Failure Modes, Effects, and Criticality Analysis (FMECA) is an extension of Failure Modes and Effects Analysis (FMEA). It is a systematic method for evaluating and analyzing the potential failure modes of a system, their causes and effects, and the criticality of these effects. The primary aim of FMECA is to identify and prioritize potential failures to enhance system reliability and safety.
FMEA vs FMECA: What’s the difference?
FMEA focuses on analyzing the causes and effects of these failure modes to understand their impact on the overall operation. The analysis helps in systematically uncovering weaknesses and vulnerabilities without assigning a criticality value to each identified failure mode. This makes
FMEA is suitable for simpler systems and processes where a detailed criticality assessment may not be necessary, such as in regular consumer products or basic manufacturing.
FMECA expands upon FMEA by integrating a criticality assessment into the analysis process. In addition to identifying failure modes, causes, and effects, FMECA evaluates the criticality of each identified failure mode based on factors like likelihood of occurrence, severity of consequences, and detectability. This criticality assessment enables a more precise prioritization of risks, ensuring that resources are allocated effectively to mitigate the most critical failures first.
FMECA is particularly valuable in complex systems and high-risk environments, such as aerospace, healthcare, and military applications, where understanding and managing the severity of potential failures is paramount to operational safety and reliability.
How FMECA Works?
The FMECA process is a structured approach that involves several key steps to systematically identify, analyze, and prioritize potential failure modes in a system.
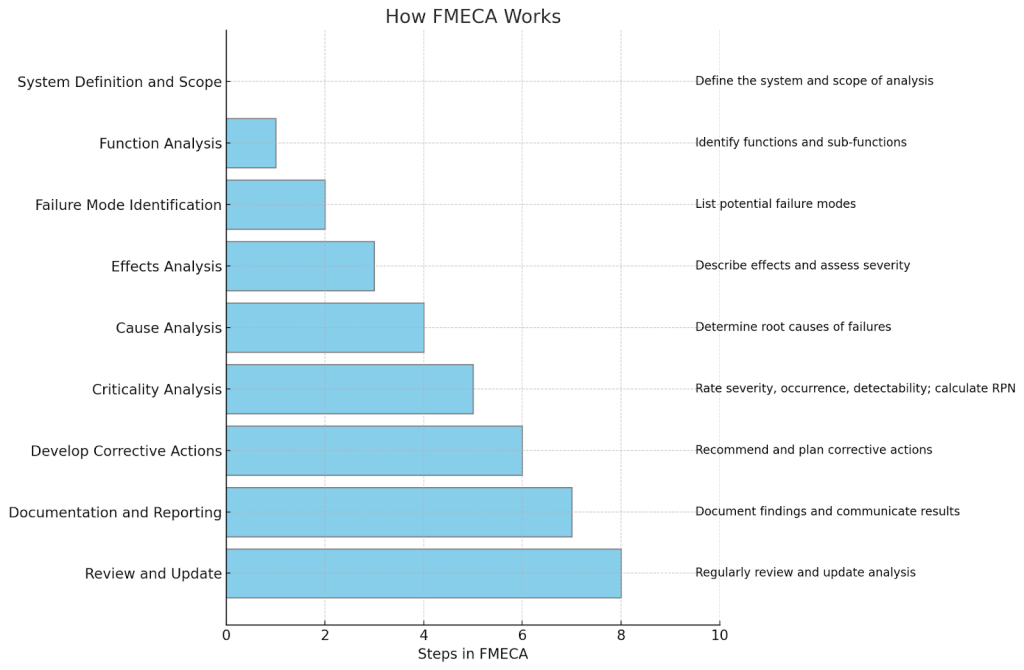
The key steps in the FMECA process:
- System Definition and Scope: Define the system and scope of analysis.
- Function Analysis: Identify functions and sub-functions.
- Failure Mode Identification: List potential failure modes.
- Effects Analysis: Describe effects and assess severity.
- Cause Analysis: Determine root causes of failures.
- Criticality Analysis: Rate severity, occurrence, detectability; calculate RPN.
- Develop Corrective Actions: Recommend and plan corrective actions.
- Documentation and Reporting: Document findings and communicate results.
- Review and Update: Regularly review and update analysis.
Who Can Use FMECA?
FMECA can be used by a diverse range of professionals and stakeholders, including:
- Engineers and Designers: To identify and mitigate potential failure modes during the design phase.
- Quality Assurance Teams: To enhance product reliability and safety.
- Maintenance Managers: To develop effective maintenance strategies and prioritize maintenance activities.
- Risk Management Professionals: To assess and mitigate risks associated with system failures.
- Regulatory Bodies: To ensure compliance with safety and reliability standards.
How Can It Be Used in Maintenance Management?
FMECA revolutionizes maintenance management by focusing on the most critical issues first, ensuring resources are wisely used where they’re most needed. It acts like a guide, helping teams prioritize tasks that prevent the biggest risks and keep operations running smoothly.
It also helps teams plan ahead with preventive maintenance. By looking at potential problems early on, they can set up schedules and procedures to fix issues before they become costly breakdowns. This proactive approach saves money and keeps equipment working well over time.
When it comes to predictive maintenance, FMECA is invaluable. It calculates the chances and impacts of potential failures, letting teams use predictive maintenance strategies effectively. By catching problems before they happen, companies can reduce unexpected downtime and keep things moving.
On top of that, FMECA also helps manage spare parts better. It pinpoints which parts are most likely to fail, and teams can make sure they have what’s needed without stocking too much. This saves money and makes sure downtime from waiting on parts is minimal.
It also helps decide the best times for maintenance. It lets you figure out which failures are most critical, companies can decide when to service equipment to balance costs and reliability. This smart planning keeps things running smoothly and extends the life of equipment.
How CMMS Helps with FMECA Analysis?
CMMS plays a crucial role in supporting Failure Modes, Effects, and Criticality Analysis (FMECA) by providing a structured framework for managing maintenance activities and data.
Here are key ways CMMS contributes to effective FMECA analysis:
Data Management:
CMMS centralizes maintenance data, including equipment histories, work orders, and maintenance logs. This organized data repository facilitates easy access to information needed for conducting FMECA, such as past failure modes, maintenance activities, and their effects.
Risk Assessment:
CMMS integrates with FMECA by enabling users to categorize equipment failure modes based on criticality levels. Maintenance teams can assess risks more accurately by leveraging CMMS to track failure probabilities, consequences, and the likelihood of detection.
Scheduled Maintenance:
CMMS supports preventive maintenance scheduling, ensuring that critical equipment is regularly inspected and maintained. By aligning scheduled maintenance tasks with FMECA findings, organizations can proactively address high-risk failure modes and mitigate potential operational disruptions.
Workflow Automation:
CMMS automates workflows for maintenance tasks, from work order generation to completion. This automation streamlines the implementation of FMECA recommendations, improving response times to identified risks and reducing downtime.
Reporting and Analysis:
CMMS generates comprehensive reports and analytics on equipment performance, maintenance history, and failure trends. These insights empower maintenance managers to refine FMECA strategies continuously, optimizing resource allocation and enhancing system reliability.
Conclusion
FMECA is a powerful tool for enhancing the reliability and safety of systems across various industries. Its applications in maintenance management make it an invaluable methodology for professionals aiming to improve system reliability and safety. Understanding and implementing FMECA can lead to more effective maintenance strategies, reduced downtime, and improved overall system performance.
Wanted to know more? – Connect with our expert now.