Facility management requires a structured approach to ensure the smooth operation of buildings, equipment, and services. From regular maintenance and safety inspections to compliance tracking and asset management, every aspect must be documented and executed efficiently. Traditional paper-based Digital Checklists or manual data entry methods often lead to inconsistencies, delays, and compliance risks, impacting overall efficiency.
Digital checklists provide a more reliable and structured solution by automating data entry, streamlining task execution, and enabling real-time monitoring. In this article, we’ll explore the key challenges of manual checklists, the technical advantages of digital checklists in facility management, and the industries that benefit from their implementation.
Challenges of Manual Checklist in Facility Management
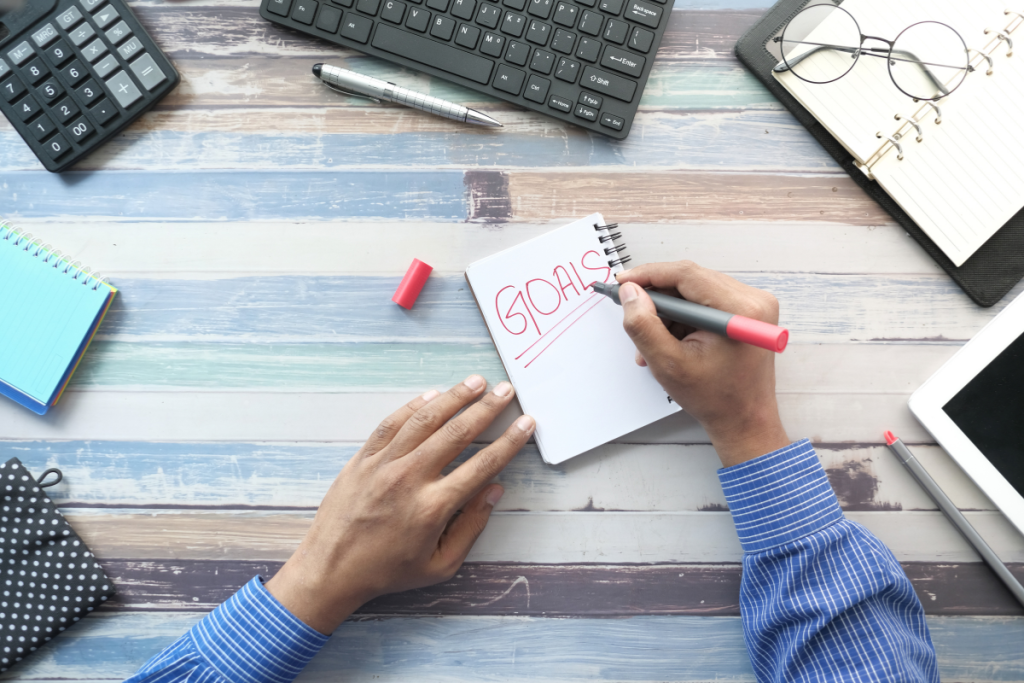
Managing facility operations with traditional checklists introduces inefficiencies that can compromise safety, compliance, and productivity. Manual tracking methods lack real-time visibility, are prone to errors, and create unnecessary administrative burdens. Below are some key challenges associated with manual checklists and their impact on facility management.
1. Data Inconsistencies & Human Errors
Handwritten checklists are prone to errors such as incomplete entries, incorrect timestamps, and illegible handwriting. These inconsistencies create gaps in maintenance logs, leading to inaccurate reporting and difficulty in tracking historical data. In regulated industries, this can result in non-compliance and operational risks.
2. Limited Real-Time Monitoring & Delayed Reporting
Paper checklists require manual submission, delaying the flow of critical information. Facility managers often rely on end-of-day or weekly reports, which makes it difficult to address issues in real time. Without instant visibility into ongoing maintenance activities, urgent issues can go unnoticed, leading to prolonged downtime or safety hazards.
3. Inefficient Workflows & Increased Administrative Burden
Facility staff spend significant time filling out checklists, organizing paperwork, and transferring data into spreadsheets or management systems. This manual process reduces operational efficiency and increases administrative overhead. Delays in processing information also slow down response times for maintenance and compliance-related tasks.
4. Storage, Retrieval & Data Loss Risks
Physical checklists require dedicated storage space, making document retrieval time-consuming. Misplaced or damaged records create challenges during audits, making it difficult to prove compliance with regulatory standards. Digital storage eliminates these risks and ensures that historical data remains easily accessible.
5. Compliance Challenges & Audit Risks
Many industries require strict adherence to maintenance schedules and safety protocols. Manual checklists can lead to missed inspections, incomplete logs, and lack of proof during compliance audits. Without a centralized system to track and store facility data, meeting industry standards becomes increasingly difficult.
How Does Digital Checklist Improve Facility Management?
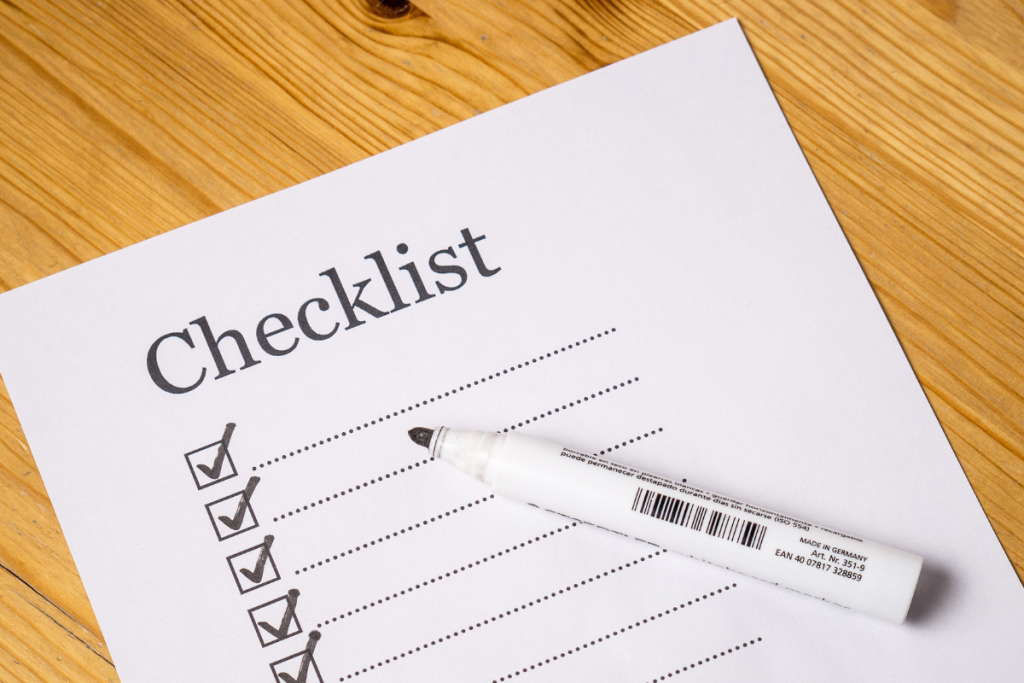
Facility management involves complex, interconnected workflows that demand accuracy and efficiency. Digital checklists optimize operations by automating task tracking, improving data accuracy, and enhancing overall compliance. They also integrate with facility management software (CAFM, CMMS, or IWMS) to provide real-time monitoring and analytics.
1. Automated Data Capture & Standardized Documentation
Digital checklists eliminate manual errors by ensuring that all required fields are completed before submission. Automated data capture features, such as barcode scanning, image uploads, and geotagging, provide a structured and standardized approach to documentation.
- Ensures accurate task completion
- Prevents missing or incorrect entries
- Enables consistent data formatting across multiple locations
2. Real-Time Tracking & Instant Notifications
With cloud-based checklists, facility managers can monitor maintenance activities in real time. Technicians can update checklists from mobile devices, allowing managers to receive immediate alerts for missed tasks or compliance breaches.
- Provides live updates on maintenance tasks
- Triggers alerts for overdue or missed inspections
- Enhances response times for critical maintenance requests
3. Automated Scheduling & Task Assignment
Digital checklists can integrate with work order systems to automatically schedule recurring inspections, maintenance checks, and safety audits. Tasks can be assigned based on technician availability, skill level, or location, ensuring optimized resource allocation.
- Eliminates manual scheduling errors
- Reduces downtime with proactive maintenance
- Ensures optimal workforce utilization
- Prevents missed maintenance tasks
4. Advanced Compliance Tracking & Audit Readiness
Digital checklists store timestamps, user logs, and task completion records, making it easier to demonstrate compliance with industry regulations. Historical data can be retrieved instantly during audits, reducing the risk of penalties.
- Maintains a digital audit trail for compliance
- Automatically generates reports for regulatory bodies
- Reduces the risk of non-compliance and penalties
- Improves accountability with user-specific task logs
- Integrates with regulatory frameworks for automated compliance checks
5. Mobile Accessibility & Remote Task Management
Mobile-enabled digital checklists allow technicians and facility managers to update tasks, log issues, and complete inspections from any location. This is particularly beneficial for large facilities or multi-site operations.
- Empowers mobile workforce with on-the-go access
- Reduces dependence on physical paperwork
- Enhances team collaboration across multiple locations
- Minimizes response time for urgent maintenance requests
6. Data Analytics for Predictive Maintenance & Continuous Improvement
Facility management teams can analyze historical checklist data to identify trends, recurring issues, and areas for process improvement. Predictive maintenance models can be implemented based on real-time equipment performance data.
- Identifies patterns in maintenance failures
- Improves decision-making with data-driven insights
- Enables proactive maintenance strategies
- Reduces costs by preventing major equipment failures
- Optimizes asset lifecycle management
Industries That Benefit from Digital Checklist in Facility Management

Digital checklists play a critical role across various industries, ensuring smooth facility operations, regulatory compliance, and enhanced safety. From healthcare and manufacturing to commercial real estate and education, businesses that rely on well-maintained infrastructure and equipment can significantly benefit from automating their maintenance and inspection processes. The ability to track tasks in real time, schedule preventive maintenance, and generate compliance reports makes digital checklists an indispensable tool. Here’s how different industries leverage digital checklists to improve efficiency and operational standards.
Healthcare Facilities
Hospitals, clinics, and aged care centers require strict adherence to hygiene, equipment maintenance, and patient safety protocols. A digital checklist helps ensure that routine sanitation, medical equipment inspections, and emergency preparedness drills are completed on time.
For example, in a hospital setting, staff can use digital checklists to confirm that operating rooms are sanitized after each procedure, oxygen levels in critical care units are checked, and pharmaceutical storage temperatures remain within the required range. Automated alerts ensure that no critical task is missed, reducing the risk of infections, equipment malfunctions, and regulatory non-compliance.
Manufacturing Plants & Industrial Facilities
Industrial environments depend on timely equipment maintenance, safety inspections, and compliance tracking to prevent machinery breakdowns and workplace hazards. Digital checklists help streamline daily operational checks, track preventive maintenance schedules, and ensure adherence to safety standards such as OSHA regulations.
For instance, a manufacturing plant can use IoT-integrated checklists to monitor real-time equipment performance; consequently, this system can trigger alerts when machines show signs of overheating or wear. Ultimately, this proactive approach not only reduces downtime but also prevents costly repairs and, in addition, enhances worker safety by ensuring that all safety gear and emergency exits are regularly inspected.
Commercial Real Estate & Corporate Buildings
Facility management in office buildings, retail centers, and high-rise commercial properties involves, notably, maintaining HVAC systems, electrical equipment, security systems, and fire safety compliance. Furthermore, a digital checklist provides a structured way to schedule routine inspections and track maintenance tasks.
For example, a commercial property manager can use a centralized digital checklist to verify that HVAC filters are replaced every three months, that security cameras are functioning correctly, and that fire extinguishers are inspected as per local compliance laws. Additionally, with mobile access, on-site facility teams can report issues in real time, which allows for immediate resolution and, ultimately, prevents potential operational disruptions.
Hospitality & Retail
Hotels, restaurants, and retail chains need to maintain high cleanliness standards, food safety regulations, and seamless facility maintenance to ensure customer satisfaction. Digital checklists enable housekeeping teams, kitchen staff, and maintenance crews to follow standardized procedures and log their tasks efficiently.
For instance, a hotel can use a digital checklist for housekeeping staff to confirm room sanitization, minibar restocking, and air conditioning checks before guest check-ins. Similarly, a retail store can track daily inventory inspections, refrigeration temperature monitoring, and compliance with fire safety regulations to maintain smooth business operations.
Educational Institutions & Public Infrastructure
Schools, universities, and government buildings require facility upkeep, security monitoring, and infrastructure inspections to provide a safe environment for students and staff. A digital checklist helps streamline maintenance workflows, ensuring that classrooms, restrooms, and common areas are cleaned regularly, HVAC systems function efficiently, and emergency exits are accessible at all times.
For example, a university campus can implement digital checklists to verify that, in addition, lecture halls are disinfected daily, playground equipment is routinely inspected for safety hazards, and, furthermore, fire alarms undergo regular testing. Additionally, with automated record-keeping, administrators can easily provide audit reports to regulatory bodies, thereby demonstrating compliance with health and safety standards.
Conclusion
Digital checklists are transforming facility management by enhancing efficiency, ensuring compliance, and reducing operational risks. With real-time data capture, automated workflows, and mobile accessibility, facility managers can maintain buildings more effectively while improving response times and accountability. The shift from manual processes to a digital solution not only saves time but also optimizes overall facility operations.Looking to implement digital checklist for your facility management services? Drop us a line at contact@terotam.com or schedule a demo now with Team Terotam to explore a tailored solution for your business.