Equipment downtime is a major concern for businesses that rely on machinery to maintain productivity. Unexpected failures not only disrupt operations but also lead to costly repairs and lost revenue. Traditional maintenance strategies, such as time-based preventive maintenance, often fall short because they do not account for actual equipment usage.
Usage-based maintenance (UBM) offers a more effective approach. Instead of following a fixed schedule, UBM relies on real-time data and equipment performance metrics to determine when maintenance is actually needed. This approach enhances uptime, reduces costs, and improves asset longevity.
The Challenges with Traditional Maintenance Approaches
Businesses have historically relied on two primary maintenance strategies:
- Reactive Maintenance – Repairs are carried out only after a breakdown occurs. While this might seem cost-effective in the short term, it often leads to unexpected downtime, higher repair costs, and operational delays.
- Scheduled Preventive Maintenance – Maintenance is performed at predetermined intervals, regardless of actual usage. Although it reduces unexpected failures, it can lead to unnecessary servicing, increased costs, and even premature component replacement.
Limitations exist in both methods because they do not consider real-time usage patterns. An asset operating at full capacity daily will wear out differently than one used only a few hours a week. Usage-based maintenance provides a more efficient alternative.
What is Usage-Based Maintenance?
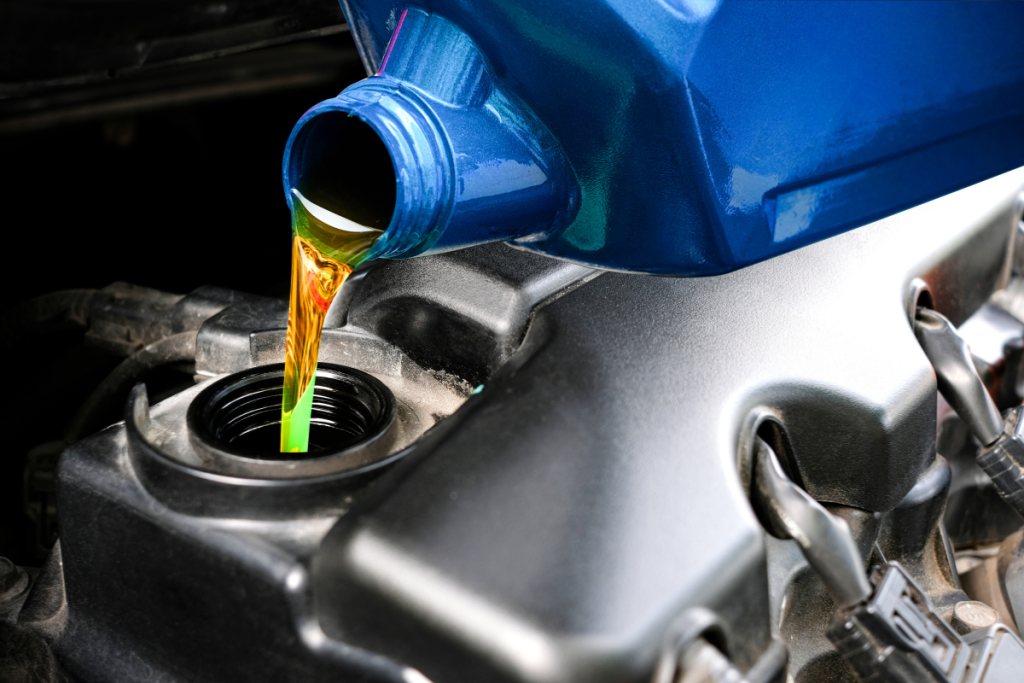
Usage-based maintenance is a proactive strategy where maintenance schedules are determined based on real-time equipment usage data. Instead of relying on fixed timelines, servicing is scheduled when the system reaches specific usage thresholds, such as:
- A certain number of operating hours
- The completion of a set number of production cycles
- The accumulation of a defined mileage or load
- Real-time sensor data indicating wear and performance decline
This approach ensures that maintenance is performed only when necessary, minimizing both over-maintenance and unexpected failures.
How Usage-Based Maintenance Maximize Equipment Uptime?
Unplanned downtime can severely impact productivity, leading to missed deadlines and financial losses. Traditional maintenance methods often fail to align with real-world usage, causing either excessive servicing or sudden failures.
A data-driven approach ensures that maintenance efforts are directed where they are needed most. Businesses can maintain operational efficiency, reduce unnecessary costs, and extend asset lifespan with usage-based maintenance.
1. Reduces Unexpected Breakdowns
Predicting potential failures before they occur minimizes downtime, helping businesses avoid costly operational disruptions.
- Real-time monitoring identifies early signs of wear and tear.
- Predictive analytics provide alerts based on performance trends.
- Immediate servicing prevents minor issues from escalating into major failures.
2. Optimizes Maintenance Intervals
Scheduling maintenance based on actual usage ensures that assets are neither over-serviced nor neglected.
- Heavy-use equipment gets timely servicing, preventing excessive wear.
- Lightly used machinery avoids unnecessary maintenance, reducing costs.
- Maintenance planning aligns with operational demands, improving efficiency.
3. Extends Equipment Life
Ensuring timely maintenance based on real performance conditions maximizes the lifespan of machinery.
- Lubrication and component replacements are done precisely when needed.
- Prevents excessive degradation caused by delayed servicing.
- Extends asset usability, reducing capital expenditure on replacements.
4. Improves Cost Efficiency
Minimizing unnecessary maintenance reduces both labor and material costs, improving financial efficiency.
- Eliminates expenses linked to premature component replacements.
- Reduces emergency repair costs associated with sudden breakdowns.
- Enhances workforce productivity by streamlining service schedules.
5. Enhances Productivity
Keeping equipment in peak condition ensures continuous operations without unexpected interruptions.
- Reduces downtime that disrupts production schedules.
- Enhances machine reliability, leading to consistent output.
- Supports better workforce planning by avoiding sudden equipment failures.
6. Supports Data-Driven Decision Making
Using real-time data allows businesses to make informed maintenance and investment decisions.
- Historical performance insights guide future equipment purchases.
- Identifies trends in wear and failure rates for better planning.
- Enables businesses to allocate resources efficiently for maintenance tasks.
Implementing Usage-Based Maintenance
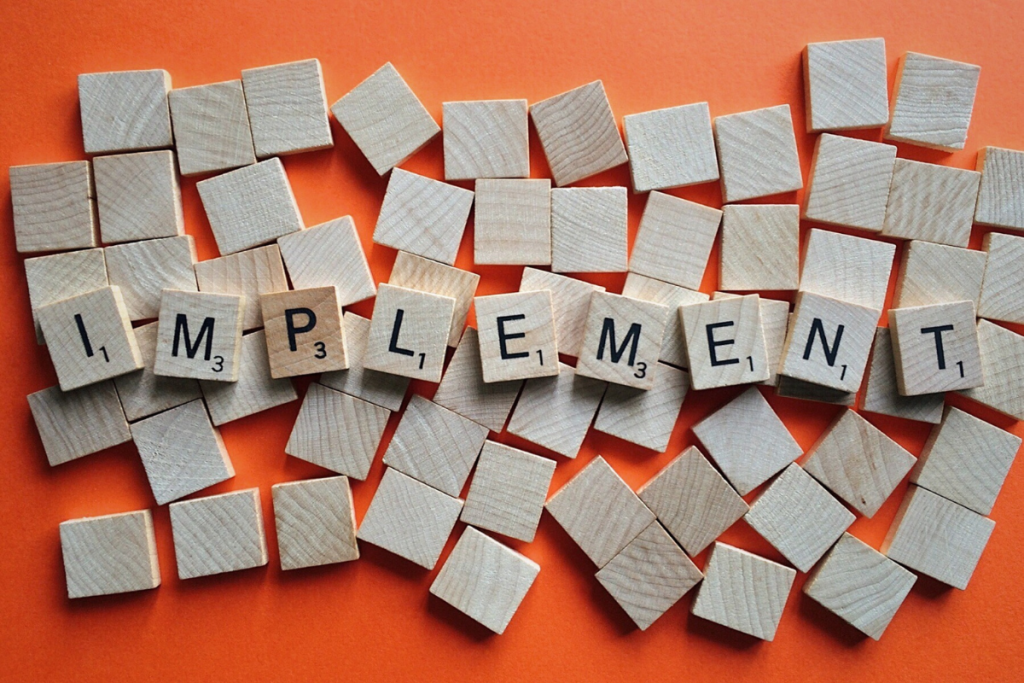
Transitioning to a usage-based maintenance model requires integrating the right tools, technologies, and processes. A structured approach ensures a smooth shift from conventional maintenance strategies to a data-driven system. Businesses must invest in monitoring equipment, analytics software, and training for maintenance teams.
a clear workflow for interpreting data and acting on insights is crucial for maximizing the benefits of UBM. When implemented effectively, this approach leads to improved equipment reliability, optimized resource allocation, and significant cost savings.
Key Steps for Implementing Usage-Based Maintenance
- Install IoT Sensors and Telematics – Real-time tracking devices provide continuous data on equipment performance and usage.
- Utilize Predictive Analytics and AI\ – Machine learning algorithms help detect patterns and forecast potential failures.
- Adopt a CMMS (Computerized Maintenance Management System) – Centralized platforms streamline scheduling, reporting, and maintenance tracking.
- Integrate with ERP and Asset Management Systems – Connecting maintenance data with enterprise-wide systems improves overall efficiency.
- Establish Threshold-Based Triggers – Maintenance actions should be initiated based on predefined performance and usage metrics.
- Train Teams on Data Interpretation – Maintenance staff must understand how to analyze and act upon real-time equipment insights.
- Continuously Improve Based on Feedback – Regular reviews of UBM data help refine maintenance strategies and improve outcomes.
- Ensure Regulatory and Compliance Alignment – Maintenance processes should meet industry standards and safety regulations.
Summing it up
Usage-based maintenance transforms equipment management by aligning servicing schedules with actual usage patterns. Real-time data, predictive analytics, and IoT-driven insights ensure maintenance is executed precisely when needed, preventing premature wear and costly breakdowns. Avoiding unnecessary servicing optimizes resources while extending asset life and reducing operational disruptions. Seamless integration with CMMS, ERP, and asset management systems enhances decision-making, ensuring every maintenance action is data-backed and strategically timed. Exploring ways to optimize your maintenance strategy? Connect with experts at support@terotam.com for tailored solutions.