Lockout/Tagout (LOTO) safety protocols are critical in preventing hazardous energy releases during maintenance. Equipment failures, unexpected startups, or residual energy discharge can cause severe injuries or fatalities if LOTO procedures are not followed correctly. Manual tracking of these protocols often leads to errors, delays, and compliance failures, putting both workers and businesses at risk.
CMMS for LOTO safety integrates digital workflows, automated verification steps, and real-time monitoring to eliminate these challenges. Maintenance teams can ensure every lockout point is secured before work begins while keeping a detailed audit trail for regulatory compliance. This article explores the key challenges in LOTO implementation, how CMMS enhances safety protocols, and strategies to maximize its effectiveness.
Why LOTO Safety is Critical in Industrial Workplaces?
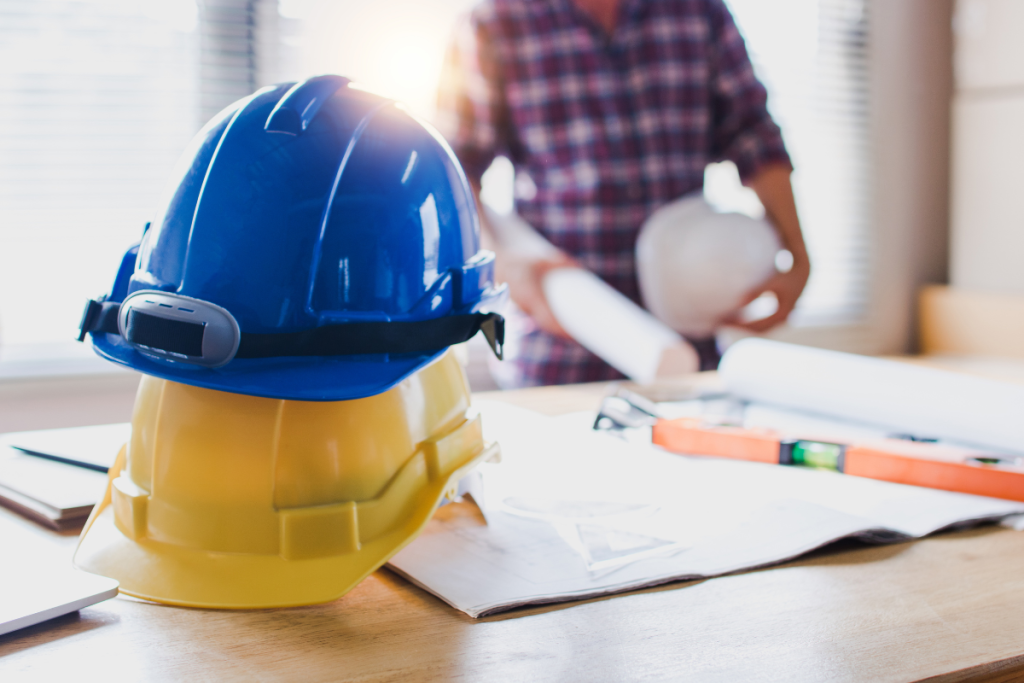
LOTO procedures are not just regulatory requirements—they are life-saving measures. Many workplace accidents occur because employees bypass lockout procedures due to time constraints or lack of awareness. In industries like manufacturing, energy, and construction, ensuring strict adherence to LOTO protocols can mean the difference between a safe workday and a catastrophic event.
Some key risks associated with improper LOTO implementation include:
- Unexpected machine startups leading to severe injuries
- Exposure to hazardous energy sources like high voltage or pressurized systems
- Lack of accountability in maintenance processes, increasing accident risks
A structured and well-documented LOTO system, backed by technology, is essential to address these concerns effectively.
Common Challenges in Implementing LOTO Procedures
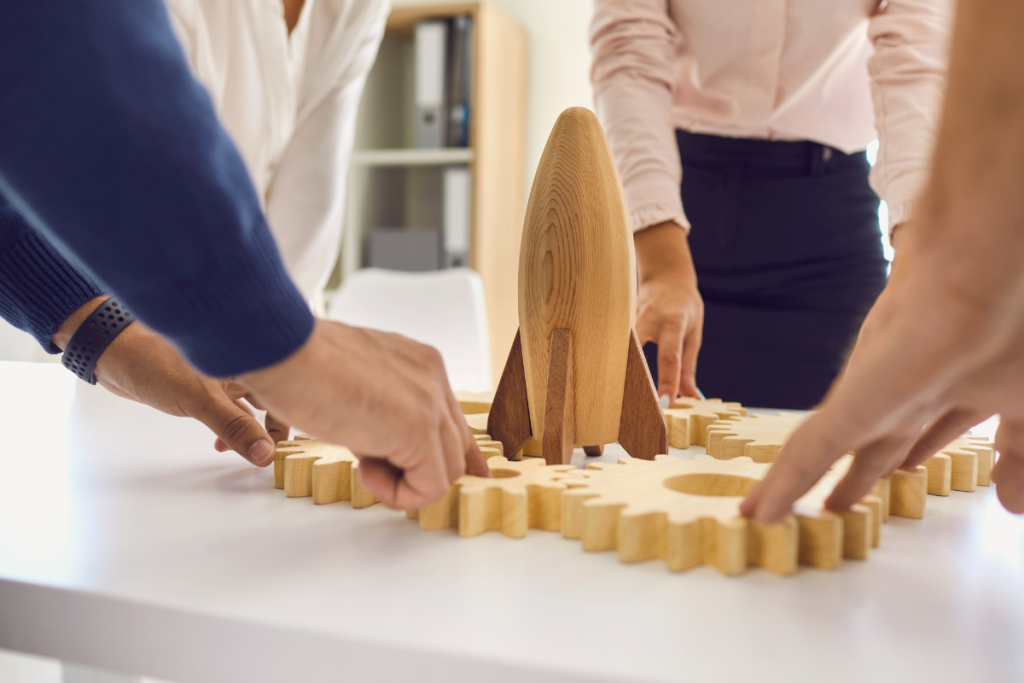
Many industries have well-defined LOTO policies, but enforcing them consistently presents several difficulties. Managing multiple lockout points manually increases the likelihood of missed steps, while poor documentation can leave safety gaps. Teams often face inefficiencies in tracking who applied or removed lockout devices, leading to confusion and non-compliance. Without a centralized system, ensuring that every LOTO protocol is followed accurately becomes a daunting task.
1. Inconsistent Documentation
LOTO procedures require detailed, up-to-date instructions for every piece of equipment. Relying on paper-based records or outdated manuals often leads to miscommunication. Workers may not have access to the latest lockout steps, increasing the risk of skipped or incorrect procedures. Digital inconsistencies across departments further complicate compliance efforts, making audits and regulatory reporting challenging.
2. Human Error and Non-Compliance
Without a structured verification process, workers may unintentionally bypass critical LOTO steps. Fatigue, lack of training, or rushing through maintenance tasks can lead to incomplete lockouts. Organizations that lack real-time monitoring struggle to detect these lapses, increasing the likelihood of hazardous energy exposure. Failure to track who applies and removes lockout devices also raises accountability concerns.
3. Tracking and Visibility Issues
Locking out multiple energy sources requires constant monitoring, which becomes overwhelming when managed manually. Maintenance supervisors may find it difficult to confirm whether all required lockouts are in place before work begins. When LOTO records are stored in spreadsheets or physical logs, real-time visibility is lost, making it harder to detect potential safety violations.
4. Regulatory Compliance Pressure
Meeting OSHA and industry-specific LOTO standards requires accurate documentation and strict procedural adherence. Organizations failing to provide a clear audit trail face penalties, legal risks, and reputational damage. Preparing compliance reports without a structured system consumes valuable time and resources, diverting focus from core maintenance tasks.
How CMMS for LOTO Safety Enhances Compliance and Efficiency?
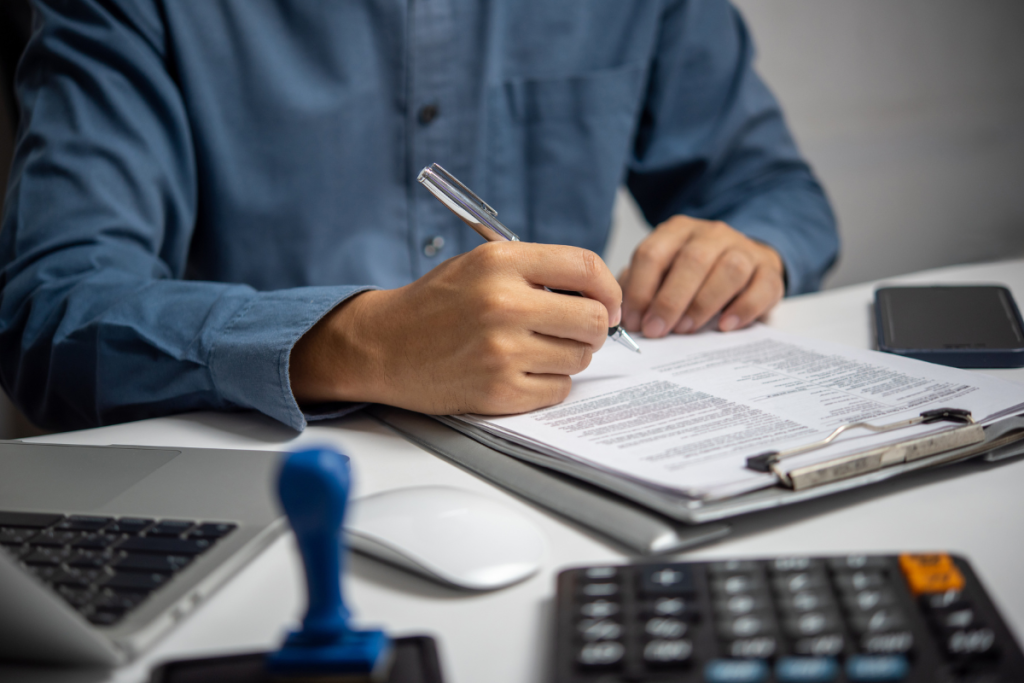
A CMMS for LOTO safety standardizes lockout procedures, ensuring that every maintenance task follows a structured workflow. Digital instructions eliminate ambiguity, reducing the risk of skipped steps. Work orders within the CMMS incorporate mandatory LOTO actions, preventing tasks from proceeding until proper lockout measures are confirmed. Real-time tracking allows supervisors to monitor LOTO status across multiple job sites, ensuring compliance without manual intervention.
1. Standardized Procedures and Digital Documentation
A centralized platform stores detailed LOTO instructions for each asset, ensuring workers always access the correct procedure. Digital documentation allows updates to be instantly applied, preventing outdated lockout steps from being used. Standardization across all locations and teams reduces variability in execution, eliminating confusion and improving overall compliance.
- Centralized LOTO procedure database
- Instant updates for new safety protocols
- Standardization across teams and job sites
2. Real-Time Access to Lockout Instructions
Maintenance personnel can retrieve LOTO procedures directly from their mobile devices, ensuring quick and accurate lockout implementation. Eliminating reliance on printed documents reduces errors caused by missing or outdated information. Real-time accessibility ensures that technicians follow the correct steps regardless of location or shift changes.
- Mobile access to LOTO steps
- Eliminates outdated paper-based instructions
- Ensures accurate procedures across shifts and teams
- Provides real-time updates for emergency modifications
3. Automated Workflows for Safer Operations
LOTO checklists and automated approvals ensure that no step is overlooked before maintenance begins. CMMS verifies that lockout devices are applied before generating work permits, reducing the risk of unauthorized servicing. These workflows also track who performed each step, maintaining accountability in high-risk environments.
- Enforces LOTO steps in work orders
- Blocks maintenance tasks until lockouts are verified
- Tracks personnel responsible for lockout actions
- Reduces unauthorized access to hazardous equipment
- Ensures compliance with site-specific safety protocols
4. Digital Checklists to Minimize Human Error
Digital checklists guide workers through LOTO procedures, requiring step-by-step confirmations. These checklists ensure that all lockout devices are applied and verified before maintenance begins. Automatic alerts notify supervisors if any step is skipped or incorrectly executed.
- Step-by-step lockout verification
- Prevents unauthorized maintenance start-ups
- Supervisor alerts for skipped steps
5. Real-Time Monitoring and Audit Trails
Live dashboards track active LOTO procedures, giving supervisors full visibility into ongoing maintenance activities. Every lockout action is recorded, creating a traceable digital audit trail for regulatory inspections. Historical data helps organizations identify areas for process improvement and training needs.
- Live dashboard for active LOTO monitoring
- Digital audit trail for compliance inspections
- Identifies training gaps through historical data
- Enables data-driven safety improvements
6. Training and Certification Management
Ensuring only trained personnel perform LOTO procedures is essential for safety and compliance. CMMS helps organizations track certification statuses, schedule refresher courses, and issue automatic reminders. This reduces the likelihood of unqualified workers handling hazardous energy sources.
- Tracks worker certifications and training history
- Schedules mandatory refresher courses
- Reduces risk of unauthorized personnel performing LOTO
- Provides detailed training logs for compliance reports
- Sends automated alerts for upcoming training requirements
Maximizing the Benefits of CMMS for LOTO Safety
Implementing CMMS for LOTO safety is not just about digitization—it requires continuous monitoring, regular updates, and workforce engagement. A structured approach ensures that the system remains effective and adaptable to evolving safety requirements. Organizations that actively review and refine their LOTO procedures see improved compliance and reduced risks.
1. Regularly Updating LOTO Procedures
Equipment modifications, new machinery, and regulatory changes require updates to LOTO steps. CMMS allows organizations to modify lockout procedures instantly, ensuring workers always follow the most current instructions.
2. Conducting Routine LOTO Audits
Periodic audits identify weaknesses in existing lockout processes and highlight areas for improvement. CMMS-generated reports streamline this process by providing data-driven insights into compliance trends.
3. Encouraging Worker Engagement
A user-friendly CMMS interface and proper training help workers actively participate in safety compliance. Technicians should be encouraged to report issues, suggest improvements, and take ownership of LOTO adherence.
4. Integrating IoT for Advanced Monitoring
IoT sensors enhance LOTO compliance by detecting unauthorized machine restarts. Integrating CMMS with IoT technology adds an extra layer of protection against human errors and safety breaches.
Conclusion
CMMS for LOTO safety strengthens workplace protection by digitizing procedures, automating compliance checks, and improving visibility into lockout processes. Organizations that leverage CMMS eliminate manual inefficiencies, reduce risks, and ensure consistent adherence to safety regulations. A proactive approach to LOTO safety not only prevents accidents but also builds a culture of accountability and operational excellence.Looking for a CMMS solution that enhances LOTO safety in your workplace? Contact us at support@terotam.com to learn how our system can streamline your lockout procedures and improve compliance.