Do you get mixed up when people talk about Standard Operating Procedures and Work Instructions? No need to worry! These are just tools to help workers do their jobs properly.
Think of it this way – you work at a factory that makes cars. The Standard Operating Procedure is like the main instructions that say to build the car body, install the engine, add the wheels and do the painting. The Work Instruction is the detailed guide that shows you exactly how to do each little task step-by-step, like how to operate the welding machine or how to properly paint the car.
The main instructions (SOP) tell you the important things to do. The detailed guide (Work Instruction) tells you how to actually perform each task correctly. Together, they make sure every car gets built perfectly every time!
SOPs and Work Instructions help factory workers and other employees do things the right way, so products turn out great.
Let’s look closer at what these helpful tools are all about.
Standard Operating Procedures and Work Instructions
In manufacturing and operational environments, Standard Operating Procedures (SOPs) and Work Instructions (WIs) are crucial documents that guide the execution of tasks and processes. While they are often used interchangeably, there are distinct differences between the two.
What are Standard Operating Procedures?
Standard Operating Procedures (SOPs) are high-level documents that provide an overview of a particular process or operation. They outline the steps involved, define the scope, and establish guidelines for consistent execution. SOPs typically answer the “what” and “why” questions regarding a process.
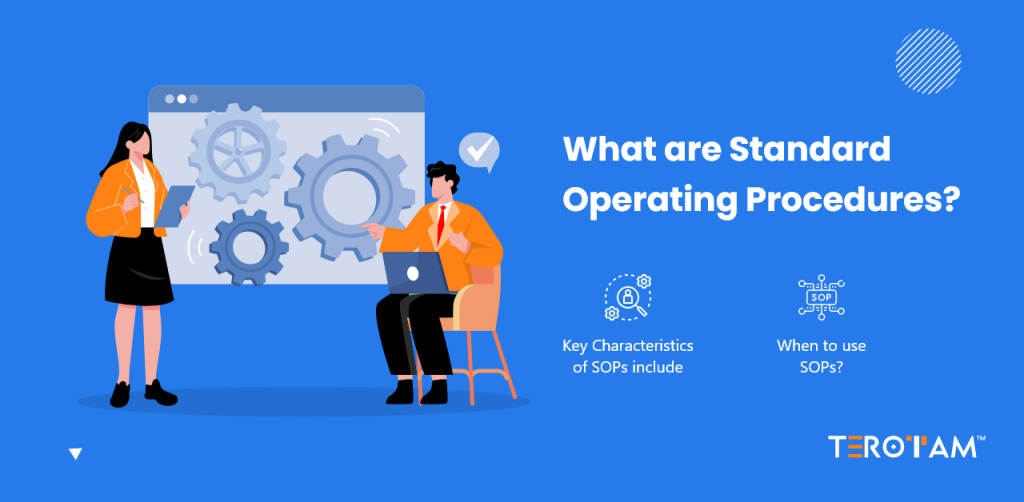
Key Characteristics of SOPs include:
- Broad scope: SOPs cover the entire process from start to finish.
- Regulatory compliance: SOPs help ensure adherence to industry regulations and best practices.
- Quality control: They establish standards for quality and consistency.
- Safety measures: SOPs often include safety protocols and precautions.
SOPs serve as a framework, providing a roadmap for various operations within an organization.
When to use SOPs?
SOPs should be employed in the following situations:
- Establishing a standardized approach: SOPs are essential when you need to define a consistent and uniform way of executing a process across different teams, locations, or shifts.
- Ensuring regulatory compliance: SOPs are critical when your organization needs to comply with industry regulations, standards, or legal requirements.
- Implementing quality control measures: SOPs help establish quality control guidelines and procedures to maintain consistent product or service quality.
- Mitigating risks and ensuring safety: SOPs can incorporate safety protocols, risk assessments, and mitigation strategies to protect employees and operations.
- Facilitating training and onboarding: SOPs serve as valuable reference documents for training new employees and ensuring consistent knowledge transfer.
- Managing change: SOPs provide a framework for implementing and documenting changes in processes or operations, ensuring a smooth transition.
What are Work Instructions?
Work Instructions (WIs) are detailed, step-by-step guides that explain how to perform specific tasks or activities within a process. They provide granular instructions, leaving no room for ambiguity.
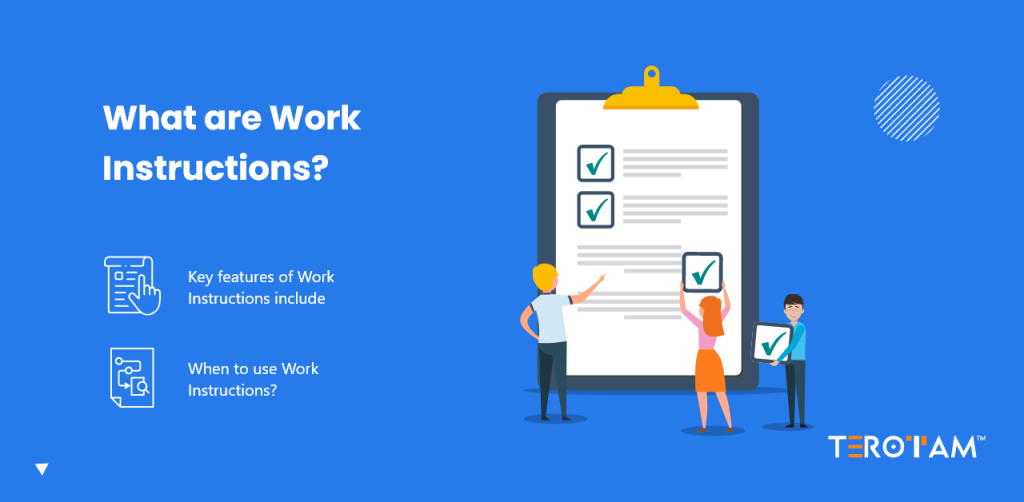
Key features of Work Instructions include:
- Task-specific: WIs focus on individual tasks or activities within a larger process.
- Detailed steps: They break down tasks into sequential, easy-to-follow steps.
- Visual aids: WIs may include diagrams, illustrations, or photographs for clarity.
- Training and knowledge transfer: WIs facilitate consistent training and knowledge sharing.
Work Instructions are the “how-to” guides that complement SOPs, ensuring consistent and accurate execution of tasks.
When to use Work Instructions?
Work Instructions should be utilized in the following scenarios:
- Detailed task execution: WIs are necessary when specific tasks or activities within a larger process require detailed, step-by-step instructions to ensure consistent and accurate execution.
- Complex or critical tasks: WIs are crucial for tasks that are intricate, high-risk, or have a significant impact on quality, safety, or operational efficiency.
- Training and knowledge transfer: WIs facilitate consistent training and knowledge sharing, ensuring that tasks are performed accurately and uniformly across different teams or individuals.
- Troubleshooting and maintenance: WIs provide detailed guidance for troubleshooting, repair, and maintenance activities, reducing the risk of errors or deviations.
- Compliance with specific requirements: WIs can be used to document compliance with specific regulatory requirements or industry standards related to task execution.
- Infrequent or new tasks: WIs are particularly useful for tasks that are performed infrequently or are new to the organization, minimizing the risk of errors or inconsistencies.
What will be more useful in the case of Maintenance Management?
Work Instructions (WIs) are likely to be more useful and applicable compared to Standard Operating Procedures (SOPs) when we plan to use them for the maintenance management tasks.
Maintenance operations often involve a wide range of specific tasks and activities that require detailed, step-by-step guidance to ensure accurate and consistent execution. These tasks can range from preventive maintenance routines, equipment inspections, troubleshooting procedures, repair activities, and various other maintenance-related tasks.
Here’s why Work Instructions are particularly valuable in maintenance management:
- Detailed task execution: Maintenance tasks are often complex and intricate, involving multiple steps and specific techniques. WIs provide the necessary granular instructions to guide technicians through each step, minimizing the risk of errors or deviations.
- Equipment-specific instructions: Different types of equipment or machinery may require unique maintenance procedures. WIs can be tailored to provide specific instructions for each piece of equipment, ensuring that technicians follow the appropriate steps for that particular asset.
- Safety and risk mitigation: Many maintenance activities involve potential safety risks, such as working with hazardous materials, heavy machinery, or high-voltage systems. WIs can incorporate detailed safety protocols, precautions, and risk mitigation measures to protect maintenance personnel and facilities.
- Troubleshooting and diagnostics: When equipment malfunctions or issues arise, WIs can provide step-by-step troubleshooting procedures and diagnostic guidelines to aid technicians in identifying and resolving problems efficiently.
- Training and knowledge transfer: WIs serve as valuable training resources for new maintenance technicians or when introducing new equipment or procedures. They ensure consistent knowledge transfer and help maintain uniform maintenance practices across teams.
While SOPs may still have a role in maintenance management, such as outlining overarching maintenance policies, schedules, or quality control measures, the detailed guidance provided by work instructions will greatly benefit the bulk of maintenance-related tasks.
Adopting comprehensive and well-documented Work Instructions, maintenance teams can improve operational efficiency, minimize downtime, extend equipment lifespan, and enhance overall maintenance effectiveness while ensuring consistent quality and adherence to safety standards.
Summing it up,
SOPs and Work Instructions are great helpers for your job. SOPs give you the big picture of what needs to be done. Work Instructions give you all the little details on how to do each task properly. When you use both together, it’s like having a guidebook that shows you the way.
Seems like you want to know more about what and how to use in your specific use case? – connect with our expert now or write us at contact@terotam.com