The textile industry is a cornerstone of the global economy, responsible for producing everything from everyday clothing to high-tech fabrics used in specialized applications. This sector relies heavily on complex machinery and high-speed production lines to meet the ever-growing demands of consumers. Any disruption in operations, whether due to equipment failure or inefficient maintenance, can lead to significant financial losses and hinder productivity. Maintenance management, therefore, plays a pivotal role in ensuring seamless operations across the supply chain.
As the industry becomes more integrated with technology, traditional maintenance approaches are being replaced with innovative, data-driven solutions. New tools and systems, such as predictive maintenance and automation, are reshaping how textile manufacturers approach maintenance tasks. In this article, we will check out the latest trends in textile industry maintenance management, focusing on how these advancements help businesses tackle ongoing challenges and improve operational efficiency.
The Role of Maintenance in Textile Industry Efficiency
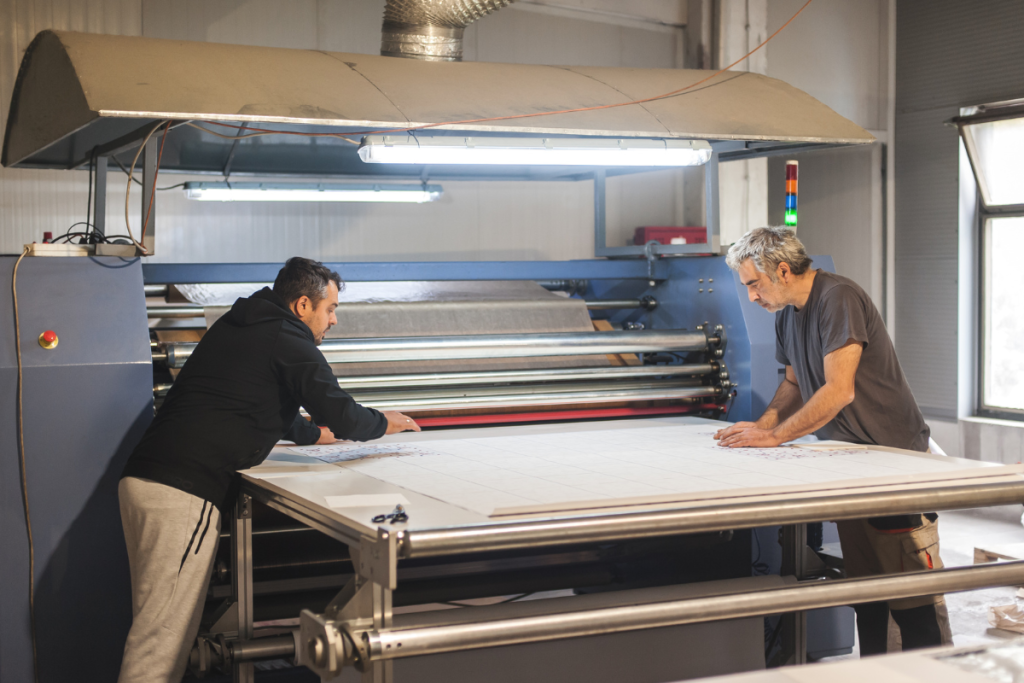
Efficient maintenance in the textile industry has a direct impact on productivity and profitability. With machinery running at high speeds and under constant pressure, regular maintenance ensures that equipment operates smoothly. Timely maintenance prevents costly downtime, allowing production to continue without interruption. In a sector where delays can result in significant financial losses, keeping machines in good working condition is essential for maintaining steady operations.
Maintenance also plays a significant role in ensuring the quality of finished products. Properly serviced machines, such as looms and dyeing equipment, help produce fabrics with consistent quality and standards. When equipment is neglected, defects can occur, leading to poor product quality, rework, or waste materials. Regular maintenance reduces these risks, safeguarding the company’s reputation and profitability.
Energy efficiency is another important benefit of well-executed maintenance. Routine servicing of machinery improves energy consumption, helping to lower operational costs. As the industry continues to focus on sustainability, maintaining energy-efficient equipment supports both cost reduction and environmental goals. This approach not only reduces energy bills but also helps businesses minimize their environmental impact.
Challenges Driving Innovations in the Maintenance of Textile Industry
The textile industry faces challenges that push for innovations in maintenance practices. As machines become more advanced and automated, traditional maintenance methods are no longer enough. The need for smarter systems that can predict failures before they happen has grown, aiming to reduce unplanned downtime and avoid disruptions in production.
Sustainability is another key challenge. With businesses striving to cut their carbon footprint, maintaining energy-efficient machines has become crucial. Many older machines, however, weren’t built with sustainability in mind, creating a gap that requires new maintenance solutions to ensure both operational and environmental goals are met.
- The growing complexity of advanced machinery.
- Need for predictive maintenance to avoid unplanned downtime.
- Increased focus on energy efficiency and sustainability.
- Pressure to reduce costs while maintaining production quality.
- Aging infrastructure requiring modern maintenance solutions.
- Skills gap in the workforce, demanding easier-to-use technology.
- Regulatory requirements for sustainability and compliance.
Emerging Trends in Maintenance Management for the Textile Industry
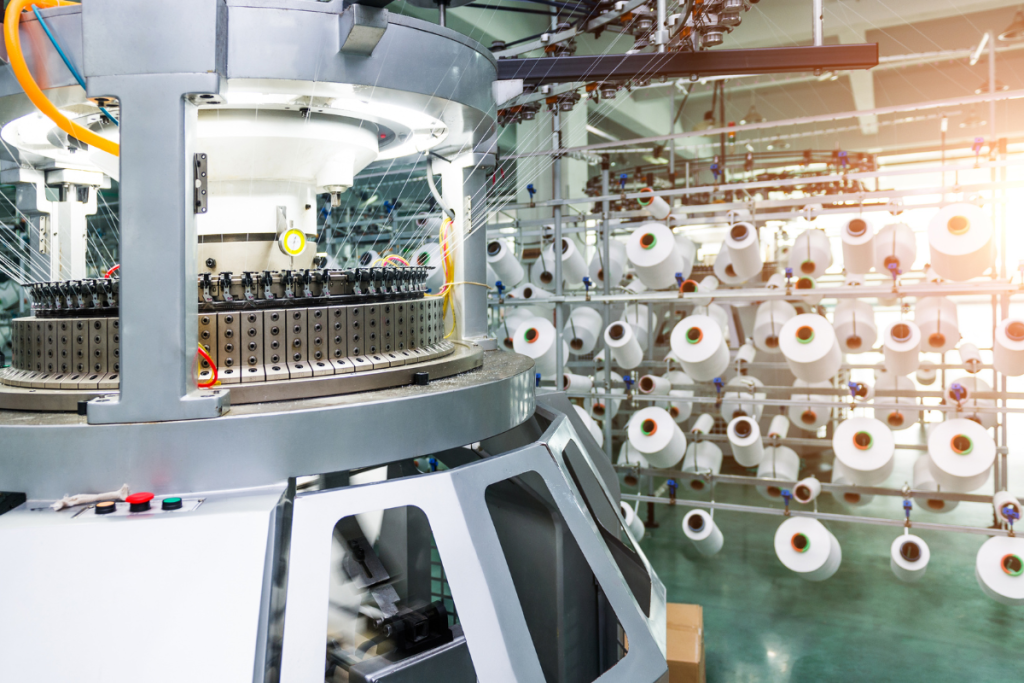
The textile industry’s maintenance management is undergoing a significant transformation, driven by advancements in technology and the need for higher operational efficiency. Manufacturers are adopting more data-driven solutions, automation, and sustainability-focused practices to maintain their competitive edge. Innovations in predictive maintenance, digital tools, and energy efficiency are reshaping how businesses handle their maintenance strategies. These trends not only improve equipment longevity but also contribute to reducing costs and minimizing production disruptions.
Below are the key trends shaping the future of maintenance management in the textile sector:
Predictive Maintenance with IoT and AI
IoT devices and AI technology are revolutionizing maintenance by allowing continuous monitoring of equipment health. Sensors embedded in machinery collect real-time data, which AI systems analyze to predict potential failures. This proactive approach helps address issues before they lead to downtime or costly repairs. Shifting from reactive to predictive maintenance optimizes operations and improves resource management.
- Continuous data collection for real-time monitoring.
- AI-powered failure predictions to prevent breakdowns.
- Enhanced machine lifespan through early detection.
- Minimizes emergency repairs through early warnings.
- Optimizes resource allocation by predicting maintenance needs.
Digital Twins for Maintenance Planning
Digital twin technology enables the creation of virtual replicas of machinery to simulate real-time performance. This innovation helps manufacturers track equipment performance without physically interacting with the machines.
Maintenance teams can anticipate issues and plan maintenance activities more efficiently. Virtual testing of solutions also helps prevent production disruptions, leading to a more streamlined maintenance process.
- Simulates machine behavior to anticipate issues.
- Improves equipment efficiency with data-driven insights.
- Facilitates predictive maintenance without direct interaction.
- Reduces downtime by testing solutions virtually.
Automated Maintenance Systems
Automation is transforming routine maintenance tasks, such as lubrication, cleaning, and calibration, by replacing manual intervention with robotics. Automated systems provide consistent and precise maintenance, minimizing human error and downtime. These systems also improve the lifespan of equipment by maintaining it at optimal performance levels, enhancing operational reliability and reducing long-term costs.
- Automates cleaning, lubrication, and calibration.
- Increases overall operational reliability.
- Reduces the need for manual intervention.
- Extends equipment lifespan with consistent upkeep.
- Reduces downtime with faster maintenance cycles.
CMMS Adoption
Computerized Maintenance Management Systems (CMMS) are essential for organizing maintenance operations. These systems centralize asset performance data, track work orders, and provide maintenance history. With CMMS, manufacturers can plan and execute maintenance tasks more efficiently, ensuring no scheduled maintenance is missed. Detailed analytics and reports from the system help make informed decisions about future maintenance needs.
- Centralizes asset performance data for easy access.
- Tracks work orders and ensures timely execution of maintenance tasks.
- Generates detailed reports to support decision-making.
- Improves resource allocation by optimizing maintenance schedules.
- Enhances team coordination and transparency throughout maintenance activities.
Sustainability-Oriented Maintenance
Sustainability is a growing priority in the textile industry, influencing maintenance practices. Energy-efficient machinery and eco-friendly lubricants are becoming common as businesses aim to reduce their carbon footprint. These practices help meet sustainability goals while also lowering energy consumption and operational costs, contributing to both environmental and economic benefits.
- Reduces operational costs through energy-efficient upgrades.
- Implements eco-friendly lubricants and materials.
Training and Upskilling Through AR/VR
Augmented Reality (AR) and Virtual Reality (VR) technologies are improving maintenance team training. These technologies allow technicians to experience real-world scenarios in a safe, controlled environment. They also provide hands-on practice with complex systems, improving understanding and reducing training time. AR and VR enhance the learning process, resulting in fewer errors and better maintenance outcomes.
- Provides real-time, interactive learning for technicians.
- Reduces training costs and time.
- Improves understanding of complex equipment setups.
- Offers risk-free training scenarios.
Post-Maintenance Analysis and Continuous Improvement
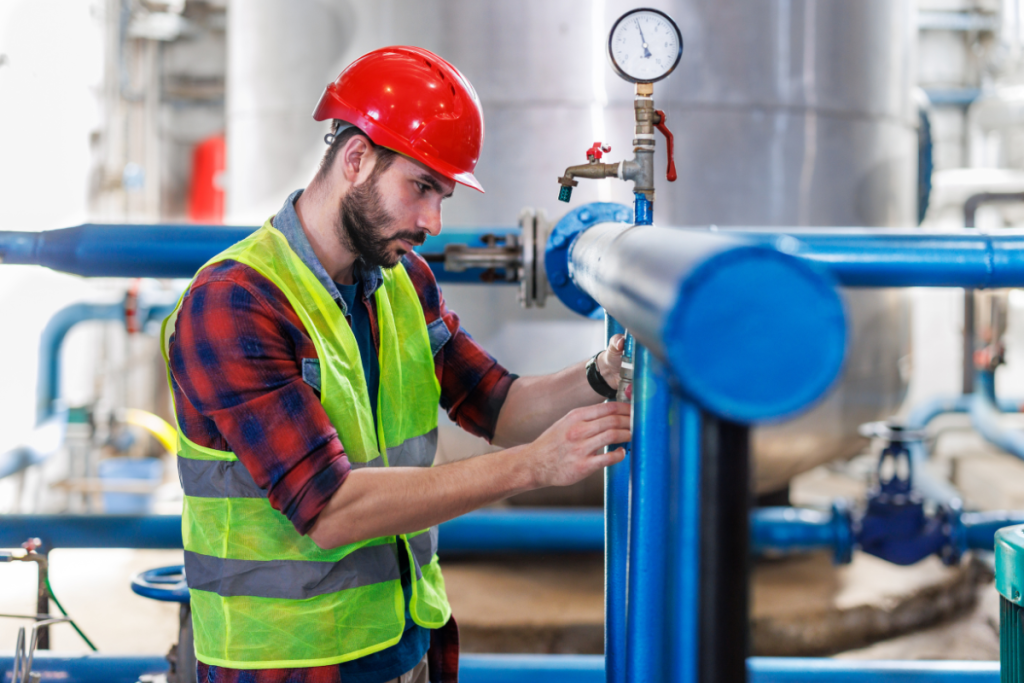
After completing maintenance tasks, it’s important to evaluate their effectiveness through a post-maintenance analysis. This involves reviewing the equipment’s performance to confirm whether issues were addressed and the maintenance objectives achieved. Key metrics such as Mean Time Between Failures (MTBF) and Mean Time to Repair (MTTR) offer insight into the effectiveness of the maintenance work, helping to determine if improvements in uptime and repair time are being achieved.
The analysis helps identify patterns or inefficiencies that can be addressed in future maintenance activities. Low MTBF or high MTTR may indicate that adjustments to the maintenance strategy are needed to improve equipment reliability. This data-driven approach ensures that maintenance efforts are focused on reducing disruptions and enhancing production efficiency.
Continuous improvement thrives on regular evaluation of maintenance outcomes. Regular reviews help refine strategies to prevent recurring issues, reduce downtime, and improve equipment performance. This ongoing cycle of analysis and adjustments leads to more effective maintenance practices and increased operational reliability.
Conclusion
In the textile industry, keeping things running smoothly is no longer just about fixing problems when they happen. It’s about staying ahead of the game with smarter, more efficient maintenance strategies. Using tools like predictive maintenance and automated systems can make a world of difference—helping you reduce downtime, cut costs, and keep equipment running longer. If you’re looking to take your maintenance management to the next level, we’re here to help. Drop us a line at contact@terotam.com and let’s chat about how we can tailor solutions to fit your needs and help your business thrive.