There are many strategies to raise production, but eliminating downtime is likely to provide you the biggest gain. Consider this: if you want to spend more time on the road, you must improve your ability to prevent flat tires.
However, because downtime can be caused by a variety of factors, there are multiple ways to reduce it.
It’s crucial to look at the types before diving into the causes. There are several, and not all of them are negative.
What Exactly is Downtime?
Downtime occurs when assets and equipment are unavailable or unavailable. So you might say that downtime is when your assets and equipment aren’t running or can’t run.
However, not all downtime is negative, and some of it is used to increase production and asset life cycles. It all relies on why the asset is down and whether you anticipated it.
Downtime is a real threat to any industrial company. One of the most feared scenarios inside an assembly plant is that if one section backs up, it might have a cascading effect on other areas that are waiting for parts to finish operations. It costs you money to wait for parts to finish jobs.
The longer these jobs take to finish, the more money you will lose. The general goal is to boost productivity and decrease the amount of time people or machines are idle. Downtime can be dangerously prolonged due to an operational error, inadequate equipment maintenance, malfunctioning hardware or software, and a variety of other factors.
How Much Does Manufacturing Downtime Really Cost?
When a piece of manufacturing equipment or machinery is not in use, manufacturing downtime occurs. For example, a company might halt production to undertake machine maintenance and repairs in order to increase performance. This kind of downtime is both innocuous and required. Other sorts of downtime, on the other hand, have a negative influence.
Instead of upgrades and scheduled maintenance, unanticipated failures might create downtime in manufacturing operations. Unplanned downtime occurs when a system fails to provide or perform its primary purpose. Unplanned downtime can have a number of detrimental effects on operations, including:
- Business disruption
- Costs of emergency repairs are excessive
- Employee productivity declines
- Reputation and loyalty issues
A variety of events might cause unplanned downtime. An operating fault, insufficient maintenance, or even a software issue could be to blame.
4 Best Ways to Reduce Manufacturing Downtime
To generate finished goods, manufacturers frequently rely on a production line of automated machinery. The use of discounted raw materials in mass production reduces labour costs while increasing profit margins. However, when relying on equipment and machinery, the possibility of unscheduled downtime might be disastrous.
There are several options available to manufacturers to assist prevent unplanned downtime and keep unexpected expenditures to a minimum.
1. Improve Machinery and Equipment
For operators, outdated and ageing equipment might be problematic. It causes job delays and can slow down the entire manufacturing process. Ensure that all outmoded assets are replaced to combat this. Although revenue constraints may limit this, the benefits of improved machine performance and task completion times may outweigh the expenditures.
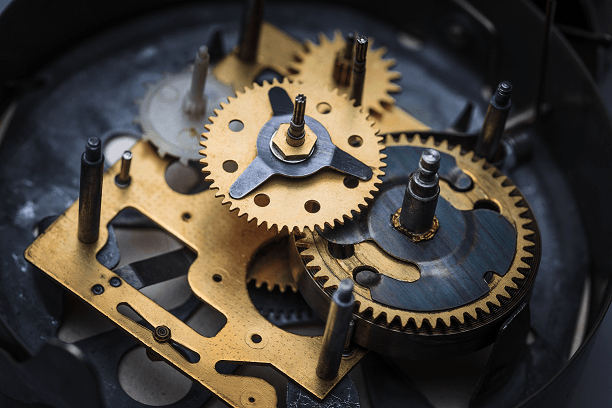
2. Enhance Employee Education & Training
Human mistake is responsible for 70% of manufacturing downtime and equipment loss. Your staff may be responsible for a production loss if they are not properly trained. Simply because they have not been properly trained. Human error can be minimized by sending employees to training sessions and providing adequate resources. Employees can learn how to operate machinery appropriately, use tools effectively, and even repair malfunctioning machines. Finally, delays and downtime will be reduced.
3. Bring a CMMS into the System
Investing in automated technologies like CMMS Software and digitizing your production data may appear costly at first, but it’s a long-term investment that will pay off. A CMMS will arm you with the information you need to cut down on manufacturing downtime. All maintenance data is centralized with digitized maintenance tools, allowing operators and maintenance teams to maximize asset use.
CMMS Software has a number of advantages, including:
- Providing Asset and Work Order Visibility
- Improving Operational Effectiveness
- Inventory, Trash, and Operating Expenditures are all under control
- Keeping Track of Compliance
- Improving Health and Safety in the workplace
4. Implement a Preventive Maintenance Plan
Taking a proactive approach to maintenance, such as developing a preventive maintenance policy, is the most effective technique to reduce manufacturing downtime. Preventive Maintenance (PM), often known as preventative maintenance, is a proactive method that entails frequent and routine equipment maintenance. This reduces the risk of failure, which might result in unplanned downtime.
A Preventative Maintenance plan has the following benefits:
- Fewer breakdowns of production-critical assets
- Equipment reliability has improved
- Fewer emergency and remedial repairs
- Assets with a longer life expectancy have a lower turnover rate
- RCA data collection has been improved
CMMS Software: The Ultimate Productivity Multiplier for Manufacturing Industry
Preventative maintenance, as we all know, takes time away from your day. In the long term, these few scheduled hours each day are significantly more valuable than having to stop working due to equipment outages, which might cause corporate operations to be disrupted for days.
Companies must protect their personnel, maintain safe working environments, keep equipment functioning at peak performance, ensure that everything is documented for inspections, keep inventories properly stocked, and the bottom line is that they must work smarter and be prepared. The correct CMMS software is essential for keeping your maintenance operations running in the event of a crisis.
TeroTAM is a pioneer in the field of CMMS software development. We deliver high-quality technologies to help enterprises streamline operations, increase productivity, stay connected with their teams, and run their businesses more efficiently.
The most valuable assets you have are your family and staff. However, your company is your second most important asset. Implementing a CMMS system enables organizations to take control of their maintenance operations and unleash the system’s ability to allow you to manage your business operations from anywhere, even in the event of a crisis. Connect with us now at contact@terotam.com or schedule an appointment with our experts to get started with the ultimate solution to boost your manufacturing productivity.