Asset tracking in the oil and gas industry is a complex task due to the vast infrastructure, hazardous environments, and high-value equipment spread across multiple locations. Traditional tracking methods fail to provide real-time visibility, leading to operational inefficiencies, compliance risks, and unplanned downtime. A comprehensive and systematic asset management system is critical for ensuring equipment reliability, optimizing maintenance workflows, and reducing unnecessary costs.
CMMS software streamlines asset tracking by centralizing data, automating maintenance scheduling, and integrating IoT-based monitoring. It enhances asset utilization, prevents failures, and ensures regulatory adherence by offering real-time insights into equipment performance. Implementing CMMS helps oil and gas companies achieve a proactive approach to maintenance, reducing risks and improving long-term operational efficiency.
Asset Tracking Challenges in the Oil and Gas Industry
Asset tracking in oil and gas requires monitoring complex machinery, pipelines, offshore platforms, and mobile equipment across widely dispersed sites. High equipment costs, harsh environments, and strict regulations demand accurate, real-time tracking to avoid unplanned shutdowns and financial losses.
Manual logs and fragmented software often create data inconsistencies and slow down decision-making. Without a unified system for various asset types—rotating equipment, static infrastructure, and digital sensors—maintenance teams face delayed inspections, lost records, and inaccurate inventory forecasts that reduce overall productivity and compliance.
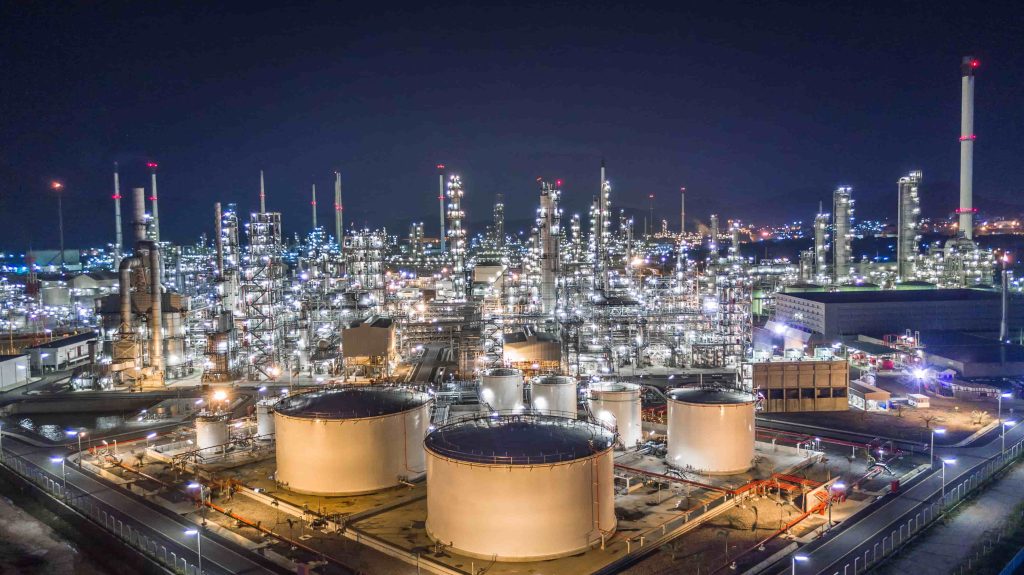
- Remote and Harsh Environments Increase Tracking Complexity – Equipment located in offshore rigs, deep-sea drilling sites, and remote onshore fields often lacks real-time monitoring, making asset visibility a challenge.
- Disconnected Systems Cause Data Inconsistencies – Many companies operate with standalone spreadsheets or legacy systems that do not synchronize asset information, leading to gaps in maintenance records and inaccurate reporting.
- Regulatory Compliance Requires Accurate Documentation – Failing to track inspection schedules, safety certifications, and maintenance logs can result in non-compliance with API, OSHA, and ISO standards, exposing companies to legal and financial risks.
- Unplanned Downtime Disrupts Operations – Without real-time asset tracking, maintenance teams rely on reactive strategies, increasing the likelihood of sudden equipment failures that halt production.
- Lack of Predictive Maintenance Leads to Premature Failures – Tracking asset health manually or through outdated systems prevents companies from implementing condition-based maintenance, reducing the operational lifespan of critical machinery.
- Unauthorized Asset Movement Creates Security Risks – Mobile equipment such as drilling rigs, transport vehicles, and generators are difficult to monitor without GPS-enabled asset tracking, increasing the risk of theft or misuse.
- Escalating Maintenance Costs Due to Poor Tracking – Without structured tracking, unnecessary repairs, duplicate maintenance efforts, and emergency replacements increase operational costs significantly.
How CMMS Software Resolves Asset Tracking Challenges?
Oil and gas companies require a robust digital solution to streamline asset tracking, enhance maintenance workflows, and ensure compliance. CMMS software offers a centralized system to automate maintenance, track real-time asset performance, and reduce operational risks. Its integration with IoT sensors, predictive analytics, and mobile accessibility enables data-driven decision-making and operational efficiency.
1. Centralized Asset Data Management
Oil and gas operations involve a vast number of assets, from drilling rigs to pipelines and processing units. Without a centralized system, asset data is often scattered across spreadsheets, legacy software, or even paper-based logs, leading to inefficiencies and inconsistencies. A CMMS consolidates all asset-related information into a single platform, providing real-time access to maintenance history, performance metrics, and lifecycle status. This improves asset traceability, ensures compliance with industry regulations, and enables informed decision-making for maintenance planning.
- Tracks asset location, operational status, and usage history.
- Stores digital records of equipment manuals, warranties, and service logs.
- Eliminates redundant data entry and ensures accuracy across departments.
2. Automated Preventive and Predictive Maintenance
Equipment failures in oil and gas operations can lead to catastrophic consequences, including production loss, environmental hazards, and safety risks. Relying on reactive maintenance increases downtime and repair costs.
A CMMS enables automated scheduling of preventive maintenance based on runtime, sensor data, or predefined intervals, ensuring critical assets receive timely servicing. With predictive analytics, it helps identify early signs of wear and tear, reducing the risk of unexpected breakdowns.
- Triggers maintenance work orders based on real-time asset conditions.
- Reduces reliance on manual scheduling, minimizing human oversight.
- Lowers downtime by identifying failure patterns before they escalate.
- Optimizes resource allocation for maintenance teams and spare parts.
3. Regulatory Compliance Tracking
Oil and gas companies must adhere to strict safety and environmental regulations, requiring meticulous record-keeping for inspections, audits, and certifications. Non-compliance can lead to severe financial penalties, operational shutdowns, and reputational damage. CMMS software automates compliance tracking by maintaining detailed logs of inspections, safety checks, and asset certifications. It ensures that all regulatory deadlines are met, preventing last-minute audits and unexpected legal consequences.
- Maintains a digital database of compliance records for audits.
- Sends automated reminders for upcoming inspections and certifications.
- Generates detailed reports for regulatory authorities in real time.
- Reduces the risk of non-compliance fines and operational disruptions.
- Ensures adherence to API, OSHA, ISO, and local industry standards.
4. Integration with IoT and GPS for Real-Time Monitoring
Real-time asset monitoring is essential for tracking the condition and location of equipment, especially in remote and offshore sites. Manual tracking methods provide delayed or inaccurate data, making it difficult to optimize asset utilization. CMMS software integrates with IoT sensors and GPS tracking systems, enabling real-time data collection on equipment health, operational status, and geolocation. This allows maintenance teams to take proactive actions, preventing equipment failures and unauthorized asset movement.
- Captures sensor data such as vibration, temperature, and pressure levels.
- Provides GPS tracking for mobile assets like drilling rigs and transport units.
- Sends automated alerts when asset conditions exceed safe operating thresholds.
- Supports predictive maintenance by analyzing real-time performance trends.
- Enhances security by detecting unauthorized asset movement.
5. Optimized Spare Parts and Inventory Management
Managing spare parts inventory is a critical challenge in the oil and gas sector, where unplanned shortages can delay maintenance and disrupt production. Overstocking, on the other hand, ties up capital and leads to storage inefficiencies. A CMMS optimizes spare parts management by tracking inventory levels, automating reorder processes, and ensuring that the right parts are available when needed. It prevents maintenance delays, reduces costs, and improves overall asset reliability.
- Tracks inventory levels in real-time to prevent stock shortages.
- Automates reorder requests based on usage patterns and lead times.
- Reduces overstocking of rarely used or obsolete spare parts.
6. Seamless Integration with ERP and SCADA Systems
A standalone CMMS may not be enough to fully optimize asset management without integrating with enterprise resource planning (ERP) and supervisory control and data acquisition (SCADA) systems. ERP integration helps align asset management with procurement, budgeting, and financial reporting, while SCADA integration provides real-time operational insights. By connecting these systems, CMMS enhances efficiency, ensuring seamless data flow across departments and improving overall decision-making.
- Syncs with ERP for procurement and financial tracking.
- Integrates with SCADA for live equipment performance monitoring.
- Enhances cross-department collaboration with unified asset data.
Tips to Choose and Implement the Right CMMS Software for Asset Tracking
Selecting the right CMMS software is crucial for maximizing asset efficiency and ensuring seamless tracking. Oil and gas companies need a solution that aligns with operational needs, integrates with existing systems, and provides scalability. A structured implementation strategy ensures successful adoption and long-term benefits. This are some of the considerations you must take care:
- Scalability – Choose a solution that grows with operational expansion.
- Integration Capabilities – Ensure compatibility with ERP, IoT, and SCADA systems.
- Mobile Accessibility – Opt for cloud-based CMMS for remote access.
- Customization Options – Look for software that adapts to industry-specific workflows.
- User-Friendly Interface – Ensure easy adoption with minimal training requirements.
- Automated Maintenance Scheduling – Prioritize software with AI-driven predictive maintenance.
- Regulatory Compliance Support – Ensure automated tracking of inspections and certifications.
- Vendor Support and Training – Select a provider offering ongoing technical assistance.
Putting it to the end
Asset tracking in the oil and gas sector plays a critical role in maintaining operational efficiency, safety, and compliance. CMMS software provides a structured method to monitor and manage assets, helping to reduce unplanned downtime and improve overall asset performance. Companies can experience more organized workflows, lower maintenance expenses, and longer asset lifecycles with proper asset tracking practices.
Selecting the right CMMS involves careful planning to ensure proper integration with current systems and alignment with business objectives. A well-executed implementation leads to better maintenance scheduling, improved decision-making, and optimized operations. For further guidance on selecting and deploying a CMMS solution for your operations, contact contact@terotam.com.