The oil and gas sector operates in a highly volatile and asset-intensive environment, where even minor inefficiencies can lead to production losses, safety hazards, and regulatory challenges. Managing assets effectively requires more than just routine inspections and scheduled maintenance. Advanced data analytics, real-time monitoring, and predictive strategies have reshaped the way companies handle asset performance, reliability, and risk mitigation.
A well-defined asset management framework integrates condition-based monitoring, digital twin technology, and predictive maintenance to enhance equipment longevity and optimize operational costs. This article explores the core strategies that oil and gas companies must implement to achieve reliability, safety, and efficiency in asset management.
What Role Does Strategic Asset Management Play in Oil and Gas Operations?
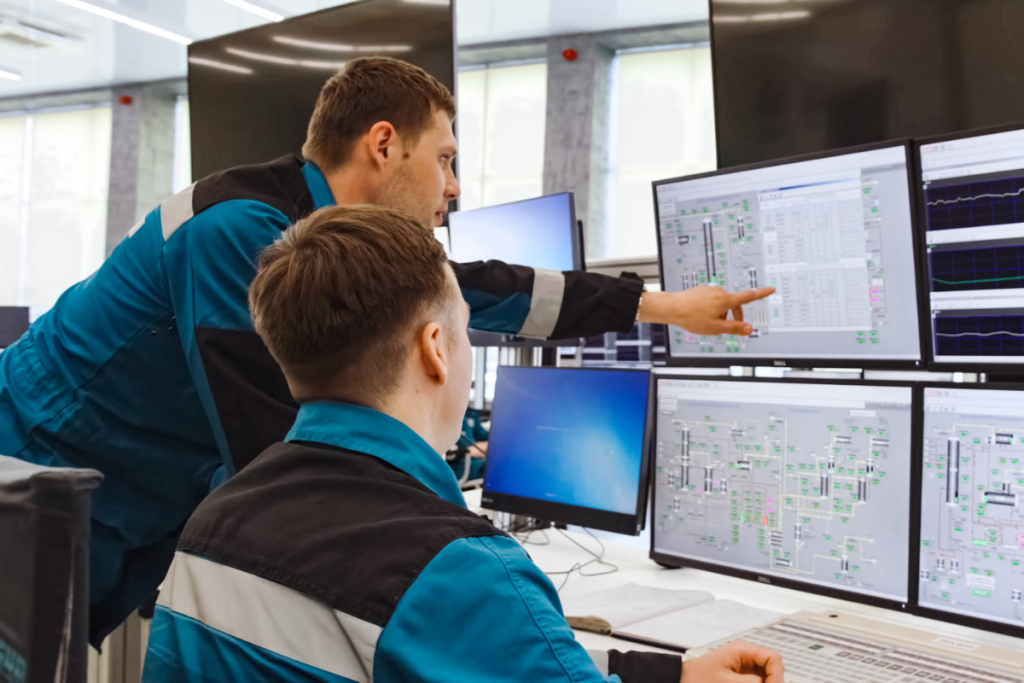
Managing assets in the oil and gas industry requires a balance between reliability, safety, and cost efficiency. With high-value infrastructure spread across remote and harsh environments, unplanned failures can lead to severe financial and operational setbacks.
A structured asset management approach integrates real-time monitoring, predictive analytics, and risk-based assessments to optimize performance. Companies that adopt advanced strategies can extend asset lifespan, reduce downtime, and enhance regulatory compliance.
The Role of Asset Management on Performance of Oil & Gas Industry
Oil and gas operations rely on complex infrastructure, including drilling rigs, refineries, pipelines, and offshore platforms, all of which require continuous oversight. A minor failure in a pipeline valve or compressor can disrupt supply chains, causing financial losses and environmental risks. To prevent such setbacks, asset management focuses on proactive strategies that ensure seamless equipment performance and regulatory adherence.
A robust asset management system optimizes lifecycle costs while maintaining asset integrity. It combines structured maintenance plans, automation technologies, and data-driven decision-making to enhance efficiency and reduce downtime. Companies that fail to implement a systematic approach often struggle with unplanned outages, compliance violations, and increased operational risks.
Most Common Challenges in Asset Management of Oil & Gas Industry
The complexity of oil and gas operations presents unique asset management challenges, requiring specialized solutions:
- Aging Infrastructure & Asset Fatigue: Many assets in the industry have been in service for decades, increasing vulnerability to failures, corrosion, and performance degradation.
- Harsh Environmental Conditions: Offshore and onshore facilities endure extreme temperatures, high pressures, and corrosive substances, accelerating equipment wear.
- Regulatory and Safety Compliance: Strict industry regulations require continuous monitoring and documentation to meet environmental and safety standards.
- Unpredictable Failures & Downtime: Unexpected breakdowns lead to costly repairs, production halts, and reputational damage.
- Data Fragmentation & Integration Issues: Real-time asset health data often remains siloed across multiple systems, limiting visibility and predictive capabilities.
Key Asset Management Strategies for the Oil and Gas Industry
In the oil and gas sector, the right asset management strategies are critical to minimizing risks, reducing operational costs, and enhancing productivity. Given the complexity and high value of assets, companies need to implement proactive, data-driven approaches to ensure reliability and efficiency. The following strategies integrate cutting-edge technologies and best practices, offering companies a way to streamline operations, prevent unplanned downtime, and extend the lifecycle of their assets.
1. Implementing Predictive Maintenance Programs
Unplanned equipment failures in oil and gas facilities not only disrupt production but also pose serious safety hazards. Traditional reactive maintenance methods lead to inefficiencies, as they either under-maintain or over-service assets. Predictive maintenance provides a data-driven approach, enabling real-time monitoring of asset health and early fault detection.
- Deploy AI-driven predictive analytics to assess wear patterns and predict failures before they occur.
- Utilize IoT-enabled sensors to monitor vibration, temperature, and pressure variations in critical equipment.
- Integrate predictive models with Enterprise Asset Management (EAM) systems for automated maintenance scheduling.
- Reduce unnecessary downtime by shifting from calendar-based maintenance to condition-based interventions.
2. Adopting Digital Twin Technology
Managing large-scale oil and gas assets requires a level of operational visibility that conventional methods cannot provide. Digital twin technology creates virtual models of physical assets, simulating real-world conditions to predict failures, test scenarios, and optimize performance.
- Use digital twins to replicate refinery processes, pipeline networks, and offshore platforms for real-time diagnostics.
- Combine IoT, AI, and machine learning to enhance predictive accuracy and failure forecasting.
- Simulate stress scenarios on assets to assess their response under extreme conditions before real-world deployment.
- Enable remote asset monitoring, reducing the need for on-site inspections and improving operational safety.
3. Enhancing Asset Integrity Management
Asset integrity management (AIM) ensures that critical infrastructure operates safely and efficiently throughout its lifecycle. Given the industry’s exposure to corrosive environments and high-pressure systems, AIM strategies must focus on continuous monitoring, risk assessment, and structural resilience.
- Implement risk-based inspection (RBI) methodologies to prioritize high-risk assets and optimize maintenance schedules.
- Utilize advanced non-destructive testing (NDT) techniques such as ultrasonic, eddy current, and infrared thermography for precise defect detection.
- Leverage robotic and drone-assisted inspections for high-risk and inaccessible areas like offshore platforms.
- Integrate corrosion monitoring systems to prevent structural failures in pipelines and storage tanks.
4. Leveraging Condition-Based Monitoring (CBM)
Real-time tracking of asset performance is essential for preventing failures before they disrupt operations. Condition-based monitoring (CBM) involves continuously assessing equipment health through various sensors and diagnostic tools.
- Deploy SCADA (Supervisory Control and Data Acquisition) systems to collect real-time performance data.
- Use machine learning algorithms to analyze asset behavior and detect anomalies in pressure, flow rates, and structural integrity.
- Implement remote condition monitoring for offshore and deep-sea drilling equipment to enhance safety and efficiency.
- Reduce operational risks by replacing reactive maintenance with predictive and condition-based strategies.
5. Strengthening Data-Driven Decision-Making
Data fragmentation across different departments often leads to inefficiencies in asset management. A unified data-driven approach ensures that decision-makers have accurate, real-time insights into asset performance, risks, and maintenance needs.
- Establish centralized asset data repositories to improve cross-functional collaboration and decision-making.
- Use cloud-based platforms for seamless integration of asset performance data across multiple locations.
- Implement AI-driven analytics to detect inefficiencies, reduce energy consumption, and optimize equipment utilization.
- Leverage digital dashboards that provide real-time operational intelligence to field operators and engineers.
6. Investing in Workforce Training and Skill Development
Technological advancements in asset management require a highly skilled workforce capable of leveraging new tools and methodologies. Without adequate training, even the most advanced asset management strategies will fail to deliver expected results.
- Develop training programs focused on predictive maintenance, digital twins, and IoT-based monitoring systems.
- Collaborate with technology providers and academic institutions to enhance workforce expertise in advanced asset management solutions.
- Establish simulation-based training modules that allow engineers to practice real-world asset failure scenarios.
- Promote a culture of continuous learning, ensuring that field operators remain up-to-date with evolving industry best practices.
Best Practices for Sustainable Asset Management in Oil & Gas Industry
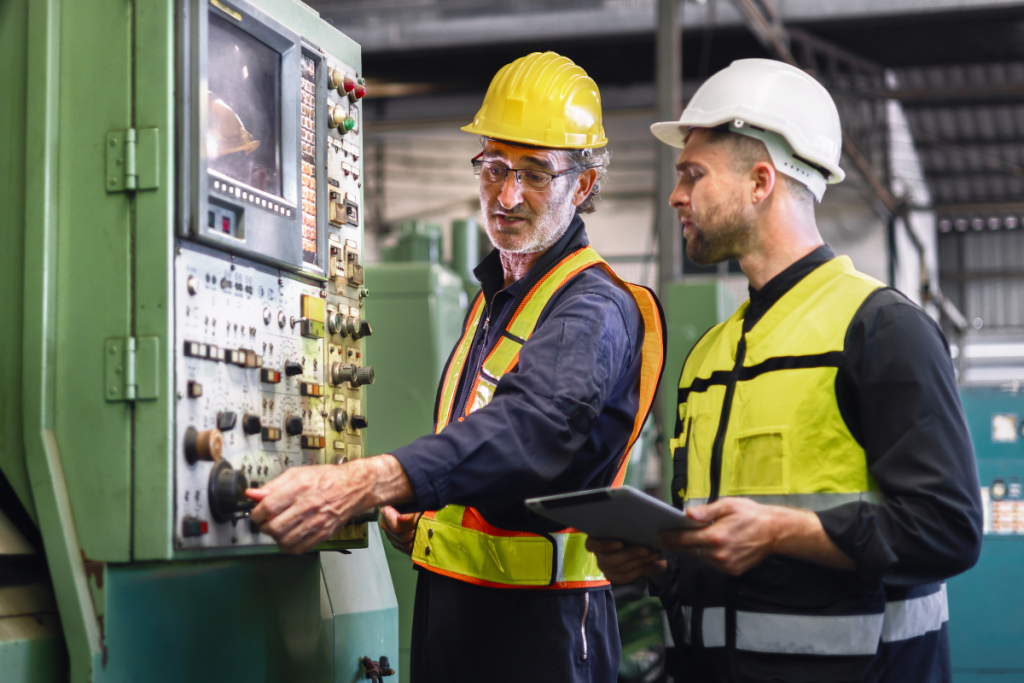
Sustainable asset management goes beyond immediate cost savings; it focuses on long-term performance, environmental responsibility, and operational efficiency. In an industry where assets operate under harsh conditions, applying best practices ensures that companies can extend asset life, reduce environmental impact, and stay compliant with evolving regulations.
The following practices help oil and gas companies enhance sustainability while optimizing performance across their operations.
1. Establishing Standardized Maintenance Procedures
Developing consistent maintenance protocols ensures uniformity and reduces the risk of errors. Standardized procedures not only ensure regulatory compliance but also minimize downtime and prolong asset life.
2. Integrating IoT and Edge Computing
The integration of IoT devices and edge computing allows real-time data collection and analysis directly from assets. This technology helps companies monitor performance continuously and identify potential issues before they lead to failures.
3. Conducting Regular Risk Assessments
Ongoing risk assessments are essential to identify vulnerabilities in both physical infrastructure and operations. A structured risk management framework helps prioritize critical assets and ensures a proactive approach to mitigating potential failures.
4. Promoting a Proactive Safety Culture
A proactive safety culture is crucial in the oil and gas sector, where safety risks are always present. Fostering a safety-focused mindset at every organizational level can prevent accidents, equipment failures, and compliance violations.
5. Leveraging Predictive Analytics for Resource Optimization
Predictive analytics can optimize asset utilization by forecasting when maintenance is required, reducing unnecessary downtime and improving resource allocation.
6. Incorporating Sustainability into Asset Life-Cycle Management
Sustainability should be embedded in every stage of the asset lifecycle, from design and operation to decommissioning. This reduces environmental impact and enhances regulatory compliance while maintaining cost-effective operations.
7. Emphasizing Data-Driven Decision Making
Utilizing data across operations allows companies to make informed decisions regarding asset management and long-term sustainability. A data-driven approach ensures transparency and consistency across the business.
Conclusion
Optimizing asset performance in the oil and gas industry requires more than just routine inspections and maintenance. Implementing predictive maintenance, leveraging digital twins, and utilizing real-time monitoring ensures efficiency and reliability. Every operation can benefit from adopting advanced asset management solutions that reduce costs, enhance safety, and improve compliance. Want to explore tailored asset management strategies for your business? Reach out to us at contact@terotam.com to discuss solutions that align with your operational goals.