Every Asset in the business has a finite lifespan, commonly referred to as its “Asset life.” The life of an asset encompasses the entire duration it remains operational, from its acquisition to its disposal or retirement. This period is influenced by various factors such as the quality of materials used in its construction, the frequency of maintenance, technological advancements, and environmental conditions.
On the other hand, an asset’s “useful life” refers to the specific timeframe during which it remains economically viable and productive for the organization. It represents the period during which the benefits derived from the asset outweigh its costs, including maintenance, repairs, and operational expenses.
Calculating an asset’s useful life is essential for financial forecasting, depreciation accounting, and investment analysis. With well-calculated useful lives, businesses can optimize resource allocation, minimize downtime, and maximize returns on their investments in assets.
How to Calculate the Useful Life of an Asset?
Determining the useful life of an asset involves employing various depreciation methods, each suited to different types of assets and business needs. Below are three common calculation methods along with their formulas and examples:
1. Straight-Line Depreciation Method:
Formula: Useful Life = (Cost of Asset – Salvage Value) / Annual Depreciation Expense
Example:
Let’s say a machine costs $50,000 with a salvage value (residual value) of $5,000 and is expected to last 10 years.
Useful Life = ($50,000 – $5,000) / 10 years
= $45,000 / 10 years
= 4.5 years
2. Double Declining Balance Method:
Formula: Useful Life = (1 / Depreciation Rate) * 2
Depreciation Rate = 1 / Useful Life
Example: (Using the same machine from the previous example)
Depreciation Rate = 1 / 10 years = 0.1 per year
Double Declining Balance Rate = 0.1 * 2 = 0.2 per year
Useful Life = (1 / 0.2) * 2 = 5 years
3. Units of Production Method:
Formula: Useful Life = Total Units of Production / Expected Units of Production Per Year
Example:
Consider a vehicle that can travel 200,000 miles before it’s no longer useful and is expected to operate for 10 years.
Expected Units of Production Per Year = 200,000 miles / 10 years
= 20,000 miles per year
Useful Life = 200,000 miles / 20,000 miles per year = 10 years
Each method offers distinct advantages and considerations. While straight-line depreciation provides simplicity and uniformity, the double-declining balance method accelerates depreciation in the early years, reflecting higher wear and tear. The units of production method aligns depreciation with actual asset usage, making it suitable for assets with variable utilization patterns.
Factors that Decrease the Useful Life of an Asset
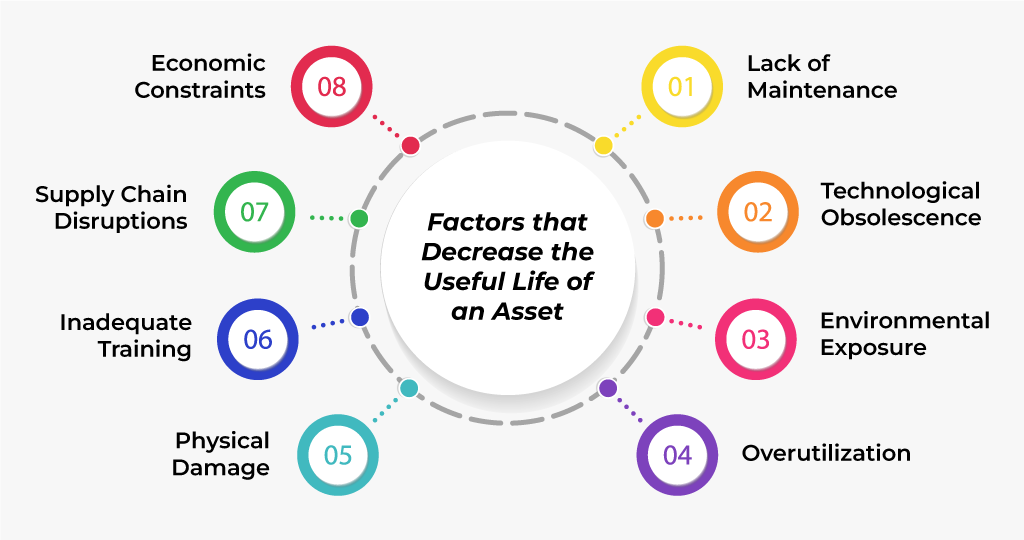
Understanding the calculation part of an asset’s useful life lets you stay aware of your asset and its life span. However, while dealing with it, you also need to understand why the useful life of an asset decreases and which factors play a major role in it.
Let’s check them out quick:
- Lack of Maintenance: Inadequate maintenance accelerates wear and tear, shortening lifespan.
- Technological Obsolescence: Rapid advancements render assets outdated, reducing value.
- Environmental Exposure: Harsh conditions lead to deterioration, diminishing longevity.
- Overutilization: Exceeding capacity increases strain, leading to premature wear.
- Physical Damage: Accidents cause structural damage, impacting operability.
- Inadequate Training: Mishandling due to lack of training results in errors, compromising lifespan.
- Supply Chain Disruptions: Delays in obtaining parts prolong downtime, reducing lifespan.
- Economic Constraints: Budget limitations lead to deferred maintenance, affecting performance.
How to Increase an Asset’s Useful Life?
With keeping all the above-discussed factors in consideration, there are some activities and strategies you must deploy within your organization that help you maximize the useful life of an asset. Such strategies are:
Preventive Maintenance
Implement regular inspection schedules, lubrication routines, and timely repairs to prevent premature wear and extend asset longevity.
Training and Education
Provide comprehensive training programs for staff to ensure proper asset operation and maintenance procedures. This will reduce the risk of misuse or neglect that can shorten the lifespan.
Environmental Controls
To mitigate deterioration, implement measures to protect assets from harsh conditions, such as climate-controlled storage facilities, corrosion-resistant coatings, or appropriate shielding.
Optimized Utilization
Develop strategies to optimize asset usage, avoiding overburdening or underutilizing assets, which can lead to premature wear or reduced efficiency.
Predictive Maintenance
Advanced techniques such as predictive analytics and condition monitoring are used to anticipate maintenance needs, address issues before they escalate, and maximize asset uptime.
Asset Tracking and Documentation
Maintain accurate records of asset history, maintenance activities, and performance metrics to facilitate informed decision-making, identify trends, and implement targeted improvement initiatives.
Implementing Systematic Asset Management Software
Implement an advanced asset management software solution to streamline maintenance schedules, track asset performance, and generate insights for optimizing lifecycle management. Centralizing asset data and automating processes, with such software enhances efficiency, reduces administrative burdens, and ensures proactive management of asset health and longevity.
How Asset Management Software Helps Increase the Useful Life of an Asset?
Asset management software plays a crucial role in maximizing the useful life of assets by providing comprehensive tools and functionalities to streamline maintenance processes, optimize resource allocation, and enhance decision-making.
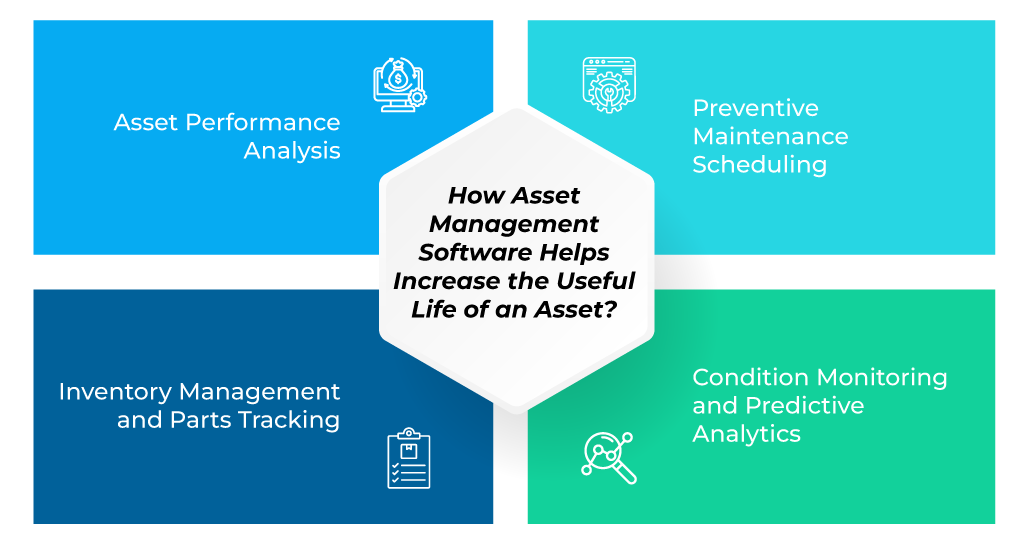
Here’s how asset management software contributes to increasing asset longevity:
Preventive Maintenance Scheduling:
- Utilizes algorithms and historical data to generate optimal maintenance schedules.
- Implements condition-based triggers for maintenance tasks based on sensor data.
- Integrates with IoT devices to monitor asset health in real-time.
- Provides predictive maintenance alerts based on machine learning algorithms.
- Allows customization of maintenance plans for different asset types and usage patterns.
- Offers automated notification systems for scheduling and executing maintenance tasks.
Condition Monitoring and Predictive Analytics:
- Implements sensor fusion techniques to collect and analyze multi-dimensional asset data.
- Utilizes machine learning algorithms to detect patterns and anomalies in asset behavior.
- Employs predictive modeling to forecast asset performance degradation.
- Integrates with predictive maintenance tools to prioritize maintenance activities based on risk assessment.
- Provides advanced visualization tools for interpreting complex asset data.
- Facilitates root cause analysis of asset failures through data correlation and trend analysis.
Inventory Management and Parts Tracking:
- Utilizes RFID or QR-code technology for real-time tracking of spare parts and inventory levels.
- Implements inventory optimization algorithms to minimize stockouts and excess inventory.
- Integrates with procurement systems to automate replenishment processes.
- Provides inventory forecasting based on historical usage and maintenance trends.
- Enables asset-specific parts categorization and bin management for efficient storage.
- Supports multi-location inventory management with centralized visibility and control.
Asset Performance Analysis:
- Utilizes data analytics techniques such as regression analysis and time-series forecasting to analyze asset performance.
- Generates key performance indicators (KPIs) such as mean time between failures (MTBF) and mean time to repair (MTTR).
- Implements trend analysis to identify long-term asset degradation patterns.
- Provides root cause analysis tools for identifying factors contributing to asset failures.
- Integrates with business intelligence platforms for customizable dashboards and reporting.
Conclusion
Maximizing the useful life of assets is a multifaceted endeavor requiring proactive maintenance, strategic upgrades, and leveraging technology. Understanding the factors influencing asset lifespan and implementing robust asset management practices empowers businesses to optimize resource utilization, reduce costs, and drive long-term success.Want to get more insights on this subject or have something in your mind to discuss? – Call our asset management experts now or write us at contact@terotam.com