers and maintenance teams have struggled with isolated systems, manual data handling, and limited real-time monitoring. These gaps resulted in downtime, high operational costs, and misaligned resource allocation. The inability to predict equipment failures and efficiently schedule maintenance caused further inefficiencies, limiting overall productivity.
The lack of reliable tools and processes left organizations vulnerable to disruptions, often requiring extensive time and resources to restore operations. Without the support of data-driven insights, teams operated reactively, addressing problems only after they surfaced. These challenges highlighted the need for modern solutions capable of transforming the industry’s approach to management.
Shifting Focus Toward Integrated Management
As businesses move toward streamlined operations, the focus has shifted to comprehensive systems that unify workflows and enable proactive strategies. Instead of dealing with scattered tools and processes, organizations are increasingly adopting integrated solutions that centralize and simplify management. This change aims to reduce inefficiencies, improve decision-making, and maximize the utilization of assets and personnel.
Emphasis on Predictive and Proactive Strategies
Modern businesses recognize the importance of proactive rather than reactive management approaches. Predictive maintenance has emerged as a key focus area, enabling organizations to forecast equipment issues before failures occur. The adoption of IoT sensors and real-time analytics allows teams to monitor machine performance, reducing downtime and extending equipment lifespans.
Predictive strategies enable organizations to transition from costly emergency repairs to planned interventions. This approach minimizes production disruptions and ensures that equipment operates at optimal performance levels. Such advancements have proven especially beneficial for industries with high-value assets or critical infrastructure.
Rise of Digital Ecosystems
Digital ecosystems have replaced fragmented tools with cohesive systems. Platforms for Enterprise Asset Management (EAM) and Computerized Maintenance Management Systems (CMMS) centralize operations. These systems integrate data across departments, improving collaboration between production, engineering, and maintenance teams.
With evolving and growing real-time communication and seamless data sharing, digital ecosystems eliminate traditional silos that hinder efficiency. They also provide transparency, enabling stakeholders to track progress, identify bottlenecks, and make informed decisions that drive continuous improvement.
Core Technologies Transforming Manufacturing and Maintenance

The adoption of advanced technologies has redefined how manufacturing and maintenance teams manage operations. These tools address long-standing gaps in communication, monitoring, and resource allocation, leading to improved performance and reduced operational costs.
Below are some of the key technologies making this transformation possible.
Internet of Things (IoT) and Real-Time Monitoring
IoT devices enable real-time data collection from machinery, ensuring timely insights into performance. Sensors embedded in equipment detect anomalies such as temperature spikes or unusual vibrations, alerting maintenance teams instantly. This capability reduces reaction times and minimizes unplanned downtime.
IoT solutions not only enhance monitoring but also allow organizations to optimize maintenance schedules and resource utilization. Data gathered from connected devices supports predictive analytics, providing actionable insights that improve operational reliability.
Artificial Intelligence (AI) and Machine Learning (ML)
AI and ML enhance decision-making by analyzing historical and real-time data to identify patterns and predict potential failures. These technologies also optimize inventory management by forecasting spare part needs, ensuring critical components are always available.
The ability of AI to process vast amounts of data enables organizations to uncover trends and correlations that would otherwise go unnoticed. Maintenance teams benefit from improved accuracy in fault detection and faster resolutions, ultimately increasing efficiency and reducing costs.
Digital Twins for Simulation and Optimization
Digital twins create virtual replicas of physical assets, providing valuable insights into how equipment operates under various conditions. Maintenance teams can use these simulations to test interventions, optimize processes, and reduce risk during actual operations.
These virtual models enable teams to anticipate issues and refine strategies without disrupting ongoing production. Digital twins also allow engineers to assess different scenarios, ensuring the most effective solutions are implemented.
Cloud-Based Solutions for Data Accessibility
Cloud-based systems such as CMMS software allow seamless access to maintenance and operational data from any location. This flexibility supports remote monitoring, cross-location collaboration, and informed decision-making, making organizations more agile and responsive.
Centralized cloud-based CMMS solutions enhance scalability and security while reducing infrastructure costs. Teams can collaborate in real-time, ensuring a unified approach to managing challenges and maintaining operational continuity.
Summing it up
Technology is revolutionizing how manufacturers and maintenance teams tackle their biggest challenges. From IoT-enabled real-time monitoring to AI-driven predictive analytics and digital twins, these innovations are driving efficiency, reducing downtime, and fostering collaboration. The key to staying ahead lies in adopting solutions that not only close existing gaps but also future-proof your operations.If you’re ready to explore how these technologies can transform your manufacturing and maintenance management, our team at Terotam is here to help. Reach out to us at contact@terotam.com to take the first step toward a more efficient and connected future.