When evaluating whether a CMMS (Computerized Maintenance Management System) is worth the investment, decision-makers need more than just sales pitches and feature lists — they need hard numbers. Calculating the Return on Investment (ROI) of a CMMS helps quantify its actual value in terms of cost savings, performance improvements, and operational efficiency.
But CMMS ROI isn’t always straightforward. It requires a structured look at both direct and indirect savings, and how the system impacts different maintenance functions over time. This blog breaks down the right way to approach it — step by step.
Why Does CMMS ROI Matter?
A CMMS can help reduce downtime, extend asset life, and improve productivity, but unless those improvements can be tied to measurable financial outcomes, it’s difficult to justify the purchase.
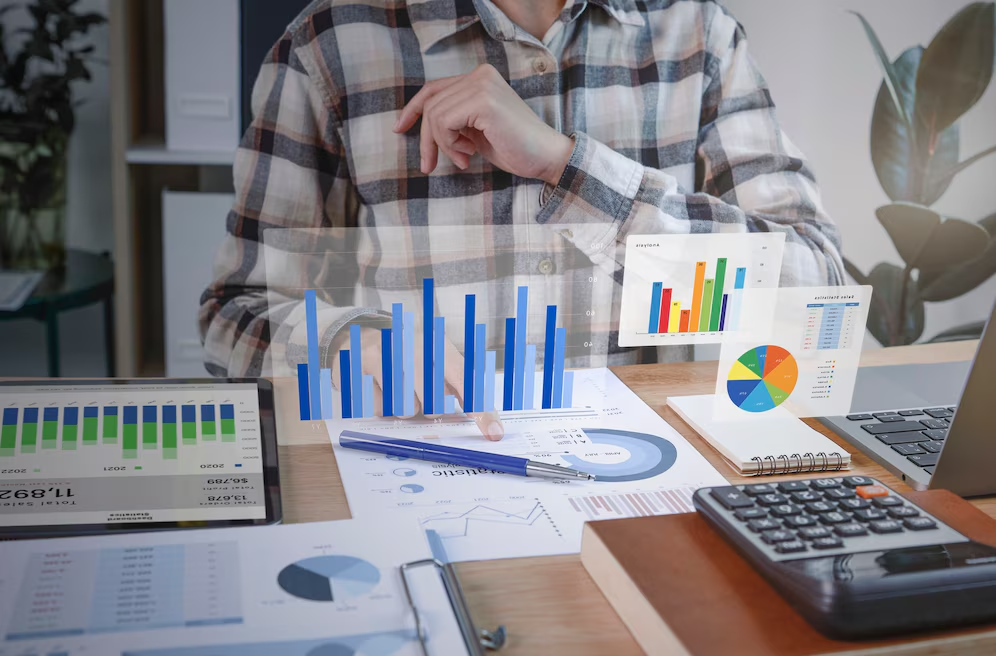
Calculating ROI helps you:
- Assess the financial impact of switching from reactive to preventive maintenance.
- Justify your investment to upper management or board members.
- Benchmark performance improvements over time.
- Guide strategic planning around staffing, parts inventory, and equipment lifecycle.
Step 1: Establish your current maintenance baseline
Before calculating ROI, you need to understand your existing maintenance costs and performance. This baseline becomes the reference point for measuring future improvements.
Key metrics to gather:
- Annual maintenance costs (labour, parts, tools, etc.)
- Unplanned downtime (in hours per asset or per month)
- Preventive vs. reactive maintenance ratio
- Mean Time to Repair (MTTR) and Mean Time Between Failures (MTBF)
- Inventory value and stockout frequency
- Technician overtime hours
- Equipment failure rates
Without this baseline, any ROI estimate will be speculative and disconnected from your operational reality.
Step 2: Identify potential areas of savings
CMMS generates ROI across several areas. Some of the most common include:
1. Reduced unplanned downtime
Unplanned breakdowns are expensive due to halted production, emergency labor costs, and equipment damage. A CMMS helps reduce this by scheduling preventive maintenance and tracking asset health.
2. Lower maintenance labor costs
Better scheduling, reduced firefighting, and fewer repeat visits help maintenance teams do more with fewer resources.
3. Improved spare parts management
CMMS tracks inventory levels and usage trends, helping avoid overstocking or emergency purchases due to stockouts.
4. Extended asset life
Regular inspections and preventive tasks reduce wear and tear, delaying the need for replacements.
5. Regulatory and safety compliance
Automated tracking and documentation help avoid fines and reduce the risk of safety violations or audit failures.
6. Increased wrench time
With less paperwork and better task visibility, technicians can spend more time maintaining and repairing assets instead of searching for parts or instructions.
Step 3: Quantify the expected improvements
This step requires converting improvements into monetary values. Start by assigning estimated percentages of improvement based on either industry benchmarks or internal projections.
Example estimations:
- 20% reduction in downtime
- 15% savings in maintenance labor
- 25% reduction in parts purchases due to better stock management
- 30% reduction in overtime hours
Now, apply these percentages to your baseline numbers.
Step 4: Calculate the total cost of ownership (TCO)
To calculate ROI accurately, you also need to know what the CMMS will cost over its useful life. TCO includes:
- License or subscription fees (monthly or annually)
- Setup and implementation costs
- Training costs
- Internal resource allocation (time and effort)
- Ongoing support and upgrades
Step 5: Determine ROI
Now plug the savings and costs into the ROI formula:
ROI = (Annual Savings – Annual Costs) / Annual Costs × 100
Using the example:
- Annual Savings: $85,000
- Annual Costs: $20,000 (Year 1)
ROI = (85,000 – 20,000) / 20,000 × 100 = 325%
In this case, the CMMS would return more than three times the investment in the first year alone. Over three years, the total return would be even more substantial.
Step 6: Consider qualitative benefits
Not all CMMS benefits are financial. While they may not directly feed into ROI, they still add value and should be acknowledged during justification:
- Centralized data access and digital work order tracking
- Easier audits and compliance checks
- Greater visibility into asset performance
- Improved team accountability and collaboration
- Data-driven decision-making across departments
These benefits contribute to smoother operations, better planning, and more scalable maintenance programs.
Final thoughts
Calculating CMMS ROI gives decision-makers a practical way to understand its financial impact before and after implementation. With the right data, it becomes easier to track where savings are coming from—whether it’s fewer breakdowns, lower labor costs, or better use of spare parts.
It also helps teams plan ahead with more confidence, set maintenance budgets more accurately, and justify future technology upgrades with evidence, not assumptions. When used consistently, ROI tracking can turn your CMMS from just another software tool into a long-term performance driver.