Traditional asset maintenance often relies on reactive or scheduled servicing, which can lead to inefficiencies, unexpected breakdowns, and high operational costs. IoT sensors are transforming this process by enabling real-time monitoring, predictive analytics, and automation. Businesses can now collect data on asset performance, detect early signs of failure, and schedule maintenance when needed rather than following fixed schedules. This shift not only improves equipment reliability but also reduces downtime and maintenance expenses.
Companies across industries are moving toward sensor-driven maintenance strategies to ensure that assets operate efficiently. Whether it is manufacturing plants optimizing machinery, logistics firms maintaining fleet health, or hospitals ensuring medical devices remain operational, IoT technology is making maintenance smarter and more efficient.
This article explores how these sensors work, their benefits, the challenges in adoption, and how different industries are using them to transform asset maintenance.
Core Technologies enabling IoT-based Asset Maintenance
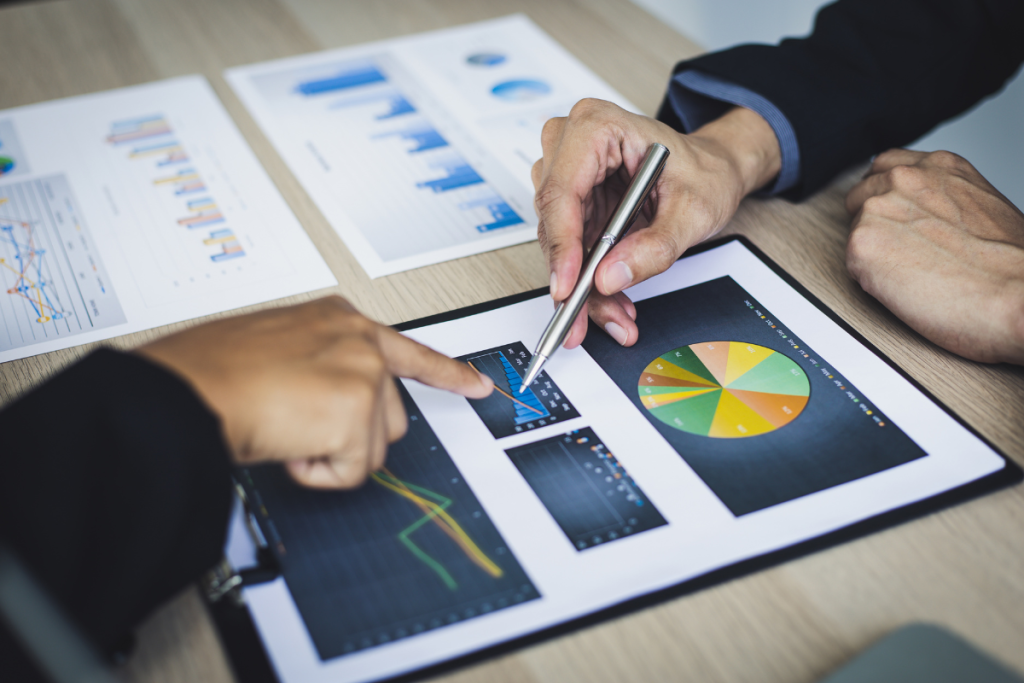
IoT-driven asset maintenance is powered by a combination of hardware and software technologies. Understanding these components is essential for industries planning to implement sensor-based maintenance strategies.
1. IoT sensor types and their functions
Different types of sensors play a crucial role in monitoring the health and performance of assets. Some commonly used IoT sensors include:
- Vibration sensors – Detect mechanical imbalances, misalignments, and early signs of component degradation in rotating equipment.
- Temperature sensors – Monitor thermal fluctuations in machinery, preventing overheating and potential failures.
- Humidity sensors – Measure moisture levels to prevent corrosion, mold growth, and degradation of sensitive equipment.
- Pressure sensors – Track fluid and gas pressure to ensure pipelines and hydraulic systems operate within safe limits.
- Acoustic sensors – Capture ultrasonic signals to detect leaks, electrical discharges, or cavitation in industrial systems.
- Proximity sensors – Detect the movement or position of mechanical components, ensuring proper alignment and function.
- Oil quality sensors – Analyze lubricant properties in engines and gearboxes, preventing failures due to contaminated or degraded fluids.
Each of these sensors continuously collects data, which is processed to identify trends, anomalies, and potential failures before they occur.
2. Edge computing and real-time data processing
Traditional IoT architectures rely on cloud-based platforms for data storage and analysis. However, edge computing is enhancing the efficiency of IoT-driven maintenance by enabling on-device data processing.
- Reduced latency – By processing data at the sensor or gateway level, edge computing minimizes delays in detecting and responding to critical asset conditions.
- Bandwidth optimization – Instead of transmitting raw data to the cloud, edge devices filter and analyze relevant information locally, reducing network congestion.
- Improved reliability – On-premises data processing ensures that maintenance operations continue even if cloud connectivity is temporarily lost.
Edge computing is particularly beneficial for industrial environments where immediate action is required to prevent asset failures.
3. AI-driven predictive analytics and failure forecasting
Predictive maintenance relies on machine learning algorithms to analyze sensor data and forecast potential failures. AI models identify patterns and correlations that indicate wear and tear, enabling businesses to:
- Estimate remaining useful life (RUL) – Predict when a component is likely to fail, allowing for timely replacements.
- Reduce false alarms – Advanced analytics differentiate between normal operational fluctuations and actual faults.
- Optimize maintenance schedules – AI-driven insights help organizations schedule maintenance based on real-time asset conditions rather than fixed intervals.
These capabilities allow industries to implement data-driven maintenance workflows that minimize downtime while extending asset lifespan.
4. Digital twin technology for asset simulation
Digital twins are virtual models of physical assets that integrate real-time sensor data to simulate performance, predict failures, and optimize maintenance strategies. Benefits of using digital twins in asset maintenance include:
- Scenario testing – Simulate different maintenance approaches to determine the most effective strategy.
- Remote asset monitoring – Visualize real-time asset conditions without physical inspections.
- Lifecycle management – Track asset health from commissioning to decommissioning, ensuring optimal performance throughout its lifespan.
Digital twin technology is particularly valuable in industries such as aerospace, energy, and smart manufacturing, where complex equipment requires precise monitoring and predictive maintenance.
5. IoT-driven automated maintenance workflows
IoT sensors enable automation in asset maintenance through interconnected systems that trigger maintenance actions based on real-time data. Key automation processes include:
- Automated work order generation – When a sensor detects an anomaly, maintenance management software automatically creates a service request.
- Predictive part replacement – AI-driven insights determine when components need replacement, ensuring spare parts are available in advance.
- Self-healing systems – Some IoT-enabled systems can automatically recalibrate or adjust settings to correct minor issues without human intervention.
These automated workflows enhance efficiency, reduce manual oversight, and minimize the risk of unexpected failures.
How IoT sensors Enhance Asset Maintenance?
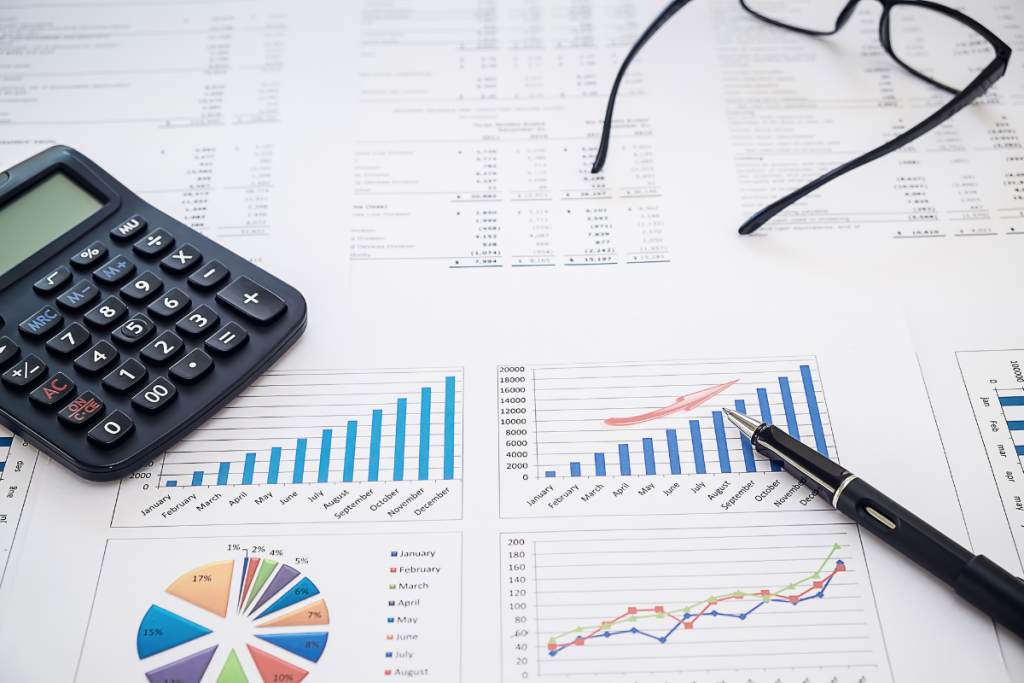
IoT sensors collect and transmit real-time data, helping businesses monitor equipment health, environmental conditions, and operational performance. This data-driven approach eliminates guesswork and helps maintenance teams act before issues escalate.
1. Predictive maintenance for early issue detection
Instead of relying on scheduled servicing, predictive maintenance uses IoT sensors to analyze asset health and detect potential failures. Sensors continuously measure factors such as vibration, temperature, pressure, and energy consumption. If abnormal readings indicate a problem, alerts are generated, allowing maintenance teams to intervene before the issue worsens.
2. Condition-based maintenance for targeted servicing
Condition-based maintenance focuses on servicing equipment only when performance indicators show a decline. IoT sensors track real-time conditions such as fluid levels, wear and tear, and component efficiency. If a machine operates within optimal parameters, unnecessary maintenance is avoided, saving costs and reducing downtime.
3. Remote monitoring for asset tracking
IoT sensors enable remote monitoring of assets spread across different locations. Businesses can track machinery, vehicles, and infrastructure in real time, ensuring that any anomalies are detected without the need for manual inspections. This is especially useful for industries with geographically dispersed assets, such as energy, logistics, and construction.
4. Automated alerts and workflow integration
Sensor-driven maintenance systems are integrated with enterprise resource planning (ERP) and computerized maintenance management systems (CMMS). When a sensor detects a potential issue, it automatically triggers work orders, assigns tasks to technicians, and ensures timely intervention. This eliminates delays caused by manual reporting and reduces response times.
Overcoming Challenges in IoT-based Asset Maintenance
While IoT-driven asset maintenance offers significant benefits, industries must address several challenges to ensure successful implementation.
- Cybersecurity risks – IoT devices are potential targets for cyber threats. Implementing end-to-end encryption, network segmentation, and authentication protocols is critical.
- Data integration with legacy systems – Many organizations operate with outdated maintenance management systems that lack IoT compatibility. Upgrading or integrating modern platforms is necessary for seamless data flow.
- Scalability concerns – As IoT adoption grows, businesses must ensure their infrastructure can handle large-scale data collection, storage, and analysis without performance bottlenecks.
- Regulatory compliance – Industries such as healthcare and energy must comply with strict regulations regarding asset monitoring and maintenance. IoT solutions should support audit trails and compliance reporting.
Final thoughts
IoT-enabled maintenance is redefining how industries manage assets by reducing operational risks, minimizing downtime, and optimizing costs. Whether it is manufacturing, healthcare, energy, or logistics, the ability to monitor equipment in real time allows businesses to detect failures before they occur. With advancements in sensor technology and AI-driven analytics, asset maintenance is becoming smarter, more efficient, and cost-effective. Businesses adopting IoT-based maintenance strategies are not only improving operational efficiency but also setting new standards for reliability and performance across various sectors.
Looking forward to seeing how that impacts the asset maintenance in your business? – Let’s talk. Schedule a Call with our experts now or drop us a line at contact@terotam.com