Maintenance strategies are essential for ensuring the reliability, efficiency, and longevity of industrial equipment. Among the widely used methodologies, preventive maintenance (PM) and predictive maintenance (PdM) stand out. While both approaches aim to minimize downtime and extend asset life, their implementation, cost-effectiveness, and efficiency differ significantly.
The choice between preventive and predictive maintenance depends on multiple factors, such as asset criticality, industry regulations, budget constraints, and technological readiness. This article provides a detailed, technical breakdown of both approaches, highlighting their mechanisms, benefits, challenges, and real-world applications.
What is Preventive Maintenance?
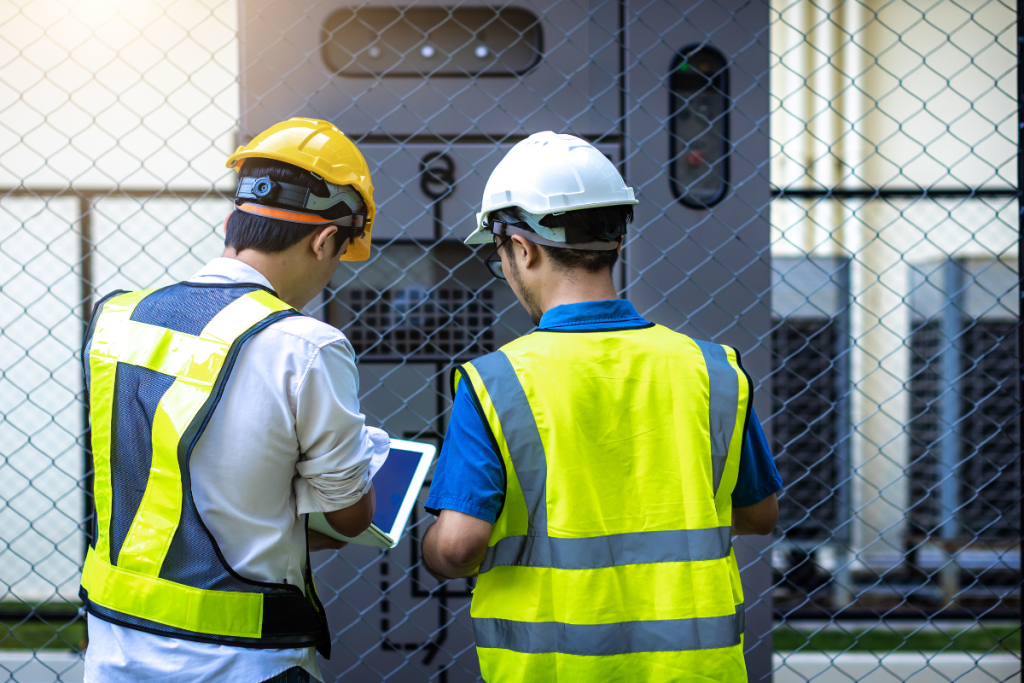
Preventive maintenance is a proactive, time-based approach where maintenance activities are scheduled at fixed intervals, regardless of the asset’s actual condition. This strategy is designed to reduce the likelihood of unexpected failures by servicing equipment based on predefined schedules.
Preventive maintenance is typically scheduled using:
- Time-based intervals (e.g., every three months)
- Usage-based triggers (e.g., every 5,000 operating hours)
- OEM recommendations (Original Equipment Manufacturer guidelines)
- Industry best practices
How Preventive Maintenance Works?
Preventive maintenance operates on a scheduled, proactive approach, ensuring equipment is serviced at regular intervals to minimize unexpected failures. It follows a structured process where inspections, lubrication, part replacements, and adjustments are carried out based on predefined schedules rather than actual asset condition. This method helps avoid premature wear and tear, enhances operational efficiency, and extends equipment lifespan.
The process typically includes the following steps:
- Establishing Maintenance Schedules – Maintenance tasks are planned based on time intervals (e.g., every six months) or usage metrics (e.g., every 1,000 operational hours).
- Routine Inspections – Technicians perform visual and manual checks to identify potential wear, misalignment, or component fatigue.
- Lubrication and Cleaning – Moving parts are lubricated, and dust or debris is removed to prevent friction and overheating.
- Component Replacements – Critical parts, such as belts, filters, or bearings, are replaced at set intervals to prevent sudden failures.
- Testing and Calibration – Equipment performance is tested, and necessary calibrations are performed to ensure optimal functionality.
- Documentation and Record-Keeping – Maintenance activities are logged for compliance, performance tracking, and future reference.
Key Features of Preventive Maintenance
- Fixed Maintenance Schedule: Carried out at regular intervals, whether needed or not.
- Manual Inspections: Relies on visual inspections and manual diagnostics.
- Standardized Maintenance Tasks: Follows predefined checklists and procedures.
- Lower Technological Dependence: Does not require complex monitoring systems.
Advantages of Preventive Maintenance
- Prevents Major Breakdowns: Regular servicing reduces the risk of sudden equipment failures.
- Cost Predictability: Budgeting for maintenance is easier since tasks are scheduled.
- Simpler Implementation: Requires minimal technological infrastructure.
- Extends Equipment Life: Reduces wear and tear, leading to longer asset lifespan.
- Compliance with Industry Regulations: Meets legal and safety standards in industries like aviation and healthcare.
Challenges of Preventive Maintenance
- Over-Maintenance: Unnecessary part replacements lead to higher costs.
- Potential for Human Error: Dependence on manual inspections may miss hidden defects.
- Does Not Prevent All Failures: Some issues arise unpredictably between maintenance cycles.
- Higher Labor Costs: Frequent servicing requires more workforce allocation.
What is Predictive Maintenance?
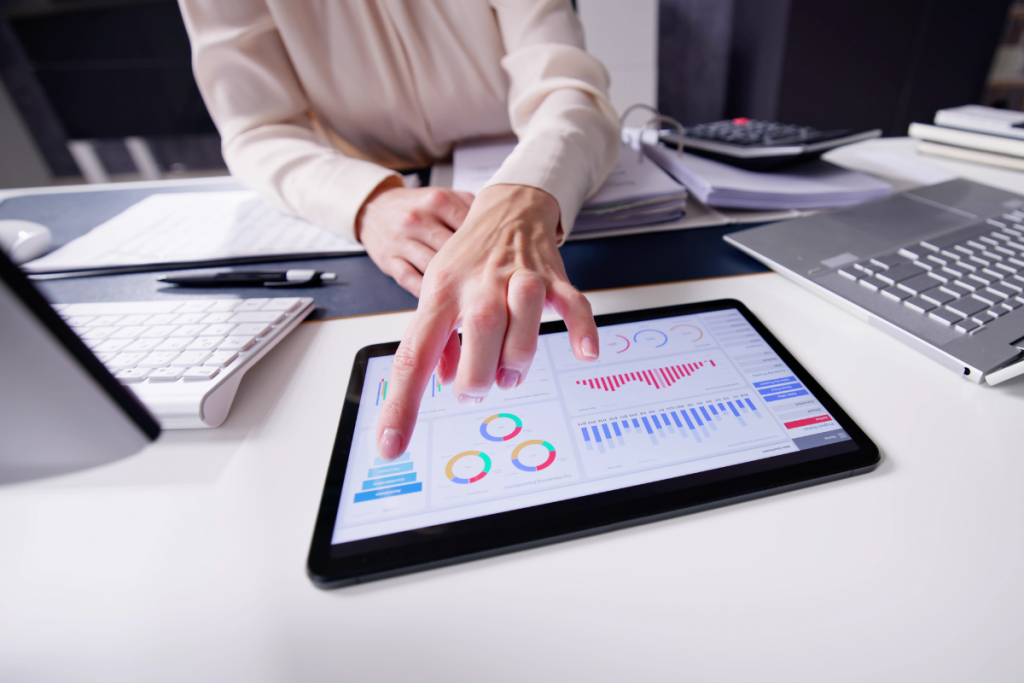
Predictive maintenance is a condition-based strategy that uses real-time data, advanced sensors, and analytics to determine when maintenance is required. Unlike preventive maintenance, PdM focuses on actual asset condition rather than time-based scheduling.
PdM relies on the Industrial Internet of Things (IIoT), Artificial Intelligence (AI), and machine learning to analyze asset behavior and predict failures before they happen.
How Predictive Maintenance Works?
Predictive maintenance relies on real-time data, advanced sensors, and AI-driven analytics to assess the actual condition of equipment and predict failures before they occur. Instead of following a fixed schedule, maintenance is performed only when necessary, reducing unnecessary servicing and optimizing resource allocation. This approach enhances asset reliability, minimizes downtime, and lowers maintenance costs.
The process typically includes the following steps:
- Sensor-Based Data Collection – IoT-enabled sensors continuously monitor key parameters like vibration, temperature, pressure, and electrical current.
- Data Transmission & Storage – Collected data is transmitted to cloud-based or on-premises systems for real-time analysis.
- Condition Monitoring & Trend Analysis – AI algorithms and machine learning models analyze performance patterns to detect anomalies.
- Failure Prediction & Alerts – Predictive models forecast potential breakdowns, triggering maintenance alerts before failures occur.
- Targeted Maintenance Actions – Technicians address specific issues based on predictive insights, reducing unnecessary part replacements.
- Continuous Improvement & Optimization – System performance data is used to refine predictive models and improve maintenance strategies over time.
Key Features of Predictive Maintenance
- Condition-Based Monitoring (CBM): Uses real-time data for maintenance decisions.
- IoT & AI Integration: Relies on smart sensors and AI-driven analysis.
- Failure Prediction: Identifies faults before they lead to failures.
- Automated Alerts: Triggers maintenance only when necessary.
Advantages of Predictive Maintenance
- Reduced Unplanned Downtime: Detects failures early, minimizing sudden breakdowns.
- Optimized Maintenance Costs: Reduces unnecessary servicing and extends component life.
- Improved Equipment Efficiency: Ensures optimal performance through real-time tracking.
- Increased Asset Lifespan: Minimizes wear and tear by addressing issues before escalation.
- Better Safety Compliance: Identifies hazardous conditions early, reducing accidents.
Challenges of Predictive Maintenance
- High Implementation Cost: Requires investment in sensors, software, and skilled personnel.
- Complex Setup & Integration: Needs advanced data analytics and system integration.
- Not Suitable for All Assets: Older or low-cost assets may not justify PdM investment.
- Requires Skilled Workforce: Data interpretation and system management need expertise.
Comparison: Preventive vs. Predictive Maintenance
Factor | Preventive Maintenance (PM) | Predictive Maintenance (PdM) |
Approach | Time/usage-based maintenance | Condition-based, data-driven maintenance |
Technology Use | Low – relies on manual inspections | High – uses sensors, IoT, and AI |
Failure Prevention | Reduces failures but cannot prevent all | Detects early warning signs, reducing failures |
Cost | Lower initial cost but higher long-term expenses due to over-maintenance | Higher upfront investment but lower long-term costs |
Implementation Complexity | Simple to implement | Requires integration of advanced monitoring systems |
Effectiveness | Works well for predictable maintenance tasks | More effective in preventing failures |
How the Manufacturing Industry Uses Preventive and Predictive Maintenance?
Preventive Maintenance:
Manufacturing plants follow scheduled maintenance for robotic arms, conveyor belts, and motors every three months. Components such as lubricants, belts, and bearings are replaced at fixed intervals to prevent unexpected breakdowns. While this approach ensures smooth operations, it sometimes results in replacing parts before they actually wear out.
Predictive Maintenance:
IoT sensors and AI-based monitoring track vibration, temperature, and motor efficiency in real time. If a conveyor belt motor starts overheating, predictive analytics detect the anomaly and trigger a service request before failure occurs. This method reduces production downtime and extends asset lifespan.
How the Power Generation Industry Uses Preventive and Predictive Maintenance?
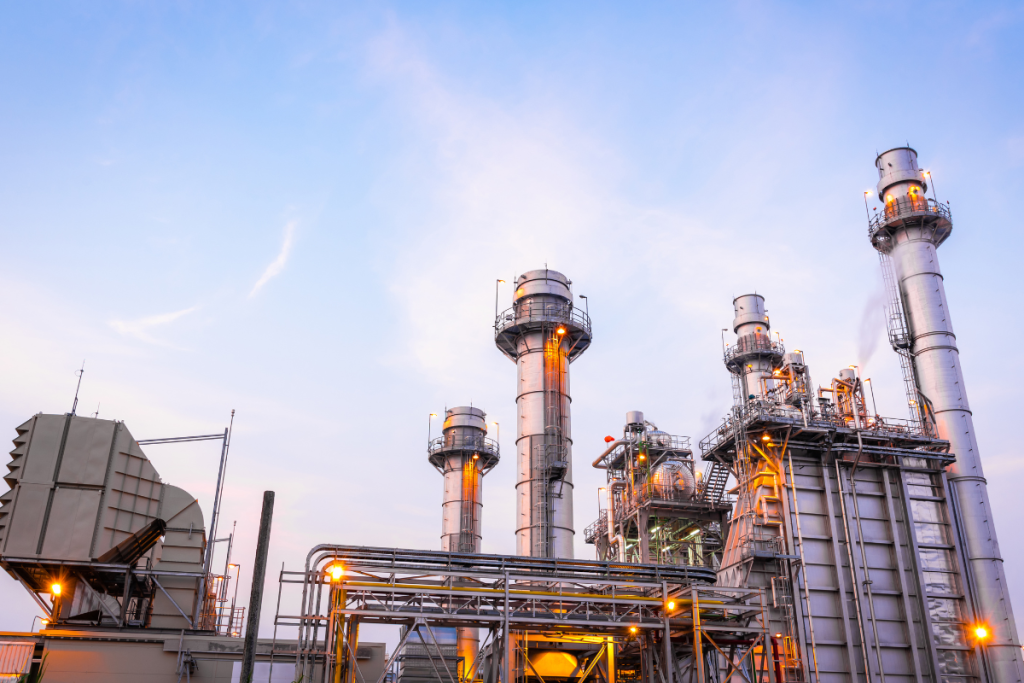
In the Power Generation Industry, ensuring uninterrupted energy supply depends on the performance and reliability of high-value equipment. To avoid failures and maintain efficiency, power plants are moving beyond traditional maintenance methods. By combining scheduled preventive maintenance with data-driven predictive maintenance, they can detect issues early, reduce downtime, and control operational costs more effectively.
Preventive Maintenance:
Gas turbines in power plants are serviced after every 6,000 operating hours. Technicians replace seals, inspect combustion chambers, and conduct thermal imaging scans—even if no faults are detected. This process ensures reliability but often results in unnecessary labor and component costs.
Predictive Maintenance:
Thermal sensors and acoustic monitoring track temperature fluctuations and vibration patterns in real time. If abnormal patterns are detected, maintenance is performed only when necessary. This approach reduces unexpected shutdowns, optimizes fuel efficiency, and lowers operational costs.
How Does the Oil & Gas Industry Use Preventive and Predictive Maintenance?
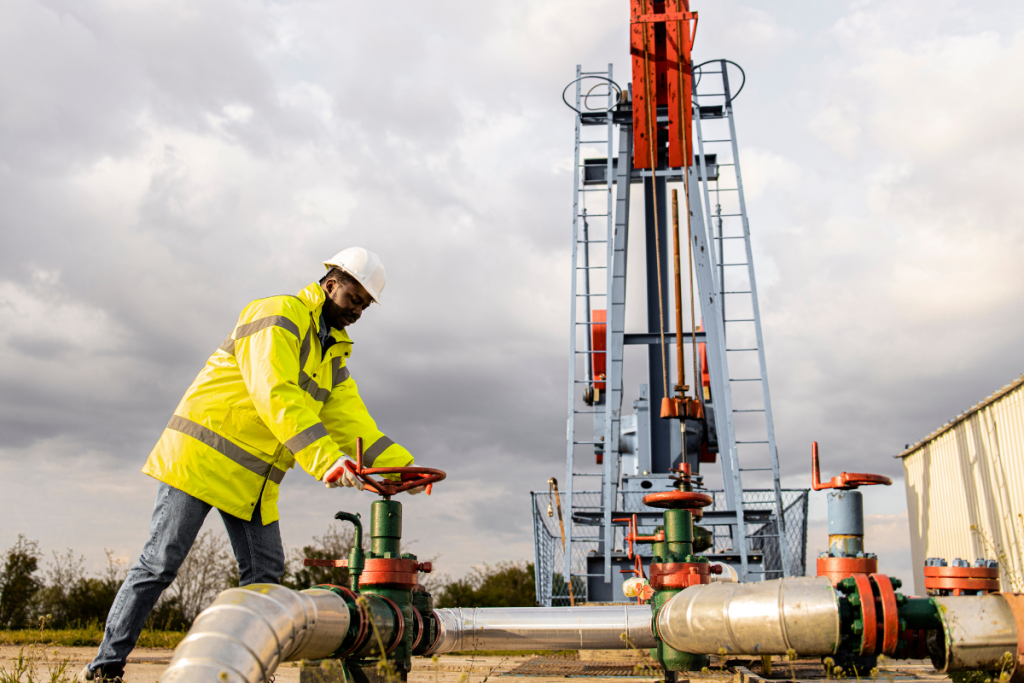
The Oil & Gas Industry operates in some of the most demanding environments, where equipment reliability is critical for safety and productivity. With high operational risks and costly downtime, companies are turning to proactive maintenance strategies to stay ahead. By combining traditional preventive maintenance with intelligent predictive maintenance technologies, the industry is finding smarter ways to extend equipment life, reduce failures, and avoid unplanned shutdowns.
Preventive Maintenance:
Offshore drilling rigs follow strict maintenance schedules, servicing pumps, compressors, and pressure valves every 90 days. This prevents catastrophic failures but often results in over-maintenance, increasing downtime and costs.
Predictive Maintenance:
Real-time pressure monitoring and AI-driven predictive analytics detect early warning signs of equipment failure. If a pump shows reduced efficiency or an abnormal pressure drop, targeted maintenance prevents costly production halts. This approach avoids multimillion-dollar losses due to unplanned shutdowns.
How the Food and Beverage Industry Uses Preventive and Predictive Maintenance?
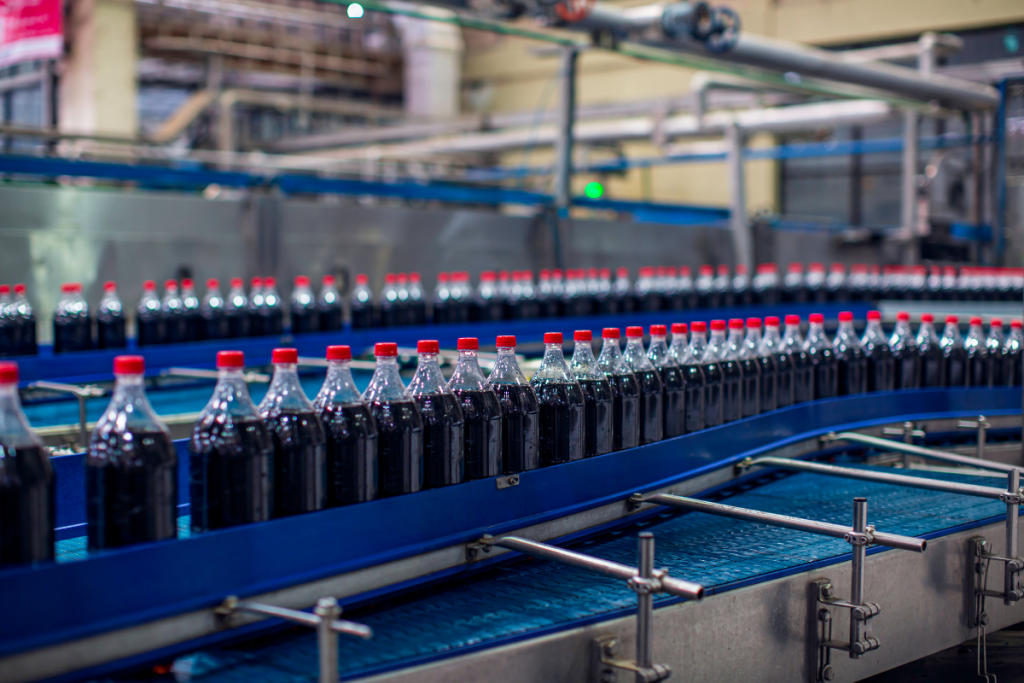
The Food and Beverage Industry depends on reliable equipment and consistent processes to deliver safe, high-quality products. To keep operations running smoothly and meet strict safety standards, businesses are adopting smarter maintenance strategies. From regular preventive maintenance to advanced predictive maintenance using AI and IoT, these approaches help reduce downtime, avoid equipment failures, and ensure compliance at every stage of production.
Preventive Maintenance:
Food processing plants follow strict maintenance schedules for production equipment, such as mixers, ovens, refrigeration units, and packaging machines. Routine servicing includes lubrication, cleaning, and part replacements at fixed intervals to prevent unexpected breakdowns. Compliance with food safety regulations requires frequent inspections of sanitization systems, conveyor belts, and temperature-controlled storage units. While this approach helps maintain hygiene and quality standards, it can lead to unnecessary maintenance tasks and production downtime.
Predictive Maintenance:
Smart sensors and AI-based analytics track temperature, pressure, vibration, and motor efficiency in real time. If a refrigeration unit shows abnormal temperature fluctuations or a mixer motor exhibits excessive vibration, predictive analytics trigger a maintenance alert before failure occurs. This ensures continuous production, prevents product spoilage, and reduces unplanned shutdowns.
Which Maintenance Strategy is Better?
The best maintenance strategy depends on:
- Asset Criticality: PdM is ideal for high-value, critical assets, while PM suits less complex equipment.
- Industry Regulations: Aerospace, healthcare, and power industries require stringent maintenance schedules (PM + PdM).
- Budget & Resources: Smaller businesses may prefer PM due to lower costs, while larger enterprises benefit from PdM’s efficiency.
- Technology Readiness: PdM requires advanced infrastructure, while PM is easier to adopt.
Hybrid Maintenance Approach of Combining Preventive and Predictive Maintenance
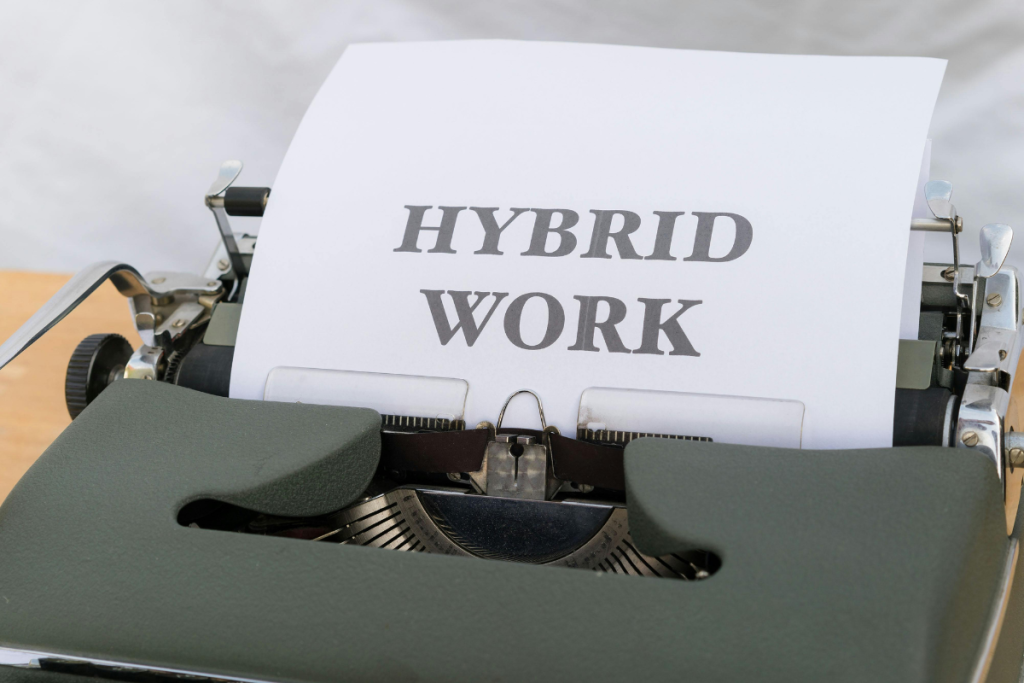
A balanced strategy combines preventive and predictive maintenance to maximize equipment reliability, reduce costs, and improve efficiency. Preventive maintenance ensures compliance and routine upkeep, while predictive maintenance optimizes servicing based on real-time data. This combination minimizes unnecessary maintenance while preventing unexpected failures.
- Categorize equipment needs by using preventive maintenance for compliance-driven assets and predictive maintenance for critical machinery.
- Integrate IoT and sensors to monitor temperature, pressure, and vibration for real-time equipment health tracking.
- Optimize maintenance intervals by adjusting schedules based on predictive data rather than fixed timeframes.
- Utilize AI-driven failure prediction to shift from fixed preventive tasks to condition-based servicing.
- Enhance workforce efficiency by focusing maintenance efforts on assets that actually require servicing.
- Ensure regulatory compliance by maintaining required inspections while using predictive tools to prevent failures.
- Reduce operational costs by minimizing unnecessary maintenance and extending equipment lifespan.
Conclusion
Finding the right balance between preventive and predictive maintenance isn’t just about keeping machines running—it’s about smarter decision-making, lower costs, and fewer unexpected breakdowns. A hybrid approach ensures businesses stay compliant, reduce downtime, and optimize maintenance efforts where they matter most. The right strategy depends on your industry, equipment, and operational goals.
Need help implementing an efficient maintenance strategy? Reach out to us at contact@terotam.com and let’s find the best solution for your business. Want to see how it works in action? Request a demo and explore how TeroTAM can streamline your maintenance operations.