Efficient management of physical spaces, assets, and infrastructure is a critical responsibility for any organisation—especially those with large facilities or multiple properties. That’s where CAFM comes into play. Short for Computer-Aided Facility Management, CAFM refers to a software solution designed to support facility managers in tracking, managing, and optimising the physical and operational aspects of buildings.
Though the concept has been around for decades, modern CAFM tools have evolved into robust platforms offering real-time data, integration capabilities, and automation—all helping organisations increase efficiency, reduce costs, and maintain compliance.
Definition and core functionality of CAFM
CAFM is a software platform that combines database technology with graphical representation (usually in the form of CAD drawings) to help facility professionals plan, execute, and monitor facility-related activities. The system typically manages data related to space, assets, maintenance, infrastructure, and workforce utilisation.
Basically, CAFM helps you answer questions such as:
- How is our building space being used?
- What assets are in each facility and what’s their maintenance status?
- Which service requests are pending, in progress, or completed?
- Are we meeting compliance and safety standards?
Key modules in a CAFM system
Modern CAFM platforms are modular in nature, meaning they come with multiple functional areas that can be deployed based on organisational needs.
1. Space management
Helps track how every square metre of facility space is being used. It includes floor plan visualisation, space allocation, occupancy tracking, and departmental usage reports.
2. Asset tracking
Provides a centralised inventory of all assets within the facility—HVAC systems, electrical panels, furniture, IT equipment—along with metadata like location, warranty, maintenance history, and service lifecycle.
3. Maintenance management
Enables both preventive and reactive maintenance workflows. You can schedule inspections, receive work requests, assign technicians, and track job status from start to finish. Many CAFM systems integrate with mobile apps for real-time updates.
4. Work order management
Helps generate, assign, and monitor work orders across multiple departments. It provides insights into technician performance, task completion rates, turnaround times, and overall maintenance efficiency.
5. Room and resource booking
Allows employees or administrators to reserve rooms, desks, parking, or equipment through an internal portal. This is especially valuable in hybrid work environments.
6. Lease and property management
For organisations that manage leased properties or large campuses, this module tracks lease terms, renewal dates, cost allocation, and occupancy metrics.
7. Compliance and safety
Automates compliance reporting by recording inspections, risk assessments, certifications, and legal documentation. Ensures your facility adheres to relevant regulations and audit requirements.
Benefits of implementing a CAFM system
Implementing a CAFM solution delivers deep insights into facility dynamics through integrated data streams, graphical models and real-time analytics. Facility engineers and planners gain the ability to monitor asset performance, track space utilisation and enforce SLAs on preventive maintenance. Data aggregation from CAD schematics, IoT sensors and work-order histories fuels advanced analytics and supports high-availability operations. This systematic approach transforms raw facility data into actionable metrics for improved decision-making and operational resilience.
1. Real-time asset performance monitoring
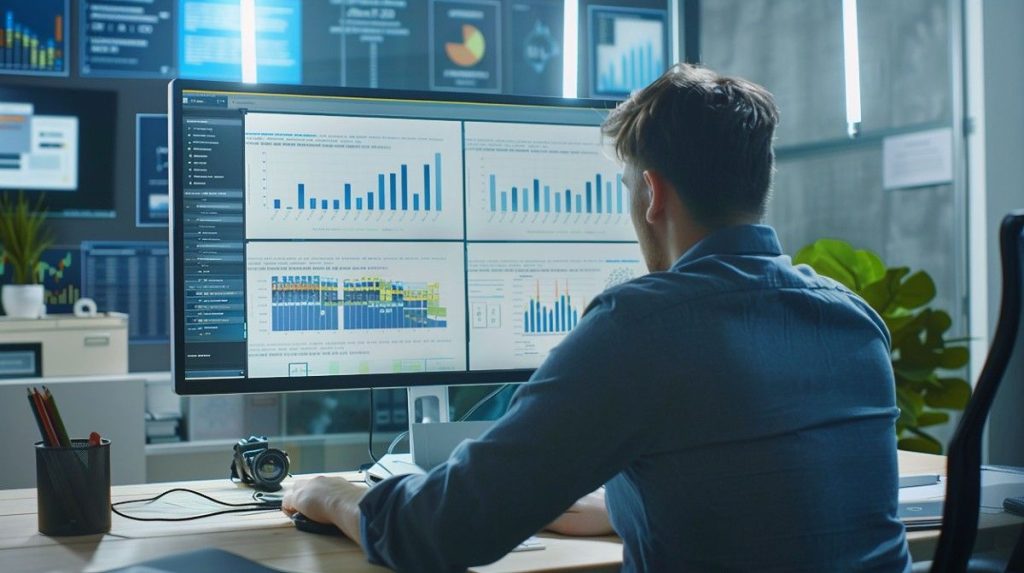
Integration with IoT devices and building management systems delivers continuous telemetry on equipment parameters such as vibration, temperature and energy consumption. Threshold alerts trigger work orders when metrics exceed predefined limits, preventing critical failures. Trend analysis on historical data supports predictive maintenance models, reducing mean time to repair and extending mean time between failures.
2. Advanced space utilisation analytics
Heat mapping overlays occupancy records on CAD floor plans to reveal utilisation patterns at the room and zone level. API connections to access control and desk-booking platforms populate live occupancy metrics, enabling dynamic desk hoteling and meeting-room scheduling. Predictive algorithms forecast demand shifts and recommend reconfiguration scenarios to reduce underutilised areas and drive cost savings.
3. Automated preventive maintenance scheduling
Rule-based engines use runtime data and failure-probability curves to generate maintenance schedules for HVAC units, chillers and fire suppression systems. Work orders include detailed parts lists, calibration procedures and safety checklists. Mobile-enabled technician interfaces capture time stamps, digital sign-offs and “before/after” imagery, closing the loop on maintenance records and feeding reliability databases.
4. Integrated SLA and contract management
Service level agreements for in-house teams and external vendors are codified in the CAFM database, with performance dashboards tracking compliance metrics such as first-response time and downtime. Automated escalation workflows route critical tickets to supervisors when contractual thresholds are breached. Comprehensive audit trails simplify vendor performance reviews and renewal negotiations.
5. Energy performance benchmarking
Consolidation of energy-meter data with equipment runtime logs calculates kWh per square metre, enabling comparison against design specifications and industry benchmarks. Anomaly detection flags off-hours operation or equipment running beyond optimal duty cycles. These insights support sustainability targets and inform retrofit projects that reduce energy waste.
6. Digital twin and scenario simulation
Three-dimensional facility models linked to live asset data create a digital twin environment for what-if analyses. Simulations test the impact of layout changes, capacity expansions or equipment downtime without physical disruptions. Scenario outcomes quantify operational risks and financial impacts, guiding capital planning and risk-mitigation strategies.
7. Scalable API-driven interoperability
RESTful APIs provide seamless data exchange with ERP, CMMS and HR systems, ensuring consistent records across finance, procurement and workforce modules. Event-driven webhooks enable real-time updates, while modular architecture supports phased deployments and custom workflow extensions. Vendor-agnostic integration avoids lock-in and future-proofs your FM ecosystem.
How can an integrated CMMS be a bigger picture than CAFM?
While CAFM (Computer-Aided Facility Management) systems are designed to manage and optimise space, assets, and overall facility operations, they are primarily focused on strategic planning and high-level management. However, when you integrate a Computerised Maintenance Management System (CMMS), you’re unlocking a whole new dimension of operational control that goes well beyond what CAFM typically covers.
1. Comprehensive asset management and maintenance
Both CAFM and CMMS track assets, but CMMS takes it a step further by managing the entire maintenance lifecycle—from preventive and corrective maintenance schedules to asset health monitoring and repair history. While CAFM can tell you where your equipment is and who’s using it, CMMS provides actionable insights on its performance, condition, and maintenance needs, ensuring assets run efficiently throughout their lifespan.
2. Preventive and predictive maintenance capabilities
One of the key benefits of an integrated CMMS is its ability to automate preventive maintenance schedules based on real-time usage or condition data. This ensures that issues are addressed before they turn into costly repairs or downtime. CAFM systems typically lack this automated maintenance functionality, focusing more on space allocation and visual representation rather than proactive asset management.
3. Detailed work order management
CMMS allows facility managers to generate, assign, and track work orders with granular details, including labour hours, parts used, service history, and real-time updates. This level of detail isn’t something CAFM is built to handle. While CAFM may assist with general work requests, CMMS ensures tasks are carried out efficiently, with performance metrics and reporting features to drive continuous improvement.
4. Real-time data and reporting
Integrated CMMS solutions offer real-time monitoring and reporting, enabling facility managers to make data-driven decisions about maintenance strategies, resource allocation, and cost management. CAFM’s strength lies in long-term space planning and resource allocation, but it doesn’t provide the same level of operational insight or dynamic, real-time reporting that CMMS delivers.
5. Improved cost control and budgeting
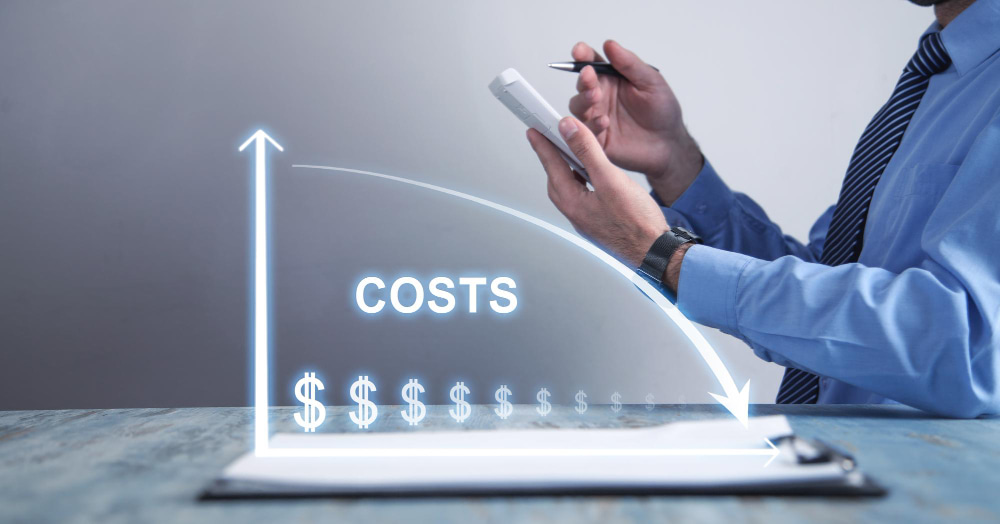
CMMS gives you a detailed breakdown of maintenance costs, including parts, labour, and downtime, allowing for more accurate budget forecasting and cost control. It helps identify trends and areas where operational costs can be reduced. CAFM, on the other hand, focuses on space and asset utilisation and might not provide the same level of financial visibility regarding operational and maintenance expenditures.
6. Compliance and audit readiness
While CAFM systems can store compliance documentation and track inspections, an integrated CMMS goes further by maintaining real-time records of every maintenance activity, ensuring a continuous audit trail. This makes it easier to demonstrate compliance during inspections, maintain certifications, and manage regulatory requirements more effectively than a CAFM system alone.
7. Seamless integration with other enterprise systems
An integrated CMMS often has the capability to connect seamlessly with other business systems like Enterprise Resource Planning (ERP), Building Management Systems (BMS), and IoT devices. This creates a fully connected environment where all data flows into a central platform, offering a holistic view of facility operations. CAFM typically focuses on facility-specific data and may not offer the same level of integration with broader business systems.
In conclusion,
While CAFM is excellent for overseeing facilities, managing spaces, and tracking asset allocation, an integrated CMMS expands upon these capabilities by focusing on the operational aspects of maintenance. It adds real-time maintenance tracking, preventive scheduling, detailed work orders, cost management, and compliance—all of which go far beyond the scope of CAFM.
By combining both systems, you not only optimise your space and asset management but also ensure that every part of your facility is running at peak performance, contributing to overall efficiency, cost savings, and operational excellence.Want to know more? – Let’s get connected. Drop us a line at contact@terotam.com