Forklifts are the backbone of many industries such as warehousing, logistics, manufacturing, ports, and construction sites. They handle heavy materials, move products to storage, and keep the flow of goods smooth and fast. However, these machines go through a lot of stress every day. When they suddenly stop working, even for a few hours, the whole operation comes to a standstill. Downtime means delayed deliveries, idle manpower, and a direct impact on cost and efficiency.
To avoid these issues, regular attention to forklift health is essential. Preventive Maintenance is a planned method where forklifts are inspected and serviced on a routine basis. Instead of waiting for a breakdown, you solve smaller issues before they grow.
In this article, we will explain what preventive maintenance means for forklifts, why it matters, a detailed checklist that you can follow step by step, and a few helpful tips to manage this process in an organised way.
Why is forklift preventive maintenance important?
Preventive maintenance for forklifts is the act of carrying out scheduled inspections and services to keep the equipment safe, reliable, and ready for daily use. The focus is on identifying wear and tear early, replacing parts before they fail, and ensuring the machine stays in good working condition. These checks can be daily, weekly, monthly, or quarterly depending on how heavily the forklift is used.
Neglecting this regular care can lead to serious consequences. Machines that are not inspected on time develop mechanical faults that can suddenly appear in the middle of operations. This can be dangerous for operators, damage goods being transported, and create unnecessary expenses.
Well-managed preventive maintenance increases the life of forklifts, reduces emergency repairs, and improves workplace safety. It also helps businesses maintain a consistent level of productivity.
Forklift preventive maintenance checklist
Forklifts consist of different systems – engine, hydraulics, electrical circuits, safety equipment, and load-bearing parts. All these need equal attention. Following a checklist makes the process organised and ensures no critical part is skipped. Below is a detailed checklist that combines both daily operator checks and scheduled professional inspections.
1. Daily visual inspection
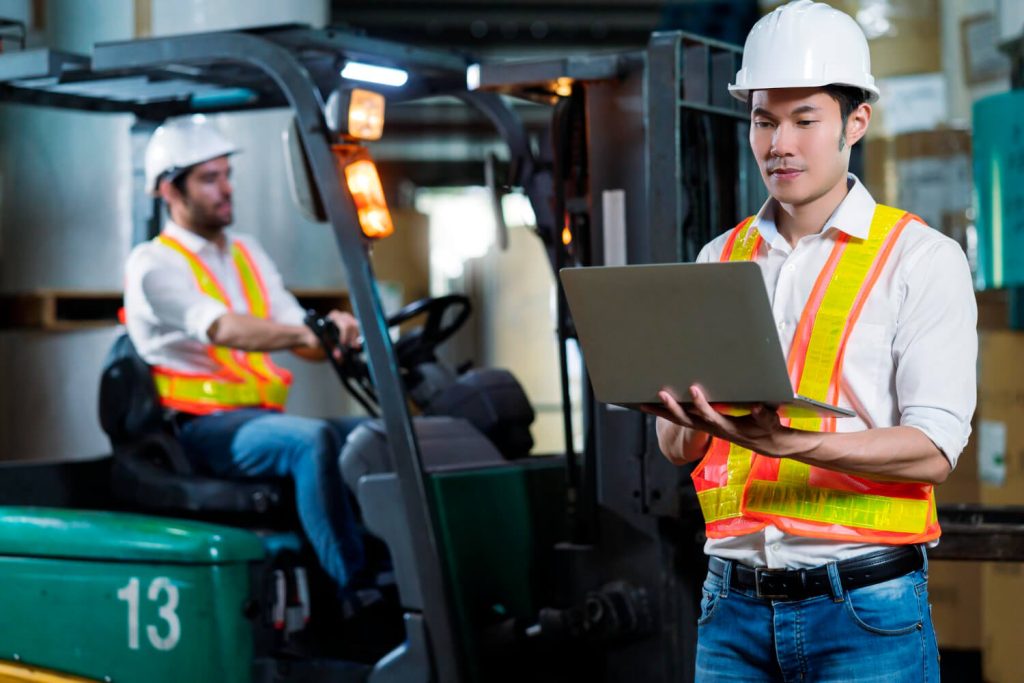
This is the first step at the start of every work shift. A quick walk-around check helps operators notice obvious problems before operating the forklift. It is a simple practice that avoids unsafe conditions.
- Inspect tyres for cuts, cracks, low air pressure, or uneven wear
- Look for oil stains under the forklift that may indicate a leak
- Examine forks for visible bends, cracks, or chipped edges
- Check if the mast is straight and chains are properly aligned
2. Fluid levels and leaks
A forklift runs smoothly only when fluids such as engine oil and hydraulic oil are at the correct levels. These also keep the machine cool and reduce friction.
- Check engine oil and transmission oil levels regularly
- Inspect hydraulic oil to ensure there is enough for lifting operations
- Top up coolant to prevent the engine from overheating
- Look underneath the machine for any signs of leaking fluids
3. Safety features and controls
Safety components are designed to protect both the operator and the load. If any of these are not working correctly, it can lead to serious hazards.
- Test the working of the service brake and parking brake
- Make sure the horn and warning alarms are working
- Check if all lights, indicators, and reverse beepers are functional
- Ensure the operator’s seat belt and restraint system are secure
4. Electrical system inspection
Electric parts in a forklift include batteries, wiring, and control circuits. Problems in these systems can cause unexpected stoppages or even fires if left unchecked.
- Inspect the battery terminals for signs of rust or corrosion
- Make sure the battery water level is maintained in wet-cell batteries
- Check for loose or exposed wires that might be dangerous
- Ensure alternators, relays, and starter circuits are operating normally
- Confirm charging systems work correctly after each shift
5. Forks and mast function
The forks and mast do all the heavy lifting, so they need to be examined closely. If these parts fail, the risk of accidents is very high.
- Measure fork thickness to ensure it is not worn out beyond limits
- Check that the fork locking pins are in place and working
- Examine mast rollers for flat spots and smooth rolling
- Check hydraulic hoses connected to the mast for cracks
- Inspect lift chains for rust, stretch marks, or broken links
6. Scheduled professional servicing
While daily checks can be done by operators, more detailed servicing must be handled by trained technicians. Professional servicing involves thorough checks and replacement of parts that cannot be done during daily inspections.
- Replacement of engine oil, hydraulic oil, and filters after set intervals
- Adjusting mast alignment, chain tension, and lifting systems
- Checking engine compression and running diagnostic scans
- Inspecting structural parts for cracks in the frame or overhead guard
- Examining exhaust systems for leaks and emissions control
- Updating all service logs so that future maintenance is easy to plan
Tips for effective forklift maintenance management
Managing forklift maintenance becomes easier when there is a proper system in place. Instead of waiting for unexpected faults, a planned routine keeps the machines ready for work every day. Good management not only reduces sudden breakdowns but also saves costs by extending the life of parts and improving safety on site.
A clear approach involves creating schedules, training operators, and tracking every check in an organised way. The following points can guide you in building an effective maintenance plan that works across different types of forklifts.
- Create a fixed inspection calendar and stick to it
- Train operators to report faults as soon as they appear
- Keep a stock of frequently used spare parts
- Use checklists for daily, weekly, and monthly inspections
- Assign responsibilities so tasks are never missed
- Document all work done on each forklift for easy reference
- Review service history before planning major repairs
- Avoid overloading the forklift beyond its rated capacity
- Rotate machines so wear and tear is evenly distributed
- Set performance benchmarks to track machine efficiency
How does TeroTAM help you with forklift preventive maintenance?
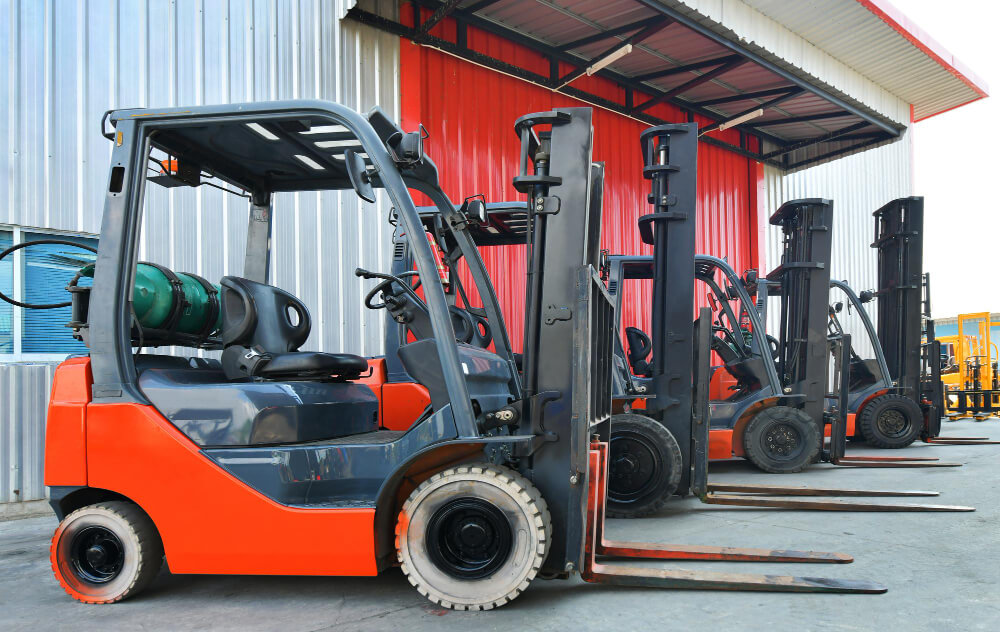
Coordinating preventive maintenance for forklifts across busy facilities requires more than manual records and reminder notes. Delayed inspections, poor documentation, and reactive repairs can quickly affect uptime. A digital maintenance platform like TeroTAM CMMS introduces a structured way to plan, track, and manage every step of the maintenance cycle for forklifts.
TeroTAM functions as a central system where scheduling, tracking, and reporting are connected in real time. It covers the full process from creating preventive service plans to tracking costs, keeping the condition of every forklift visible to both technicians and management teams. This approach reduces unplanned breakdowns and ensures that preventive actions are carried out at the right intervals.
- Preventive maintenance scheduling – Create automated service cycles for daily, weekly, monthly, and usage-based inspections so no forklift is overlooked.
- Work order management – Convert service tasks into digital work orders, assign them to technicians, and track status updates without manual follow‑ups.
- Asset tracking module – Maintain a digital record of every forklift, including age, operating hours, warranty, service history, and upcoming tasks.
- Inventory and parts control – Monitor spare parts availability, set reorder levels, and avoid downtime due to unavailable components.
- Mobile technician access – Use a mobile app to scan asset QR codes, upload inspection photos, complete checklists, and close work orders instantly.
- IoT-based monitoring – Connect sensors to track run‑time, temperature, and fault alerts from forklifts for condition‑based servicing.
- Checklist and document management – Store standard operating procedures, inspection forms, and manuals so technicians can follow proper steps without searching for files.
- Analytics and reporting tools – Generate reports for downtime, costs, and frequency of issues to make informed decisions about fleet utilization and replacement planning.
- Multi-site control panel – Get a single view of maintenance activities across different locations and manage service compliance centrally.
- Compliance-ready record keeping – Keep accurate service logs that help meet safety audits and ISO maintenance documentation requirements.
These features work together to keep every forklift in the fleet under active supervision. Maintenance becomes predictable, downtime reduces, and asset life improves without depending on paper records or manual tracking.
Conclusion
Forklift preventive maintenance may look like an extra task, but it saves you from sudden breakdowns and keeps your operations smooth. Regular checks and servicing mean your forklifts will run better, last longer, and keep your team safe.
The effort you invest today in a proper checklist pays back in reduced downtime, fewer accidents, and more reliable performance. Start following a plan and see the difference it makes in your warehouse or factory.For more information or to explore how TeroTAM can help automate your forklift maintenance schedule, write to contact@terotam.com.