Power plant maintenance requires a system-level approach to manage the complexity of interconnected assets operating under continuous load. Each asset—from turbines and boilers to transformers and switchgear—has specific service intervals, safety thresholds, and operational dependencies that must be tracked and executed with discipline. In the absence of a centralized platform, maintenance efforts often rely on fragmented data and reactive workflows, leading to inefficient resource use, extended downtimes, and audit-related risks.
A CMMS offers a unified environment to automate maintenance schedules, record asset histories, allocate workforce intelligently, and ensure complete traceability of all activities. It enables better visibility into operational risks and allows maintenance managers to act proactively using accurate, real-time data. The result is a well-coordinated system where maintenance tasks are predictable, asset degradation is better controlled, and compliance is consistently aligned with operational needs.
In this article, we’ll explore the common maintenance challenges faced by power plants and how a CMMS addresses them through structured planning, automation, and data-driven execution.
Common Challenges in Power Plant Maintenance
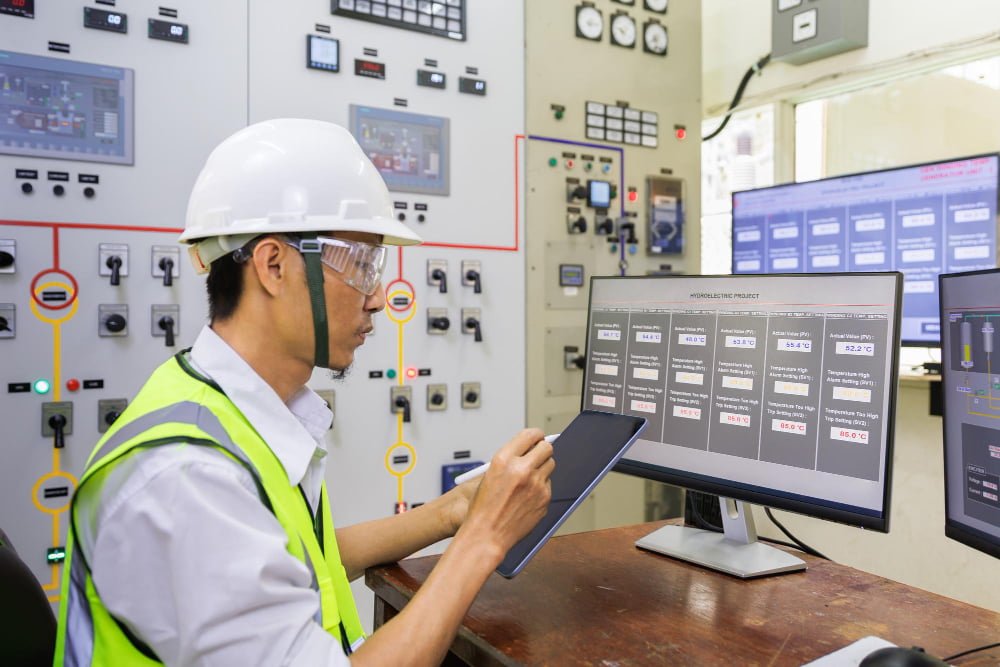
Power plants operate under non-stop pressure. Whether it’s thermal, nuclear, hydro, or gas-based, the complexity of systems and the high cost of downtime mean maintenance isn’t optional—it’s critical. But even with large teams and technical staff, keeping everything running smoothly without proper tools can feel like a losing battle.
In many plants, maintenance practices still rely on outdated methods like paper logs or siloed spreadsheets. This not only slows down work but makes it harder to spot issues before they spiral into emergencies. Below are some of the most common hurdles maintenance teams face in power plants:
1. Unplanned equipment failures
Unexpected breakdowns in turbines, transformers, pumps, or control panels can bring operations to a halt. Without condition-based alerts or predictive insights, most maintenance becomes reactive rather than planned.
2. Incomplete maintenance history
Lack of access to asset history makes it hard for technicians to understand recurring issues. Guesswork replaces data-driven diagnosis, often leading to temporary fixes instead of long-term solutions.
3. Spare parts mismanagement
Without real-time inventory tracking, technicians either overstock unnecessary parts or face delays because critical components are missing when needed most.
4. Compliance and audit pressure
Power plants are regularly audited for safety, environmental, and operational compliance. Missing records or skipped inspections can lead to hefty penalties or reputational damage.
5. Coordination gaps between teams
Mechanical, electrical, and instrumentation teams often work in silos, leading to communication breakdowns and overlapping or missed maintenance tasks.
6. Labour productivity issues
When technicians waste time locating paperwork, figuring out job priorities, or walking back and forth for tools and instructions, efficiency drops and downtime increases.
How CMMS addresses Power Plant Maintenance Challenges
Managing a power plant without structured systems is like trying to fix a machine while it’s running. There’s no time to pause, yet everything needs attention—right now. A CMMS changes the game by turning maintenance into a well-orchestrated process instead of a race against failures. It brings predictability, transparency, and responsiveness to every maintenance activity, helping teams stay in control instead of constantly playing catch-up.
Here’s a deeper look at how CMMS helps solve key maintenance challenges across the power plant:
1. Preventive maintenance automation
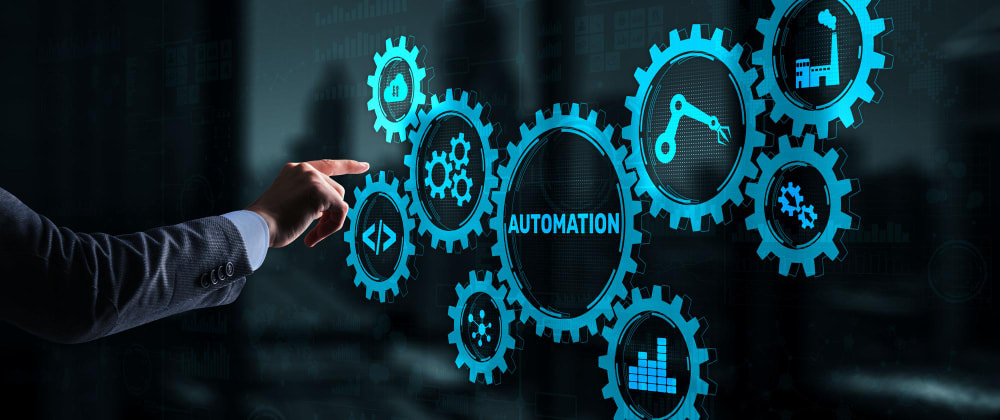
In a power plant, unplanned downtime can cost thousands of dollars per minute and affect entire grids. CMMS helps avoid this by automating preventive maintenance tasks across all critical systems. It builds a structured plan for each asset, triggers timely service alerts, and ensures nothing slips through the cracks—whether it’s a turbine oil change or a high-voltage panel check.
- Automatically schedules tasks based on calendar, runtime, or meter readings
- Assigns recurring jobs to specific technicians with time buffers for delays
- Notifies supervisors if a scheduled task is overdue or skipped
- Tracks completion history to fine-tune future frequencies
2. Streamlined asset management
Every asset in a power plant—from generators to cooling systems—requires individual tracking. A CMMS centralizes asset profiles, allowing maintenance teams to view complete service history, manuals, photos, and warranty details at any time. This removes guesswork, speeds up troubleshooting, and supports better decision-making for asset lifecycle management.
- Creates a digital profile for each asset with technical specs and service logs
- Connects assets to their related parts, locations, and vendors
- Flags assets with frequent failures or rising maintenance costs
- Tracks warranty periods to avoid unnecessary spend
- Stores manuals and maintenance SOPs for on-the-spot technician use
3. Real-time inventory tracking
Without proper inventory visibility, technicians often run into delays or excess costs due to missing or overstocked parts. CMMS links your inventory directly to the work order system, so you always know what’s available, what’s needed, and what’s about to run out. This eliminates blind spots and ensures maintenance is never held back due to spare parts issues.
- Monitors live stock levels for each part in multiple locations
- Triggers auto-reorder requests when items reach minimum thresholds
- Flags unused or slow-moving inventory to avoid wastage
- Links parts usage directly to equipment and job history
- Tracks supplier performance and delivery timelines
- Supports batch tracking and serial number records
4. Mobile-enabled workforce
When technicians can access and update maintenance data from the field, efficiency shoots up. CMMS with mobile functionality turns smartphones and tablets into powerful maintenance tools. It eliminates paperwork, improves field coordination, and allows technicians to solve problems faster by accessing asset info, task instructions, and service history wherever they are.
- Allows technicians to receive, start, and close tasks from the mobile app
- Supports photo uploads and digital signatures for task proof
- Enables field access to equipment manuals and past reports
- Updates task status in real-time for supervisors to track progress
- Sends push notifications for urgent repairs or alerts
- Records GPS and timestamp data for better accountability
- Allows field comments to be added directly into the job log
5. Improved regulatory compliance
Power plants face tight regulations across safety, environmental, and operational standards. CMMS simplifies compliance by automating inspection schedules, maintaining clean digital logs, and keeping documentation audit-ready. This ensures your plant is always prepared for external audits or internal reviews without last-minute chaos.
- Schedules and tracks recurring safety inspections and legal checks
- Stores calibration and testing certificates for easy retrieval
- Flags overdue inspections and pending compliance reports
- Maintains digital logs of who did what, when, and on which equipment
- Supports checklists and standard operating procedures for every task
- Exports audit reports with asset-wise or department-wise filters
6. Interdepartmental coordination
In power plants, mechanical, electrical, and control systems teams often work in parallel but not always in sync. CMMS creates a shared space where all departments view the same data, track cross-functional jobs, and avoid duplication. This improves transparency, reduces delays, and fosters smoother handoffs between teams.
- Assigns tasks to departments or individuals with role-based access
- Maintains a shared dashboard showing task status and overlaps
- Allows inter-team communication through internal notes or comments
- Links shared assets to all departments that interact with them
- Flags schedule conflicts or dependency clashes in maintenance plans
- Keeps all documents centralized so no team works with outdated info
- Enables shared calendars for shutdowns, overhauls, or inspections
7. Data analytics and reporting
CMMS turns your maintenance data into meaningful insights. It goes beyond record-keeping to highlight trends, inefficiencies, and opportunities. From asset reliability scores to technician performance reports, CMMS helps management stay informed and make smarter decisions that improve both short-term performance and long-term planning.
- Tracks mean time to repair (MTTR) and mean time between failures (MTBF)
- Identifies top cost drivers across assets and departments
- Generates monthly performance reports by location or asset category
- Forecasts maintenance workload and spare parts demand
- Highlights technician response times and work order closure rates
- Helps plan budgets by analysing past maintenance spend
- Supports data exports for integration with ERP or finance systems
CMMS Implementation tips for Power Plants
Adopting a CMMS is not just about installing software. It requires a clear process and team collaboration to make it truly effective.
Start with asset hierarchy
Map out all equipment, locations, and systems clearly. This gives the CMMS a structure to work with and ensures accurate tracking.
Define maintenance types
Separate routine, preventive, emergency, and predictive tasks. Each should have its own workflow and scheduling logic in the CMMS.
Train the team
Technicians, supervisors, and managers must be trained not just on how to use the software, but how to adapt their roles around it.
Connect inventory and procurement
Sync your CMMS with the warehouse and vendor management systems to enable real-time updates and streamlined ordering.
Review and adjust regularly
Check reports and system usage monthly. Adjust schedules, roles, or thresholds as the system evolves with your plant’s needs.
Summing it up
Managing power plant maintenance without a smart system is like working in the dark—when equipment fails, it can lead to costly downtime and unpredictable outcomes. A CMMS helps eliminate these risks by providing the tools needed to plan maintenance efficiently, streamline operations, and maintain complete control over asset health. If you’re looking to improve your plant’s maintenance strategy and bring more reliability to your operations, TeroTAM is here to assist. Reach out to us at contact@terotam.com to learn how our CMMS can be the solution your power plant needs.