Coffee vending machines are no longer a luxury—they’ve become a staple in offices, commercial buildings, hospitals, and public spaces. As their demand grows, so does the need to keep them running smoothly. Any breakdown not only impacts sales but also damages brand reputation and user experience.
Behind each well-functioning vending machine is a network of service, repair, and refilling activities. Managing these tasks manually or through spreadsheets often results in missed service schedules, delays, or poor inventory tracking. That’s where maintenance management software comes into play.
In this article, we’ll cover what coffee vending machines require in terms of maintenance, the common challenges faced by providers, how maintenance management software addresses these issues, key features to consider in such software, and how TeroTAM is assisting leading coffee vending machine brands with their maintenance needs.
Coffee vending machine and its maintenance
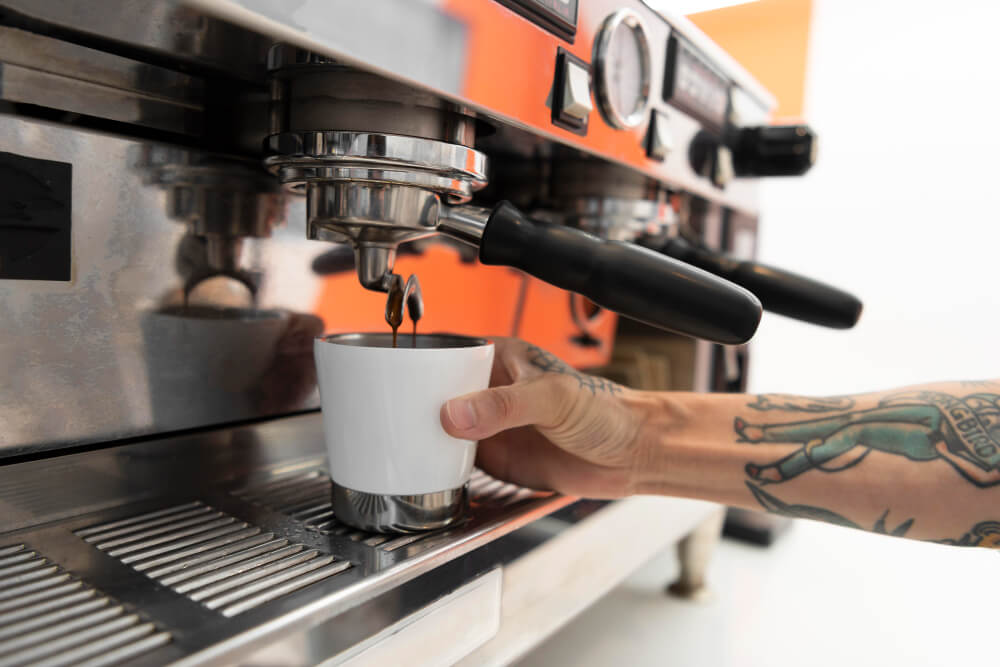
A coffee vending machine might look simple from the outside, but it’s a compact system of electrical, mechanical, and fluid components that must work in sync. These machines need consistent monitoring—water heating elements, mixing motors, cup dispensers, and payment systems all need regular upkeep. Even a minor fault in one module can halt the entire unit.
Maintenance isn’t just about fixing issues; it also includes preventive actions like regular cleaning, replacing consumables, descaling water lines, and calibrating systems to maintain taste consistency. As vending machine fleets grow, managing their upkeep without a structured system quickly turns chaotic.
For providers handling dozens or hundreds of machines across locations, timely maintenance ensures minimal downtime, extended machine life, and customer satisfaction. But juggling schedules, tracking parts, coordinating technicians, and logging machine history manually creates bottlenecks that cost time and money.
Challenges of coffee vending machine maintenance for its providers
Coffee vending machine providers face several practical and operational issues when maintaining their fleets. The growing number of machines, spread across various sites, demands fast service coordination and detailed tracking. Delays in refills or breakdowns can quickly lead to user complaints, lost sales, and negative feedback.
Here are the major challenges faced:
- Lack of real-time machine performance monitoring
- Missed preventive maintenance schedules
- Inability to track parts inventory accurately
- Delays in assigning technicians to service requests
- Poor visibility into machine repair history
- Manual logbooks prone to errors or data loss
- Difficulty managing service SLAs with clients
How maintenance management software can streamline coffee vending machine maintenance challenges?
Maintenance software introduces automation, transparency, and accountability into the service and support model. Instead of relying on spreadsheets or verbal updates, everything from machine uptime to service history is tracked digitally and updated in real-time.
It simplifies technician coordination, provides automated service alerts, keeps tabs on inventory, and ensures every machine gets serviced on time—without letting anything fall through the cracks.
Here’s how it helps:
1. Real-time monitoring and ticketing
Software can connect with vending machine sensors or smart modules to instantly detect faults or performance drops. It reduces manual reporting and speeds up resolution.
- Generates auto-tickets when a fault is detected
- Prioritizes issues based on machine usage and error type
- Routes tickets to the right technician without human intervention
- Supports escalation workflows for unattended tickets
2. Centralized asset tracking
With all machines mapped digitally, service teams can view the full history, specs, and maintenance logs of each unit at any time.
- Track machine installation date, location, warranty status
- Monitor service frequency and failure trends
- Identify machines that repeatedly break down
- Sync updates from field technicians to asset history\
- Tag machines needing urgent attention
3. Scheduled preventive maintenance
Regular upkeep prevents small issues from snowballing into full breakdowns. Software schedules these tasks and alerts teams automatically.
- Create recurring PM tasks for cleaning, descaling, testing
- Set custom intervals by machine type or usage
- Send reminders to technicians before the due date
- Link spare parts to recurring tasks for pre-planning
- Reduce unscheduled service calls over time
- Monitor PM task completion compliance
4. Technician assignment and route planning
Assigning jobs to the right person at the right time becomes easier when you have data on technician location, workload, and availability.
- View which technician is closest to a breakdown site
- Auto-assign based on availability and skillset
- Share GPS-enabled directions for optimized routing
- Notify technicians instantly via mobile app
- Track progress and time taken per job
- Reduce idle time and travel costs
- Enable in-app photo uploads and e-signatures
5. Parts and consumables inventory control
No machine should stop because of a missing part. The system ensures you always know what’s available, what’s running low, and what’s being overused.
- Track real-time inventory of filters, cups, powders
- Get reorder alerts for critical consumables
- Log part usage against each machine or job
- Forecast stock needs based on consumption patterns
6. Performance analytics and reporting
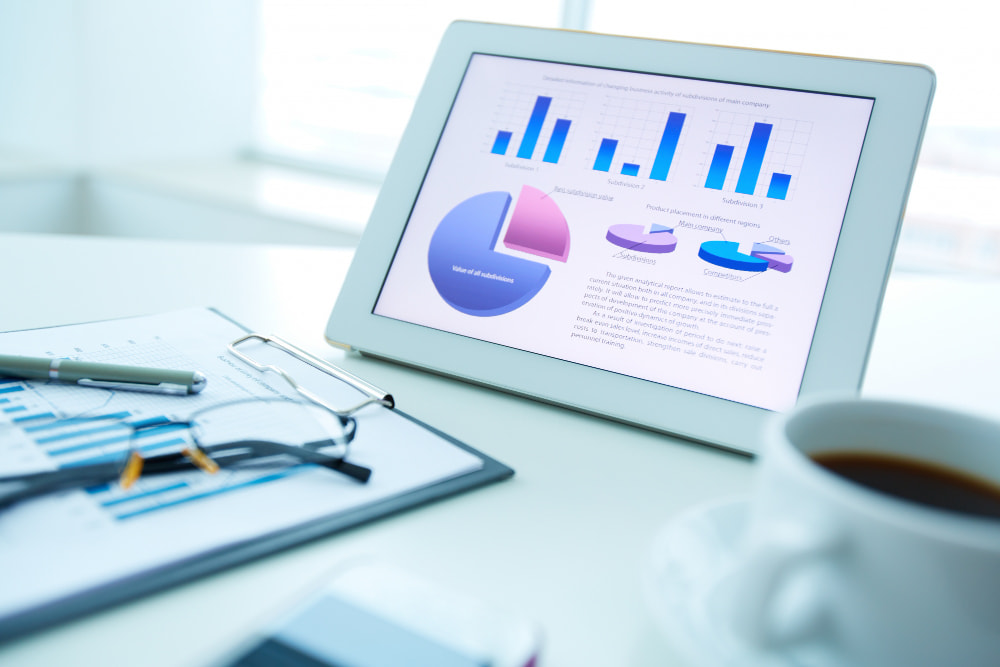
Good maintenance isn’t just about action—it’s about learning from data. Software gives visual insights that help you refine your service model.
- Analyze technician performance by completion time
- Review breakdown frequency by machine model or brand
- Identify top recurring faults and root causes
- Compare SLA compliance across service regions
- Generate automated monthly reports
- Spot cost trends and maintenance ROI
- Filter data by machine, location, or time range
Key features to look for in coffee vending machine maintenance software
Choosing the right software requires evaluating how well it matches your operational model. Not all systems are designed for vending machines, so it’s essential to ensure they support the required functions.
Here are must-have features:
- Asset management module
Track each machine’s lifecycle, warranty, service records, and maintenance status. - Mobile technician app
Field teams can update tasks, upload photos, and mark completion directly from their smartphones. - Preventive maintenance scheduling
Automated service routines ensure no machine is neglected or over-serviced. - Geo-tagging and location mapping
Know exactly where each machine is installed, which helps during routing and service planning. - Inventory tracking for parts and consumables
Stay updated on low stock levels and consumption patterns. - Real-time notifications and alerts
Get notified for breakdowns, service delays, and SLA breaches instantly. - Custom workflows and SLA tracking
Tailor the software to match your internal process and meet service-level agreements. - Reporting and analytics dashboard
Access performance trends, technician KPIs, machine-wise breakdown analysis, and more.
How TeroTAM is helping some of the leading coffee vending machine brands for streamlined maintenance management?
TeroTAM’s CMMS solution is trusted by several vending service providers to simplify and optimize their machine maintenance process. From small providers managing 30–50 machines to larger brands with 500+ units across cities, TeroTAM has scaled with their growth.
With real-time ticketing, automated PM schedules, geo-tagging, and technician apps, it helps vending machine companies:
- Track asset health and service history across locations
- Ensure no breakdown request goes unattended
- Optimize technician dispatches using route maps
- Prevent stock-outs with smart inventory alerts
- Maintain audit-ready digital records for every machine
Companies using TeroTAM have reported faster ticket resolution, reduced machine downtime, and improved customer satisfaction.
Conclusion
Coffee vending machine providers face a range of recurring maintenance tasks—technical servicing, preventive care, stock management, and service coordination. Without a structured system in place, it becomes difficult to maintain service standards, meet client expectations, or scale operations effectively.
Maintenance management software simplifies these processes by centralizing data, automating service schedules, improving technician efficiency, and helping providers reduce machine downtime. For providers aiming to grow and deliver consistent service across all locations, a digital system is no longer optional.Reach out to us at contact@terotam.com to explore how TeroTAM can support your vending machine maintenance needs.